Anodizing involves creating an artificial oxide layer on the surface of a non-ferrous alloy, aluminum-based alloys being the most traditional, and hard coat, also known as Type III anodizing, provides the most durable layer of them all (between 400 and 600HV on the Vickers scale). Also known by its U.S. military specification of “MIL-PRF-8625F,” the process can also make the surface electrically resistant, causing it to act like an insulator. Hardcoat anodize on Xometry's platform conforms to MIL-A-8625/MIL-PRF-8625, Type III, Class 1/2 with finishing certs provided. To learn more about this fabricating process and how it works, read on.
What is Hard Coat Anodizing?
Hard coat anodizing is a fabrication and finishing process used on alloy metals to make them stronger and more durable. It creates a protective oxide layer that’s .002" thick—sometimes double the thickness of the layer made with regular anodizing. It’s used a lot on aluminum and gives the material more resistance against corrosion, scratches, and wear and tear. It’s a particularly helpful process for parts exposed to the elements and extreme weather conditions.
Surfaces that have been hard coat anodized can be colored using dyes, but if aesthetics are more important than durability to you, go for something like the Type II sulfuric acid method, which allows for more colors and is easier to dye. In addition to aluminum, the hard coat method can also be used on materials like titanium and magnesium, and makes their surface non-conductive and in some cases, very pretty.
It’s no surprise that this process is used all the time in the optics, defense, aerospace, food service, architectural, and medical industries. But, like every manufacturing method, there are a couple of downsides you might want to keep in mind. First of all, the part ’s fatigue strength will likely be reduced. If your part will be exposed to cyclic loading, you might want to consider Type I or Type II anodizing. Also, as mentioned briefly, hard coat anodizing won’t give you as many color options as other types will, and that’s because the oxide layer is very thick, making it darker and almost bronze-gray in color. With hard-coat anodized parts, you’ll have to seal the surface if you want to dye it, which will likely reduce its abrasion properties.
How it Works
There are a few steps to the process, starting with cleaning the part and etching off its natural oxide layer. You should then be left with a clean, uniform surface to get started on. The part is then dunked in a temperature-regulated acidic electrolyte liquid (usually sulfuric acid) and acts as the anode while it's connected to a positive electrode. To complete the electrical circuit, a cathode that’s made from an unreactive material needs to be inside the bath.
This type of anodizing requires a higher voltage than the others—it usually starts at around 25V DC and goes up to 60–100V as it goes on—because the oxide layer will become less conductive as it gets thicker, so turning up the voltage will make up for this. You can also control the thickness of the new layer by adjusting things like the temperature of the electrolytes, the voltage, the concentration of acid, and how long it’s in there. This is an image of an anodized aluminum part we made here at Xometry:
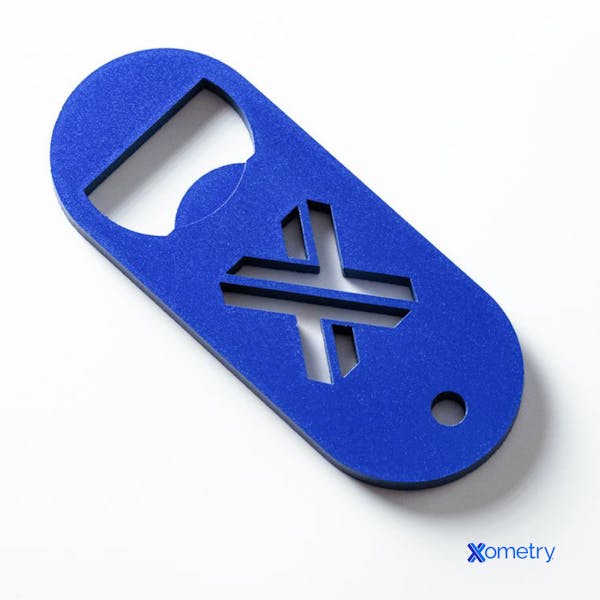
Frequently Asked Questions on Hard Coat Anodizing
How long will the new coating last?
As this is the toughest coating method of three, it can last anywhere from a few years to several decades. Obviously, that depends on what the part will be used for, but hard coats are designed to withstand all sorts of environments and provide excellent resistance to abrasion.
What equipment do I need for the process?
We briefly mentioned some of the equipment above, but to clarify what you need for the anodizing process, we’ve listed it below:
- An electrolyte tank (acid-resistant)
- A cathode (it can be an unreactive material like graphite or lead sheeting)
- A power supply that can handle the voltage
- Some form of air agitation, like nozzles to create turbulence in the tank and increase the quality of the coating
- A temperature control system like a water- or air-cooled chiller that can remove the excess heat that builds up in the tank during the process
- Extra equipment that will help you with both pre- and post-processing, like degreaser, etchant, dye, and sealing tools
How is this type of anodizing sealed?
You can use hydrothermal sealing, which involves dipping the part in hot water (around 95–100°C) to close the pores and give it more corrosion resistance. There’s also precipitation sealing, which uses chemicals to add a barrier to the surface, sealing it right up.
How Xometry Can Help
We have a good range of anodizing services available for all your manufacturing needs, including Type II hard coat and Type III with PTFE. If you’d like to know more about these options or have any other questions relating to anodizing, you can reach out to one of our Xometry representatives, who will be happy to assist you. You can also get your project off the ground today by requesting a free, no-obligation quote on our Instant Quoting page for anodizing, or any of our other offerings like CNC machining, 3D printing, and laser cutting.
Disclaimer
The content appearing on this webpage is for informational purposes only. Xometry makes no representation or warranty of any kind, be it expressed or implied, as to the accuracy, completeness, or validity of the information. Any performance parameters, geometric tolerances, specific design features, quality and types of materials, or processes should not be inferred to represent what will be delivered by third-party suppliers or manufacturers through Xometry’s network. Buyers seeking quotes for parts are responsible for defining the specific requirements for those parts. Please refer to our terms and conditions for more information.
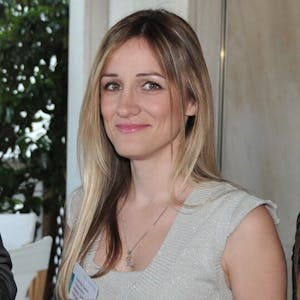