Hole drill electrical discharge machining (EDM) is a manufacturing service that just seems to keep on growing in popularity. It’s a great way of making cooling channels in turbine blades, starter holes for wire EDM cutting, and even removing broken taps and drills from machinery that’s being manufactured or reworked. This article will explain the hole drill EDM process and how it’s used.
What is Hole Drill EDM?
As the name suggests, hole drill EDM is a type of electrical discharge machining that’s intended to drill small, yet deep, holes. These holes can have diameters as small as 0.065 mm and be as deep as 1 m—basically 250 times the hole’s diameter. That’s almost impossible to beat using other methods. It uses an electrode, usually made of tungsten, graphite, brass, or copper, which is essentially a hollow tube that allows dielectric fluid to flow through it. The electrode and the workpiece are both connected to a power source—the electrode is usually negatively charged, and the workpiece is positively charged.
As the electrode nears the workpiece, sparks will start to appear, and these can reach temperatures between 8,000°C and 12,000°C, and rates between 500 and 30,000 sparks per second, although only one will hit the workpiece at a time. The fluid, which stabilizes the electrode, and clears away debris and eroded material, is pumped through the electrode to prevent short circuits and withstand the electrical flow until the voltage reaches a point high enough to generate a spark. Each spark vaporizes and erodes a tiny part of the workpiece; so as they continue, the hole gets deeper. The image below shows how the process works.
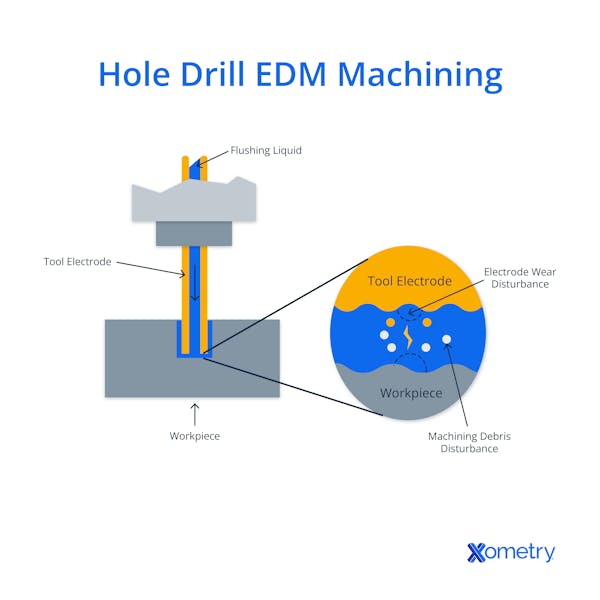
Hole Drill EDM Machining
This machining process is good for drilling holes through curved surfaces and with hard-to-machine metals like hardened steel, stainless steel, or tungsten carbide. It can be used to drill “through holes” or “blind holes,” although sinker EDM machines are better for the latter because hole drill EDM machines can’t always make flat-bottomed holes.
Frequently Asked Questions on Hole Drill EDM
How accurate is hole drill EDM?
Hole drill EDM is perhaps the most accurate process, especially for making small holes. Using a hole that’s 150 mm deep and 1 mm wide as an example, EDM can hold tolerances as small as +0.0025 mm on the hole diameter and +0.025 mm on its straightness. It all boils down to the fact that this process doesn’t use drill bits, and bits that small would very likely bend, deflect, or break during the drilling process.
Does hole drill EDM have any drawbacks?
Although speeds are continually improving, the hole drill EDM process is slow, sometimes taking a good few minutes for a single hole. This means that, while it’s super accurate, it won’t be suitable for high-volume production projects. Other drawbacks include the high purchase, operating, and maintenance costs, and it consumes a fair bit of energy, too. It’s also somewhat limited to conductive materials; it can’t and shouldn’t be used on plastics or composites.
How Xometry Can Help
With all of its benefits, EDM is being used more and more in almost every industry. This is a process we’re very familiar with here at Xometry, and we offer many related services, like sinker EDM and wire EDM. You can get a free, no-obligation quote quickly by uploading your design to our Instant Quoting page or contacting one of our representatives if you have any EDM-related queries. In case you didn’t know, Xometry also offers a large array of other manufacturing services, like 3D printing, and CNC machining, which you can just as easily get a quote for.
Disclaimer
The content appearing on this webpage is for informational purposes only. Xometry makes no representation or warranty of any kind, be it expressed or implied, as to the accuracy, completeness, or validity of the information. Any performance parameters, geometric tolerances, specific design features, quality and types of materials, or processes should not be inferred to represent what will be delivered by third-party suppliers or manufacturers through Xometry’s network. Buyers seeking quotes for parts are responsible for defining the specific requirements for those parts. Please refer to our terms and conditions for more information.
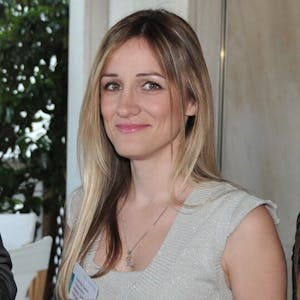