When deciding whether to use HDPE or Delrin for an application, it is important to understand the differences between the two materials. HDPE (high-density polyethylene) is a thermoplastic that is moisture resistant, has high stiffness, high impact strength, and is relatively cost-effective. Delrin® is the brand name for acetal homopolymer. It is an engineering plastic known for its strength and stiffness, excellent dimensional stability, and low friction properties. HDPE is commonly used for bottles, pipes, and containers, while Delrin is most often used in automotive components and medical instruments.
HDPE is usually manufactured using injection molding, while Delrin can be injection molded or extruded. Both HDPE and Delrin are versatile materials that offer many benefits. HDPE, however, is typically used for applications requiring greater chemical resistance, and Delrin for applications needing high tensile strength. Ultimately, the choice between HDPE and Delrin must be based on the specific needs of the application. In this article, we’ll discuss HDPE vs. Delrin in more detail, so you can decide which material is best for your project.
What Is HDPE?
HDPE (high-density polyethylene) is a thermoplastic material with high stiffness, impact strength, and resistance to moisture absorption. HDPE offers many additional advantages, including low cost, durability, chemical resistance, and good thermal insulation.
HDPE parts are usually manufactured using injection molding, although they can also be extruded or thermoformed. HDPE is available in a variety of colors, which can make it useful for aesthetic applications. HDPE is most commonly used for bottles, pipes, and containers. It can also be used in automotive components, medical instruments, and consumer goods. For more information, see our guide on All About High Density Polyethylene.
What Is Delrin?
Delrin is a trademarked brand name for acetal homopolymer. It is an engineering plastic that offers excellent dimensional stability, low friction, and high strength and stiffness making it a versatile material for many different industries. Delrin can be injection molded or extruded. It has excellent wear resistance, making it a good choice for applications where parts may be subject to friction or wear. Delrin is also available in a range of colors, making it ideal for aesthetic applications. It is often used in applications requiring high tensile strength, such as automotive components, medical instruments, electronics enclosures, and many other products.
HDPE vs. Delrin: Applications and Uses
Both HDPE and Delrin have their advantages and disadvantages, making them suitable for various applications. HDPE is typically used for applications requiring greater chemical resistance, while Delrin is usually chosen for applications needing high tensile strength and low friction. HDPE is commonly used to create bottles, pipes, and cutting boards, and can also be used in automotive applications (many of the moving mechanisms such as gears and bearings in a car are made of HDPE), medical instruments, and food packaging products.
Delrin is usually used for applications requiring high tensile strength, such as automotive components, medical instruments, electrical enclosures, and many other products.
HDPE vs. Delrin: Physical Properties
Table 1 below compares the properties of HDPE and Delrin:
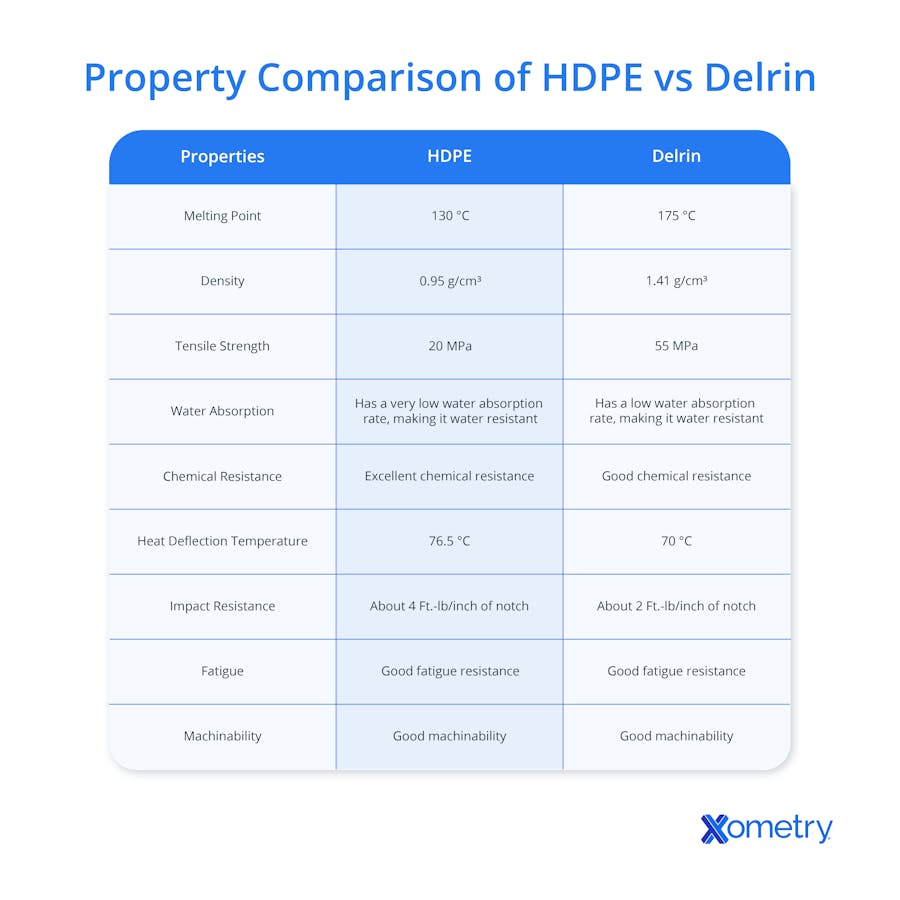
HDPE vs. Delrin: Recyclability and Sustainability
Both HDPE and Delrin can be recycled. However, they are both petroleum products — making them non-renewable and ultimately unsustainable. HDPE is the most widely recycled plastic in the world, as it is one of the easiest types of plastic to recycle. HDPE can be recycled up to ten times, making it an ideal choice for applications requiring large quantities of material. It is often used in the manufacture of products such as pallets, fencing, and crates. Recycled HDPE can also be used to make plastic lumber, which can be used in many different applications. HDPE is also frequently used in the production of textiles and carpets, as well as recycled plastic bags. Figure 1 shows examples of recyclable products made with HDPE:
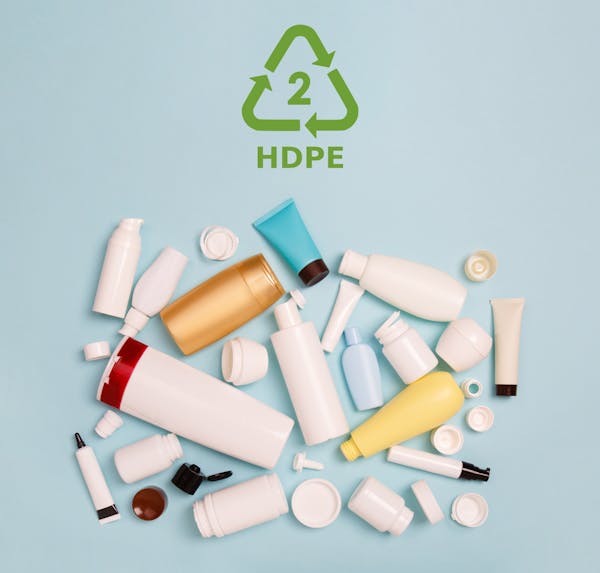
Delrin, on the other hand, can only be recycled into a variety of useful products up to five times. Delrin can also be re-extruded so that it can be re-used even in applications requiring high tensile strength.
HDPE vs. Delrin: Cost
HDPE is generally less expensive than Delrin, due to its lower production costs. The cost of HDPE and Delrin can vary significantly, depending on the specific product form. HDPE costs about $0.90-1.56 per kg, while Delrin is somewhere in the range of $2.40-3.70 per kg or higher.
Alternative Materials to HDPE and Delrin
Other materials that can be used as alternatives to HDPE and Delrin include:
- PEEK: Polyether ether ketone is a semi-crystalline thermoplastic that offers excellent chemical and thermal resistance, as well as superior mechanical strength. PEEK is lightweight and has excellent wear resistance, making it a viable alternative to HDPE and Delrin in many applications.
- Nylon: Nylon is a strong and versatile thermoplastic that provides excellent wear resistance, making it ideal for many applications. It is also lightweight and easy to machine, making it an attractive alternative to HDPE and Delrin.
- ABS: Acrylonitrile butadiene styrene is a high-strength-to-weight ratio thermoplastic with excellent mechanical and thermal properties, making it a cost-effective alternative to HDPE and Delrin. ABS is also resistant to many acids, bases, and other chemicals, making it an ideal material for applications that require superior chemical resistance.
- Ultem®: Ultem® is a high-performance thermoplastic with superior heat and flame resistance, making it a good alternative to HDPE and Delrin if cost is not an issue. It also offers great strength and stiffness, making it an excellent choice for applications that require high strength.
- Polycarbonate: Polycarbonate is a thermoplastic polymer with excellent tensile strength and impact resistance. It is also resistant to many chemicals, making it a good material for applications requiring superior chemical resistance. Polycarbonate also has a high strength-to-weight ratio, making it an attractive alternative to HDPE and Delrin.
Summary
This article presented HDPE and Delrin materials, explained what they are, and discussed how each are used in manufacturing. To learn more about HDPE and Delrin, contact a Xometry representative.
Xometry provides a wide range of manufacturing capabilities and other value-added services for all of your prototyping and production needs. Visit our website to learn more or to request a free, no-obligation quote.
Copyright and Trademark Notices
- Delrin® is a trademark of Dupont Polymers, INC.
- Ultem® is a trademark and brand of SHPP Global Technologies B.V., Bergen OP ZOOM, NL.
Disclaimer
The content appearing on this webpage is for informational purposes only. Xometry makes no representation or warranty of any kind, be it expressed or implied, as to the accuracy, completeness, or validity of the information. Any performance parameters, geometric tolerances, specific design features, quality and types of materials, or processes should not be inferred to represent what will be delivered by third-party suppliers or manufacturers through Xometry’s network. Buyers seeking quotes for parts are responsible for defining the specific requirements for those parts. Please refer to our terms and conditions for more information.
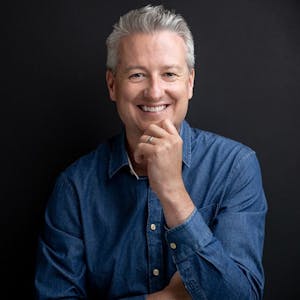