Normalizing is a heat treatment process that is akin to annealing but with lower standards of control and a somewhat lesser effect on the microstructure of the metals. It involves raising the temperature of a metal component that has either undergone heat/quench hardening or work hardening. It is held at that temperature for a prescribed and approximate period and then naturally cooled back to ambient in open air, room temperature. The temperature required for normalizing is above the critical and glass transition temperatures, but well below the melting point.
This approach is used to relieve internal stresses and reduce the hardness of materials in a relatively quick and simple way. The process allows further work to be undertaken more easily, or to increase the toughness of the material.
Both of these outcomes are achieved by recovering the ductility/malleability of the material that has been lost through work or thermal hardening. This results from relieving the harder and more brittle alterations to the crystalline structure that have taken place, reverting the matrix to a form that is closer to the fully soft/ductile condition.
This article will discuss normalizing, its purpose, how it works, its applications, and the stages.
What Is Normalizing?
Normalizing is a simple heat treatment process applied to metals, particularly steel and its alloys but also various others. It helps to improve their mechanical properties, reduce internal stresses, and achieve a more uniform and refined microstructure. Normalizing involves three main stages, each performed in a moderately controlled manner: heating, soaking (in a maintained, elevated temperature), and cooling.
Specific parameters of the normalizing process, including heating temperature and soaking time, are dependent on: the material type, its initial hardness condition, and the desired degree of change in its properties. Normalizing is widely employed in automotive, aerospace, construction, and manufacturing to prepare materials for further processing and to achieve desired mechanical characteristics.
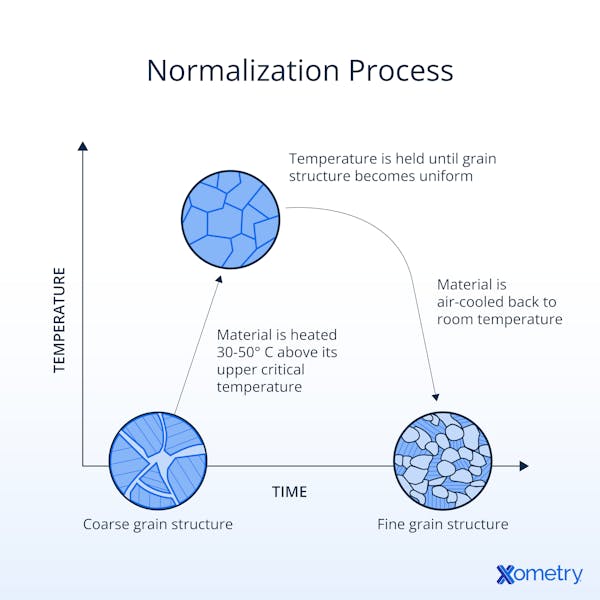
What Is Normalizing Also Known As?
Normalizing is often named interchangeably with annealing. Though the processes use the same basic mechanisms, normalizing has a generally lesser effect on the resultant properties. Its intervention is less controlled, particularly in the cooling phase, during which normalizing involves the natural pace of convective/radiative cooling in an ambient atmosphere, without any effort to restrain or reduce that rate.
What Is the Purpose of Normalizing?
Normalizing regularizes the grain structure of the material, resulting in smaller and more uniform grains throughout and improved anisotropy. This alters mechanical properties, increasing strength and toughness while reducing hardness. Normalizing helps relieve internal stresses that develop during previous manufacturing processes, particularly bending, forging, and welding. This reduces the risk of distortion or cracking in the material, in the “worked” zone which will have become relatively harder and more brittle.
Normalized materials are often easier to machine, making them more efficient and cost-effective for subsequent manufacturing processes. In particular, the hardness variations that result from local work hardening can be a barrier to consistent machining processes. Such hardness can also greatly reduce machined part quality and tool life. The process improves the homogenization of the material's composition. It ensures a more consistent distribution of alloying elements throughout the structure and reduces the uneven distribution of precipitates that can badly affect regional properties. Normalizing can return the materials to which it's applied to a more native ductility level, making subsequent processes easier and lowering the risk of fracture. Once normalized, materials are often more receptive to subsequent heat-treatment processes, allowing for more precise control over their final properties.
Why Is Normalizing Important in Manufacturing?
Normalizing is important in manufacturing because it improves the mechanical properties of materials, reduces internal stresses, and refines the microstructure. This enhances the material's strength, toughness, and machinability, making it suitable for various manufacturing processes. Normalizing also promotes consistency and quality control in production.
Does Normalizing Materials Increase Ductility?
Yes, normalizing materials can increase ductility. Normalizing refines the microstructure of materials, leading to smaller and more uniform grain sizes. This finer grain structure enhances ductility, making the material more malleable and easier to deform without fracturing.
To learn more, see our guide on the Definition of Ductility.
What Are the Different Types of Normalizing?
There are several variations and techniques of normalizing, each tailored to specific materials and desired outcomes. These types are listed below:
- Full Normalizing: The material is heated to a temperature slightly above its upper critical temperature. It is then soaked for a period that is often derived by trial, and then allowed to cool naturally, in still, ambient air. This process alters and refines the grain structure and relieves internal stresses, most commonly for low-carbon steels.
- Process Normalizing: A variation in which the cooling stage is accelerated by immersing the material in a medium like water or oil. This results in a finer grain structure and increased hardness compared to full normalizing. Note the difference between this and heat/quench hardening is that the peak temperature of the part is generally lower when the process normalizes.
- Isothermal Normalizing: This involves cooling the material to a specific intermediate temperature range, typically targeting the pearlite transformation range. The material is then held at this temperature before being cooled further. It is used to achieve a finer grain and higher strength.
- Air Normalizing: This process is essentially a common terminology used to identify a process that is identical to full normalizing.
How Does Normalizing Work?
Normalizing is used to refine the microstructure and improve the mechanical properties of materials, particularly steel and its alloys.
The diverse, coarse, and often anisotropic grain structure of a material that resulted from prior manufacturing processes (particularly cold working) is refined to a moderately controllable degree. Internal stresses are relieved, reducing the risk of post-machining deformation or fracture. The mechanical properties are improved, increasing strength, toughness, and ductility. The material is prepared for subsequent manufacturing processes or heat treatments, either reducing the stress and effort of further forming or returning the structure to a known and consistent quality that existed prior to heat treatment/hardening.
To learn more, see our guide on Steel Microstructure.
When To Normalize Materials?
Materials are normalized for a spectrum of reasons that are highly dependent on the specific material, its pre-existing condition, and the properties for the intended application or subsequent processes. Materials that have been heat/quenched for hardening will exhibit high internal stresses and brittleness. Normalizing can relieve these stresses and enhance toughness, at the cost of reduced hardness. Forged or welded materials often have irregular and highly regionalized grain structures and internal stresses, due to non-uniform heating. Where that irregularity/anisotropy is not a target of the production (as it can be in forgings), normalizing can revert the grain structure to the natural state and relieve stresses. Materials with uneven composition or inconsistent properties may benefit from normalizing to achieve a more uniform distribution of alloying elements and mechanical properties. This can be because of thermal, work, or other processes creating uneven condensates in some regions, dramatically altering local properties. Normalizing can improve the machinability of materials by essentially softening them, rendering them easier to machine, shape, or fabricate, easing manufacturability. Normalizing is often used as an intermediate step before other heat treatment processes such as hardening. It prepares the material for these subsequent treatments, improving the uniformity of the final treatment. Normalizing is often used to ensure consistent material properties in production, promoting better quality control and minimizing inter- and intra-batch variations in properties.
What Are the Applications of Normalizing?
Normalizing is a widely used heat-treatment process with applications across various industries. It is employed in the production of steel to refine grain structures, relieve internal stresses, and optimize uniformity and mechanical properties. It is crucial for manufacturing components in automotive, construction, and machinery. Forged materials often undergo normalizing after one or more forging steps to eliminate irregular grain structures and internal stresses, enhance strength, and restore toughness. Normalizing is used to relieve stresses and refine the microstructure of welded materials, ensuring weld integrity, uniformity of properties across the weld zone, and prevention of fracture.
Aerospace components, such as landing gear and engine parts, undergo normalizing to meet stringent strength and durability requirements. Durability is restored after forming, by normalizing. Normalizing is applied to automotive components like crankshafts and axles to enhance their toughness and performance. Tools and dies are often normalized to improve durability and wear resistance. Steel beams, rods, and structural components are normalized to meet safety and durability standards in construction. Components for the oil & gas industry, such as drill-string components and valves are normalized for improved toughness performance and longevity.
What Are the Different Stages of the Normalizing Process?
The different stages of the normalizing process are listed below:
1. The Recovery Stage
The recovery stage is the initiating phase of the normalizing process. It occurs when the metal is heated close to the upper critical temperature. The material is heated to a temperature slightly above its upper critical temperature, which is specific to the material type and composition. This is between 815–925 °C for most steels. During this heating phase, recovery begins. This sees progressive relief of defects and irregularities in the material's microstructure, resulting from prior manufacturing processes. These defects typically consist of dislocations, vacancies, and grain boundaries. As the material heats, the thermal energy allows the atoms in the crystal lattice to move more freely. This movement enables the reformation of many microscopic defects, relieving internal stresses and fracture initiation points.
The recovery stage is to prepare the material for subsequent transformations during the normalizing process.
2. The Recrystallization Stage
The recrystallization stage is the most critical phase in the normalizing process after recovery has commenced. During recrystallization, the microstructure of the material undergoes significant changes by grain boundary dissolution and atomic diffusion.
The material is further heated to a temperature just above its upper critical temperature, which is an intrinsic property of each metal and alloy and varies greatly between metals. As the material reaches the recrystallization temperature, new grains begin to form within the existing microstructure. These new and smaller grains progressively consume all the existing grain structure in a new and more uniform matrix. Recrystallization helps eliminate the effects (and defects) of prior forming and heat/quenching. It replaces the deformed and disrupted grains with a new, strain-free structure with better ductility and toughness.
The recrystallization stage is essential for normalizing because it refines the grain structure and enhances its mechanical properties, eliminating the negative consequences of prior processing.
3. The Grain-Growth Stage
The grain-growth stage follows the recrystallization stage. During this stage, the newly formed grains within the material continue to grow and evolve in size, contributing to the final microstructure of the material. Grain growth will continue at a diminishing pace, as the heat is maintained. This is the soak period and its effect on the microstructure can be more significant than the prior phases.
After the material has undergone initial recrystallization it is held at elevated temperature. In the grain-growth stage, the small, newly formed grains that resulted from recrystallization continue to grow by consuming adjacent grains. The grain-growth stage allows for the development of a more uniform and consistent grain size throughout the material, resulting in larger, strain-free grains. The final microstructure achieved during the grain-growth stage depends on factors such as: the material type, initial condition, the stable temperature, and the hold or dwell period. As the heat is removed, the grain-growth stage will slow and plateau as a result of air cooling, which progressively diminishes the atomic movements required for crystal matrix alterations.
The grain growth stage is critical for the subsequent mechanical properties. A more uniform and controlled grain-size distribution can result in improved material performance and will result from sufficient dwell time.
How Long Does the Normalizing Process Take?
Typically, the heating and soaking stages of normalizing may take anywhere from a few minutes to several hours, depending on: the degree of lattice adjustment required, the thickness of the section, and the properties of the material. The cooling stage is considerably slower than quenching but still relatively fast.
The heat-up time will vary depending on the material's thickness and the heating method used. It may take anywhere from a few minutes to a few hours. Soaking times can range from a few minutes to several hours, again depending on the desired properties, the material, and its section thickness. The cooling stage, which is typically done in still air, can take several hours to return the material to room temperature.
The total duration of the normalizing process, from heating to cooling, can vary from a few minutes for small parts, up to several hours for larger parts and thicker sections.
What Are the Metals Used for Normalizing?
Normalizing is applicable to a wide range of metals, but it is most commonly used for ferrous materials. Normalizing various grades of steel such as carbon steel, alloy/tool steels, and stainless steel is widely used. Cast iron is normalized (after casting) to improve its machinability and reduce internal stresses. Some copper alloys, such as brasses and bronzes are susceptible to work hardening, so they must undergo normalizing to improve their mechanical properties. While less common, certain aluminum alloys can benefit from normalizing in exactly the same way as other metals. Some nickel-based alloys, such as Inconel® and Monel®, can benefit from normalization. Normalizing is not as common for titanium alloys as other heat-treatment processes, but it can be effective, particularly in forged parts.
How Does Tool Steel React to Normalizing?
Tool steel is greatly affected by normalizing, undergoing a range of beneficial changes. Normalizing refines the grain structure, forming smaller and more-uniform grains (which have certain associated mechanical properties), and making subsequent machining easier. Tool steel often experiences internal stresses due to various manufacturing processes. Normalizing helps relieve these stresses. Normalizing ensures a consistent and uniform material structure, improving quality in tool manufacturing.
Can Aluminum Be Normalized?
Yes. Aluminum can be normalized, although the process is not commonly applied. Aluminum alloys, including those used in aerospace and engineering applications, typically undergo different heat treatment processes to achieve desired properties. While not typically used for aluminum alloys, it may be applied in certain specialized applications or research scenarios in which specific microstructural changes are desired, such as for wire drawing.
To learn more, see our guide on the Physical Properties of Aluminum.
Can Normalizing Be Done to Brass?
Yes. Brass can be normalized, but the process for brass is different from that of ferrous metals due to a considerably lower critical temperature. Brass is heated to a temperature between 700–800 °C. Once the brass reaches the desired temperature, it is soaked at that temperature to ensure uniformity throughout the material. The brass is then allowed to cool in still air or at a controlled rate.
This process can be particularly useful when working with brass components that have undergone extensive deformation or machining, as it can reduce the risk of distortion and improve toughness.
To learn more, see our article on Brass Elements.
At What Temperature Is Normalizing Done?
The normalizing temperature is specific to each family of materials (pure metals and alloys). It is also varied according to the intended effect on the microstructure, in many cases. For steel, temperatures typically lie between 815–925 °C, depending on the carbon and other alloying agents. For cast iron, normalizing temperatures are higher than steel, generally between 870–940 °C. For copper alloys, the temperatures are generally between 700–800 °C. For aluminum alloys, if needed, temperatures are highly specific to the alloy's properties. For nickel alloys, Inconel® is normalized between 925-1010 °C, whereas Monel® is between 850–1050 °C. Normalizing of titanium alloys, when performed, is at 700-785 °C, though alloying elements can alter this significantly.
How Does the Color of Steel Change When Normalized?
During normalizing, the color of steel changes as it is heated, soaked, and cooled. Initially, it appears dull red, progressing to brighter red, orange, and yellow hues as it reaches the normalizing temperature. During cooling, it returns to its original gray or silver color.
How Many Times Can You Normalize Steel?
There is essentially no limit to the number of normalization cycles that a steel part can undergo if relief of process hardening is required after intermediate manufacturing stages. For example, when steel wire is drawn from large to small diameters, restoring the ductility after each drawing stage is necessary such that the next drawing stage can proceed without fracture.
Do You Quench After Normalizing?
No, normalizing applies heat and then a relatively slow cooling process, exposing the heated sample to ambient air to allow the temperature to fall naturally.
What Are the Advantages of Normalizing?
Normalizing offers several advantages in manufacturing metal parts, including:
- Improves mechanical properties by refining the microstructure, enhancing strength, toughness, and ductility.
- Relieves internal stresses created during manufacturing processes, reducing the risk of post-machining deformation or fracture.
- Promotes a uniform and fine-grained microstructure, resulting in greater material consistency and anisotropy.
- The improved uniformity and ductility of the material results in easier machining and fabrication.
- Ensures consistent material properties within and between batches.
- Prepares materials for subsequent heat treatments, improving the response to hardening and tempering.
What Are the Disadvantages of Normalizing?
While normalizing offers numerous benefits, it also has some limitations and potential disadvantages such as:
- Is primarily used for ferrous alloys like steel and cast iron.
- Requires significant energy to reach and maintain the high normalizing temperatures.
- Cooling in still air is slower than quenching, which can be a disadvantage in throughput or work in progress.
- Can result in slight dimensional changes in the material, particularly when non-uniform sections must be heated.
Is Normalizing Metal More Expensive Than Tempering?
No, normalizing is a less-controlled and less-refined process than tempering. It requires similar temperatures at the heating phase, but no enclosed or controlled cool-down equipment is required, so process times are lower allowing faster throughput and hence reduced cost.
How Common Is Normalizing?
Normalizing is a relatively common heat-treatment process, especially in industries in which steel and cast iron components are widely used. Its prevalence can vary depending on factors such as: the specific industry, the type of materials being processed, and the desired properties of the end products.
Normalizing is a standard practice in the production of various steel products, including: structural components, automotive parts, and machinery components. Forged and cast components often require the microstructural refinement and stress relief of normalizing. Welded materials benefit from normalizing to relieve stresses and improve the material's properties in the heat-affected zone. Steels used in tool and die manufacturing are typically normalized to enhance machinability between process stages and toughness in finished parts.
What Is the Difference Between Normalizing and Annealing?
Normalizing and annealing are both heat-treatment processes used to alter the microstructure and properties of metals, but they differ in their objectives and methods.
Normalizing aims to refine the grain structure, improve mechanical properties, and relieve internal stresses in the material. It produces a more uniform and fine-grained microstructure, enhancing strength and toughness.
Annealing similarly relieves internal stresses and improves grain structure and machinability. It allows greater time for grain growth than does normalization, due to the extended cooling period, additionally softening the material.
Summary
This article presented normalizing, explained it, and discussed its purpose and how it works. To learn more about normalizing, contact a Xometry representative.
Xometry provides a wide range of manufacturing capabilities and other value-added services for all of your prototyping and production needs. Visit our website to learn more or to request a free, no-obligation quote.
Copyright and Trademark Notices
- Monel® is a registered trademark of Special Metals Corporation.
- Inconel® is a registered trademark of Special Metals Corporation.
Disclaimer
The content appearing on this webpage is for informational purposes only. Xometry makes no representation or warranty of any kind, be it expressed or implied, as to the accuracy, completeness, or validity of the information. Any performance parameters, geometric tolerances, specific design features, quality and types of materials, or processes should not be inferred to represent what will be delivered by third-party suppliers or manufacturers through Xometry’s network. Buyers seeking quotes for parts are responsible for defining the specific requirements for those parts. Please refer to our terms and conditions for more information.
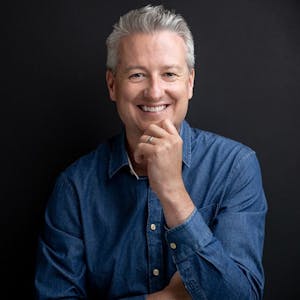