Polyetherketone (PEK) is a high-performance, semicrystalline thermoplastic with exceptional performance at higher temperatures. It has a continuous use temperature of up to 260°C and a melting point of 373°C. PEK has good fatigue and creep resistance across its entire usable temperature range. It also has excellent resistance to solvents, acids, and oils. PEK is non-toxic and poses no significant health risks. PEK is often used for gears, bearings, bushes, and other mechanical components.
What is Polyetherketone (PEK)?
PEK (polyetherketone) is a high-performance, semicrystalline thermoplastic that has excellent thermal stability. PEK forms part of the PAEK (polyaryletherketones) family of materials, which also includes PEEK (polyetheretherketone). Semicrystalline plastics have ordered molecular structures and therefore have well-defined melting points.
The diphenylene ketone groups in PEK raise the stiffness of its polymer chains, leading to an increase in the glass transition temperature and melting point. Stronger molecular bonds produced by PEK's ether-to-ketone ratio of 1:1 underlie its superior thermal characteristics. The higher melting point increases PEK's service temperature, but it also means that processing temperatures must be correspondingly higher. This requirement makes it more technically challenging to process PEK with typical melt processing techniques. The properties of PEK can be further enhanced with the addition of fillers like glass and carbon fiber. These fillers can further improve temperature resistance, wear resistance, and impact strength.
What are the Properties of Polyetherketone (PEK)?
Polyetherketone is primarily used for its excellent mechanical properties at elevated temperatures. Below is a list of its key properties:
Property | Value |
---|---|
Property Density (g/cm^3) | Value 1 |
Property Hardness (Shore D) | Value 86 |
Property Yield Strength (MPa) | Value 115 |
Property Elongation @ Break (%) | Value 25 |
Property Flexural Yield Strength (MPa) | Value 180 |
Property Tensile Modulus (GPa) | Value 4.3 |
Property Melting Point (°C) | Value 373 |
Property Glass Transition Temperature (°C) | Value 152 |
Property Heat Deflection Temperature @ 1.8 MPa (°C) | Value 163 |
Polyetherketone Properties
Table Credit: https://www.matweb.com/search/DataSheet.aspx?MatGUID=a936ff7c9ef34598aed9bed3026cd3be
How is Polyetherketone (PEK) Made?
PAEKs such as PEK are manufactured using either a process called nucleophilic aromatic substitution (NAS) polymerization, or less commonly, electrophilic polymerization. The nucleophilic process uses a substitution reaction of aryl dihalides with aromatic diphenolates in a dipolar aprotic solvent. PEK can be processed using typical thermoplastic manufacturing methods such as injection molding, 3D printing, and extrusion. However, due to its high melting point, special processing conditions are required to produce good results. For example, molds need to be designed to extract higher than normal amounts of heat before the part can be ejected. Designing the mold means more cooling channels, thermal pins, and oil are used as the thermal transfer medium.
What Are the Characteristics of Polyetherketone (PEK)?
PEK is one of the more temperature-resistant grades of the PAEK group of materials. It remains dimensionally stable and resists both fatigue and creep damage at remarkably high temperatures. PEK performs well in continuous service up to 260 degrees C, which is extremely high compared to other engineering thermoplastics. For example, although PEEK has many other desirable characteristics, it is only rated for 230 degrees C in continuous use. PEK is the best choice for more severe thermal environments. In addition to its good mechanical performance at elevated operating temperatures, PEK also maintains excellent chemical resistance under heat stress. PEK is able to perform well under cyclic loading conditions that would typically result in fatigue failures, especially at elevated temperatures.
What are the Uses of Polyetherketone (PEK)?
PEK's resistance to elevated temperatures makes it useful in applications that require good mechanical performance under challenging thermal conditions.
PEK is especially useful in applications that experience cyclic loading, which can lead to fatigue failure in some materials. Some typical applications are listed below:
- Bearings
- Bushings
- Medical Implants
- Shafts
- Valve Seats
- Gears
- Electrical Connectors
- Impellers
What are the Advantages of Polyetherketone (PEK)?
Polyetherketone is an engineering plastic that has a long list of beneficial properties, some of which are listed below:
- Moisture Resistance: PEK is resistant to moisture ingress, which would typically cause swelling in a polymer. Materials made from PEK do not break down even when continuously submerged in boiling water.
- Biocompatible: PEK is a very non-reactive material, making it ideal for medical implants and other biologically sensitive applications. PEK can also be steam-sterilized due to its stability in high-temperature environments.
- High-Temperature Performance: PEK performs well at elevated temperatures, and has excellent fatigue and creep resistance. It has almost double the creep resistance of PEEK, another popular engineering plastic. PEK also has good compressive strength at elevated temperatures.
- Chemical Resistance: PEK is insoluble in acids and has good resistance to salts, solvents, and oils. This excellent chemical resistance is partly due to the strong chemical bonds present in the ketone and ether bonds in the PEK molecular chain.
What are the Disadvantages of Polyetherketone (PEK)?
PEK is an incredibly versatile material but it has poor UV (Ultraviolet) light resistance. Its high melting point makes it difficult to process. PEK’s disadvantages are described below:
- Low UV Resistance: PEK has poor resistance to UV radiation. It will weather when exposed to sunlight or other UV sources.
- High Cost: Synthesis and processing of PEK are both challenging, making PEK particularly expensive compared to other engineering thermoplastics.
- Difficult to Process: PEK has a very high melting temperature. Special processing to accommodate this otherwise beneficial characteristic of PEK adds complexity to the manufacturing process.
- Anisotropy: PEK's long, semicrystalline molecular chains display different (anisotropic) mechanical properties in a direction along these chains versus across the chains.
Common FAQs About Polyetherketone (PEK)
How Does Polyetherketone (PEK) Affect Human Health?
PEK has no known negative effects on human health. Skin exposure causes no reaction and accidental ingestion poses no significant risk. Inhalation of PEK does not have any negative effect on human health, either.
Is Polyetherketone (PEK) Toxic?
PEK is nontoxic due to its low reactivity and general chemical stability. Fumes released during melt processing present no risk if there is adequate ventilation in the processing facility.
What is the Difference Between Polyetherketone and Polyethylene?
Polyethylene (PE) is one of the most widely used thermoplastics and as such is much lower cost when compared to Polyetherketone. PE has a mostly crystalline structure with some amorphous regions. Polyethylene also has worse mechanical and thermal properties when compared to PEK. In general, PEK is a high-performance thermoplastic used for more challenging applications whereas Polyethylene is a commodity thermoplastic used for general purpose applications.
For more information on Polyethylene, see our full Polyethylene Guide.
Summary
This article provided a summary of the properties, uses, advantages, and toxicity of Polyetherketone (PEK). To learn more about how you could incorporate PEK into your high-temperature product applications to improve their performance, contact a Xometry representative or make use of Xometry's powerful instant quoting engine.
Disclaimer
The content appearing on this webpage is for informational purposes only. Xometry makes no representation or warranty of any kind, be it expressed or implied, as to the accuracy, completeness, or validity of the information. Any performance parameters, geometric tolerances, specific design features, quality and types of materials, or processes should not be inferred to represent what will be delivered by third-party suppliers or manufacturers through Xometry’s network. Buyers seeking quotes for parts are responsible for defining the specific requirements for those parts. Please refer to our terms and conditions for more information.
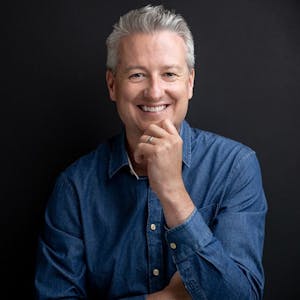