Polyethylene terephthalate, most commonly known as PET, is one of the most well-known thermoplastic polymer resins in the polyester family. Xometry customers often ask about this plastic, so this article will explain exactly what PET is, how it’s made, and take a look at its different grades, characteristics, and uses.
What is Polyethylene Terephthalate?
PET is a clear, strong, and stiff plastic often used for food and drink packaging, thanks to its high strength-to-weight ratio, and light weight, which keeps shipping costs low. If you turn most products at the supermarket around—from takeout food containers and water bottles to shampoo and liquid soap—you’ll likely see the PET logo at the bottom. It’s even used to make certain textiles and tennis balls. It was first made in the 1940s by chemists at DuPont, who were trying to make new synthetic fibers and later renamed the PET fiber "Dacron."
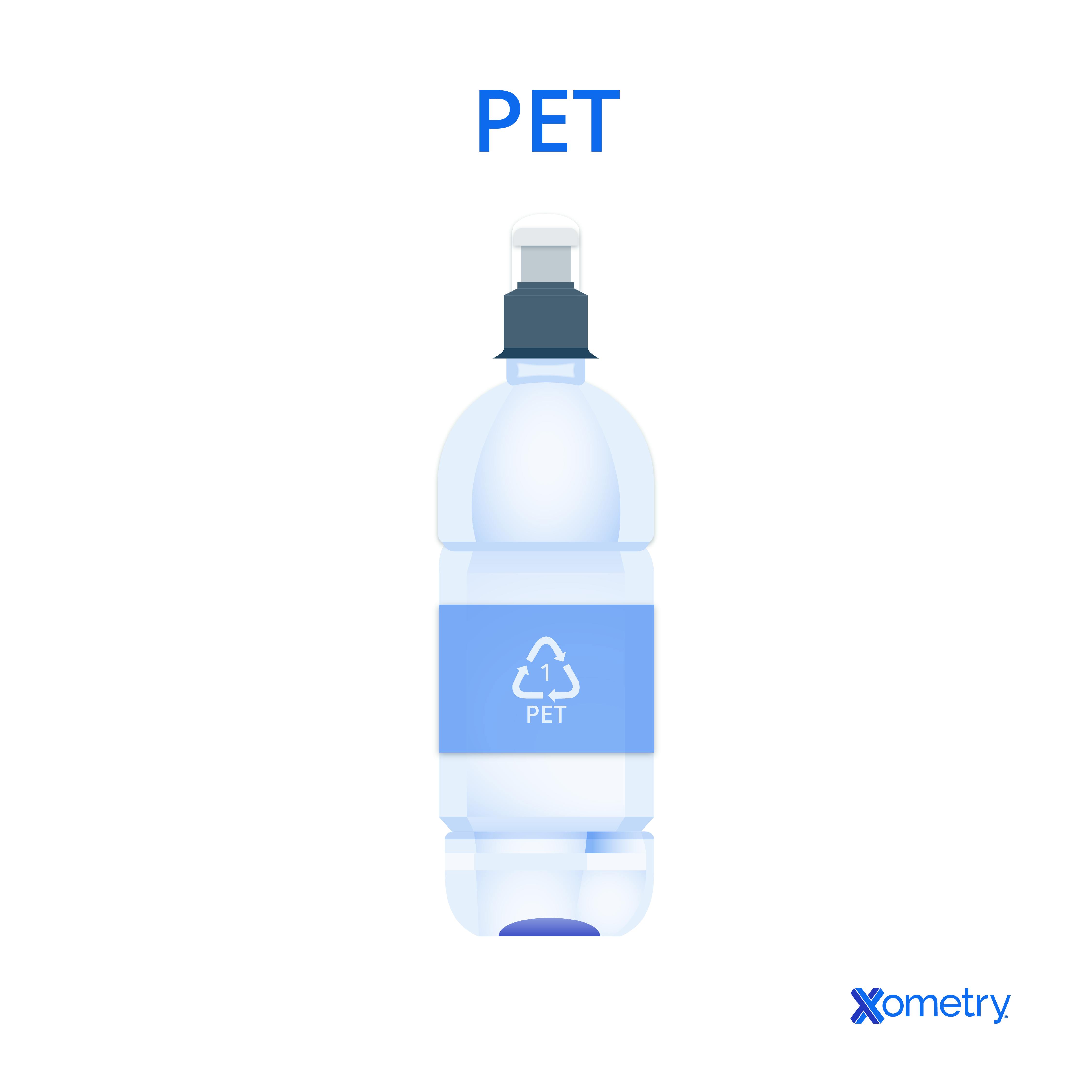
Over half of synthetic fibers found around the world are made from PET. When used as a fabric or a fiber, PET is generally called “polyester”, and when it is in more solid forms, like for packaging or containers, it’s referred to as “PET” or “PET resin.” PET is made with a mix of two elements that form a polymer chain: ethylene glycol (“MEG” from monoethylene glycol) and purified terephthalic acid (“PTA”). MEG usually comes from natural gas, and PTA from p-xylene that’s made from crude oil. It can also be made another way, by using MEG and dimethyl terephthalate (DMT) (C6H4(CO2CH3)2).
In the PET-making process, a catalyst (usually an antimony or titanium compound) and a stabilizer (phosphite) are added. To hide any yellow hues, a bluing agent, like cobalt salt, is also used. Once the chemical reaction happens, the strands—which will now look a little like spaghetti—will be extruded so that the material can be processed and made into whatever is necessary. Once the strands have cooled, they are cut into small resin pellets, which can then be melted to make extrusion or plastic injection molding easier. PET can be recycled (it’s also known as a “green” plastic) because it won’t burn in high temperatures; instead it will liquefy. It doesn’t absorb or interfere with microwave radiation (which is why many ready meals are PET packaged), and it won’t shatter, fracture, or break either.
Other perks of PET are its electrical insulating, gas (i.e., oxygen and carbon dioxide), and moisture barrier properties. Its gas permeability is very low (especially with carbon dioxide), and it’s not reactive with food or water. If quenches (cooled rapidly), it can be used for making see-through products. At high temperatures, PET absorbs moisture from the atmosphere at high temperatures, and if it’s reinforced with glass fiber, it can become even stronger. This might make it bend, or warp, though. PET temperatures to know about are listed below:
- Operating range: 60°C–130°C
- Processing range: 120~220°C
- Glass transition: 67–81°C
- Melting point: 260°C
- Glass conversion: ~165°C
PET’s heat resistance is lower than other polymers, and it can only really be injection molded with a screw-type machine. The material, although recyclable, isn’t biodegradable. In addition, PET resin can oxidize and change the taste of PET-packaged food or drinks when they’ve been on the shelf for a long time.
PET Grades
The following is a list of PET grades:
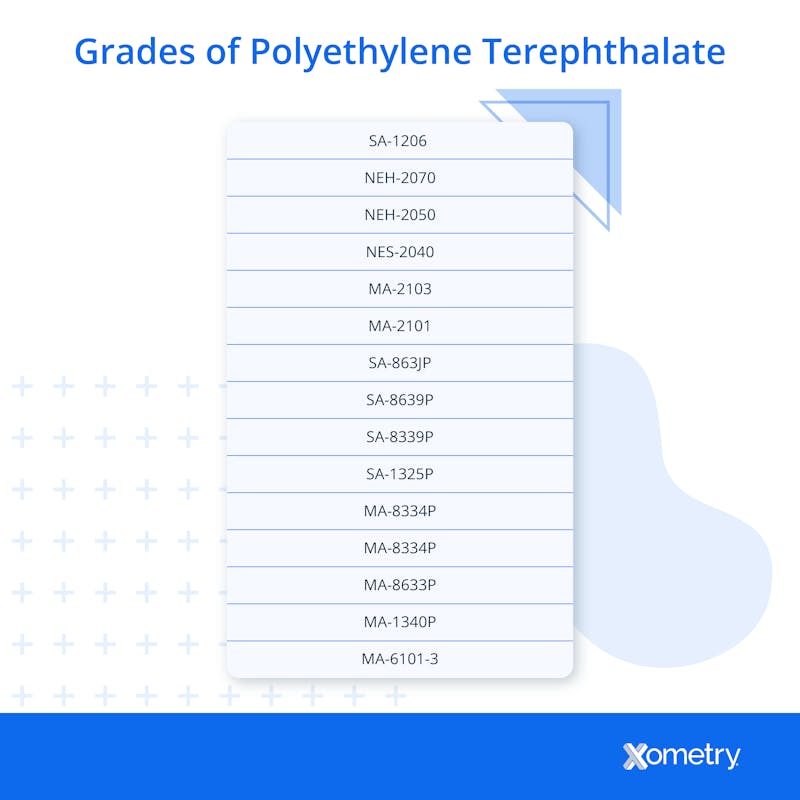
The commercial grades of PET are flame retardant, heat resistant, glass-reinforced, and various other engineering materials offering good strength. For a better surface finish and to reduce the likelihood of the material warping, other fillers can be added.
PET vs. HDPE
High-density polyethylene (HDPE) and PET are quite similar; they’re both used to make plastic bottles, and can both be made into any color of the spectrum. HDPE is a ubiquitous plastic used in manufacturing and can hold its own in temperatures in the range of -110° to 165°F (way more than PET). It’s not a clear plastic like PET, but it can be used for semi-opaque bottles. HDPE will start to degrade when in contact with alcohols, oils, and diluted acids whereas PET is unfazed by them.
To learn more, see our guide on PET vs. HDPE Polyethylene.
How Xometry Can Help
Xometry offers injection molding services and 3D printing using a variety of materials. Contact us for a quote today.
Disclaimer
The content appearing on this webpage is for informational purposes only. Xometry makes no representation or warranty of any kind, be it expressed or implied, as to the accuracy, completeness, or validity of the information. Any performance parameters, geometric tolerances, specific design features, quality and types of materials, or processes should not be inferred to represent what will be delivered by third-party suppliers or manufacturers through Xometry’s network. Buyers seeking quotes for parts are responsible for defining the specific requirements for those parts. Please refer to our terms and conditions for more information.
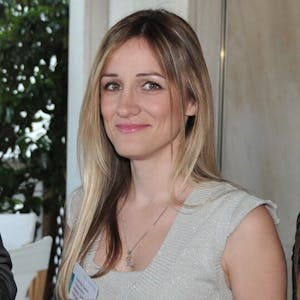