HDPE (high-density polyethylene) is a thermoplastic manufactured from petroleum byproducts, with polyethylene (PE) as its base product. HDPE stands apart from the rest of the PE forms by the relative sparseness of side-branched groups—fewer side branches resulting in higher density.
The range of densities of HDPE represents a spectrum of properties and suitability for wide and overlapping applications. It is widely employed in making packaging for household chemicals such as wet and dry detergents. It is also used for making caps/closures for low-density polyethylene (LDPE) bottles for similar applications and for PET bottles for water and carbonated drinks.
PET (polyethylene terephthalate) is among the most commonly utilized polyester polymers which are also generally derived from petrochemical sources. PET finds extensive application in various forms: as fibers for textiles; as injection-molded, blow-molded, clear, and colored containers for foods, liquids, and carbonated drinks; as extruded and calendered films for vacuum forming (or thermoforming) for product packages; as fine glass-fiber fillers; and as an injection-molded and extruded engineering polymer.
This article will compare HDPE vs. PET in terms of their application, properties, and costs.
What Is HDPE?
HDPE (high-density polyethylene) is the generic name for a spectrum of higher molecular weight polyethylene variants. All polyethylene forms are chemically similar. They have long chains of CH2 which have been created by high temperature and high pressure, catalyzing breakdown byproducts of diazomethane in a reaction chamber. For more information, see our guide on What is High Density Polyethylene.
Figure 1 are examples of products made with HDPE:
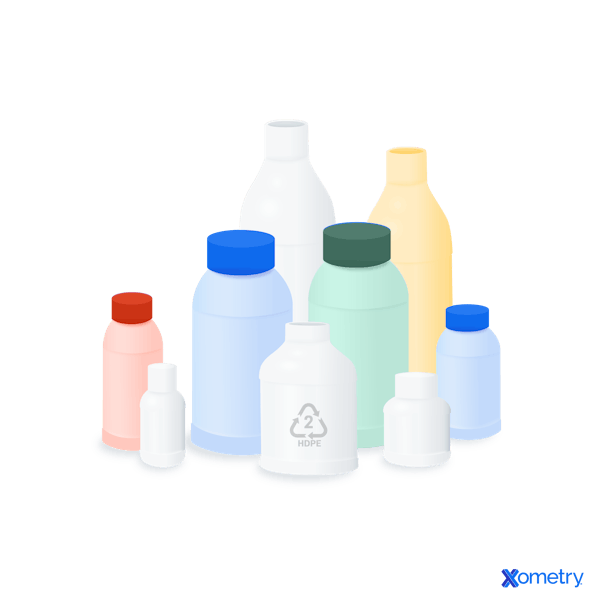
HDPE is characterized by particularly low levels of side-branching groups on the main polymer chains, and no long side branches at all. This allows the chains to lie close together in very orderly, pseudo-crystalline arrangements that allow higher-density materials. The degree of side branching is a result of variations in process conditions and catalysts. It is now a highly controllable property, so a range of (different) molecular weight end-result materials can be manufactured, with properties that are dependent on this variance. HDPE’s increased density and crystallinity make it stronger, less elastic, and more resistant to load distortion than many common polymers. Typical HDPE densities are between 0.933 and 1.27 g/cm3, with a resultant range in properties.
What Is PET?
PET or polyethylene terephthalate, belongs to the polyester family, which is a large and diverse group. PET is a strong and resilient material and relatively low cost, but its properties are greatly appreciated in various fields of manufacture. For more information, see our guide on What is Polyethylene Terephthalate.
Figure 2 is an example of a plastic bottle made with PET:
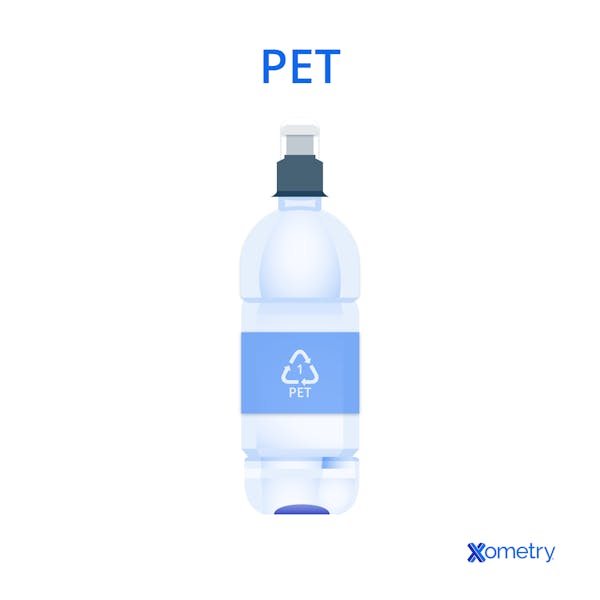
PET is a long-chain polymer, constructed from sequences of C10H8O4. Methods of manufacturing and handling result in partial crystallization of the generally amorphous, transparent material, negatively affecting various properties. Crystallization can result from maintained heat of 82°C as part of the drying process. Semi-crystalline results occur from biaxial orientation (stretching) in filmmaking or blow molding. In sheets, this material is sometimes known as Mylar®.
HDPE vs. PET: Applications and Uses
Some HDPE applications include:
- Fuel tanks, wiring & cables, cable ties and retainers, and body-mounted clips.
- Trash bins, garden equipment and furniture, storage bins, children's toys, and playground equipment.
- Crates, trays, milk bottles, caps for PET bottles, fuel cans, drums, and industrial-fluid containers.
- Ropes, fishing and sports nets, as well as industrial and decorative fabrics.
Some PET applications are:
- Packaging for water and carbonated soft drinks.
- Non-oriented film for thermoforming for packaging trays and blisters.
- Orientated PET films for tapes.
- Product jars, and heat-tolerant/microwave kitchen containers.
- PET monofil “felt” (non-woven fabrics for printing or oil and water filtering.
- Automotive wiper arms, gear housings, engine-bay covers, and connector housings (generally glass filled).
- Electronics manufacture, insulators.
Common applications for both HDPE and PET are:
- Liquid packaging, for which both display very high resistance to chemical attack and low tainting of contents.
- Electrical insulators, for which both materials have very high breakdown voltages.
HDPE vs. PET: Physical Properties
Table 1 below lists the physical properties comparison of HDPE vs. PET:
Property | PET value (metric) | Biaxially oriented PET value (metric) | HDPE value (metric) |
---|---|---|---|
Property Density | PET
value (metric) 0.7–1.45 g/cm3 (typical 1.3 g/cm3) | Biaxially oriented PET
value (metric) 1.39 g/cm3 | HDPE
value (metric) 0.933–1.27 g/cm3 |
Property Hardness, Shore D | PET
value (metric) 71–87 | Biaxially oriented PET
value (metric) Not relevant to films | HDPE
value (metric) 55–69 |
Property Tensile strength, ultimate | PET
value (metric) 22–95 MPa | Biaxially oriented PET
value (metric) 20 (MD)–24 (XMD) MPa | HDPE
value (metric) 15.2–45 MPa |
Property Tensile strength, yield | PET
value (metric) 55–260 MPa | Biaxially oriented PET
value (metric) 200 MPa | HDPE
value (metric) 2.69–200 MPa |
Property Elongation at break | PET
value (metric) 4–600% | Biaxially oriented PET
value (metric) 110% | HDPE
value (metric) 3–1900% |
Property Modulus of elasticity | PET
value (metric) 1.57–5.2 GPa | Biaxially oriented PET
value (metric) 5.2 (MD)–5.5 (XMD) GPa | HDPE
value (metric) 0.483–1.45 GPa |
Property Flexural yield strength | PET
value (metric) 55.1–135 MPa | Biaxially oriented PET
value (metric) — | HDPE
value (metric) 16.5–91 MPa |
Property Flexural modulus | PET
value (metric) 0.138–3.5 GPa | Biaxially oriented PET
value (metric) 4.1–4.3 GPa | HDPE
value (metric) 0.5–4.83 GPa |
Property Dielectric constant | PET
value (metric) 2.4–3.7 | Biaxially oriented PET
value (metric) — | HDPE
value (metric) 2.0–2.6 |
Property Melting point | PET
value (metric) 200–260 °C | Biaxially oriented PET
value (metric) 254 °C | HDPE
value (metric) 120–130 °C |
Property Max service temperature | PET
value (metric) 60–225 °C | Biaxially oriented PET
value (metric) 121 °C | HDPE
value (metric) 80–120 °C |
For various properties, MD refers to machine axis elongation, and XMD refers to cross axis.
HDPE vs. PET: Recyclability and Sustainability
Overall, HDPE (high-density polyethylene) materials are highly recyclable and can produce good resultant products for 10 or more cycles (potentially many more, if perfectly sorted and treated gently). However, actual recycling rates of the worldwide tonnage manufactured are minimal as a percentage of the total. Most HDPE is lost to the environment, put in landfills, or burned for disposal or power generation.
HDPE film materials are generally used for items requiring a degree of rigidity, and they are colored. They are relatively easy to sort for high purity. The process does not require the thorough separation of colors at the sorting stage unless a color-controlled recycled material is required. Most recycled applications accept a somewhat-variable brown color. Sorted plastic is washed, dried, and then shredded into fine shards for easier processing. This material is then heated to the melt/flow point and extruded as pellet feedstock. The end result is a high-quality but second-grade material that generally has a dark color and can be used for a range of otherwise normal applications. The pellets are used to substitute for virgin material, or more often as a second-grade minority component along with otherwise new material.
The mechanics of PET (polyethylene terephthalate) recycling are similar to that of HDPE—sorting, washing, shredding, and melting extrusion as chips. However, the manufacture of clear drink bottles consumes the largest amount of PET (after fabrics), so the sorting process is considerably easier as there is great homogeneity in the feedstock. This makes PET one of the only polymers that can sustain a truly circular supply chain. However, recycled material in its second incarnation is rarely used for high-quality bottles because of the potential for contamination during waste collection. Some use is made of twin films, where a thin, virgin material layer is used in the food contact surfaces. This is backed by a thicker, recycled layer. Most recycled PET is not made into bottles but goes to clothing/fiber production. Overall, although PET is highly recyclable, most markets make little use of recycling. Instead, the waste goes to incineration, landfill, or to the environment.
Both PE (polyethylene) and PET (polyethylene terephthalate) materials are commercially produced from hydrocarbon source materials and represent a significant environmental burden. Very little HDPE (high-density polyethylene) is recycled, though claims of 28% recycling of milk containers are made in some markets. Despite this, overall estimates of recycling volume are unreliable and very low. Higher proportions of PET are recycled because the production of textile fibers readily suits low-grade material. However, this usage is still extremely low in percentage terms of virgin production.
HDPE vs. PET: Cost
HDPE (high-density polyethylene) is a low-price commodity material manufactured in huge quantities. The price for virgin material is around $8.50 per kg, falling to $2.50 for recycled material. PET (polyethylene terephthalate) is also a low-price material manufactured in huge quantities. A spectrum of quality is available. Basic, unbranded granules sell for around $0.80–$2.00 per kg, DuPont®-branded material at $2.00–$3.00 per kg, and recycled material at $0.80–1.20 per kg.
Alternative Materials to HDPE and PET
HDPE (high-density polyethylene) have a wide range of applications, but they are narrow in scope, and alternatives are straightforward. For most applications, HDPE alternatives are: LDPE, PEX, ABS, PP, and rubber-modified PP.
PET (polyethylene terephthalate), on the other hand, is so widely used in single-use consumer packaging for drinks and food that it is the main focus for alternative materials that, in principle, will reduce the environmental burden. Alternatives are:
- In drinks-bottle manufacture, bio-sourced alternatives are: PEF (polyethylene furanoate), PET, PE, PA (polyamide, nylon), and PTT (polytrimethylene terephthalate).
- Hydrocarbon-based, biodegradable alternative materials are: PCL (polycaprolactone), and PBAT (polybutylene adipate terephthalate).
- Bio-source and biodegradable alternatives are: PBAF (poly(butylene adipate-co-butylene furandicarboxylate)), PLA (polylactic acid), PHA (polyhydroxyalkanoates), PBS (polybutylene succinate), and starch materials.
- In fiber production for textiles, filters, rope, etc, there are thousands of alternatives such as nylon, polyester, cotton, flax/linen, and hemp.
Summary
This article presented HDPE and PET, explained each of them, and discussed their various differences and applications. To learn more about HDPE and PET, contact a Xometry representative.
Xometry provides a wide range of manufacturing capabilities and other value-added services for all of your prototyping and production needs. Visit our website to learn more or to request a free, no-obligation quote.
Copyright and Trademark Notices
- Dupont® is a registered trademark of the E.I. DuPont de Nemours company.
- Mylar®, is a registered trademark of the DuPont - Teijin Corporation.
Disclaimer
The content appearing on this webpage is for informational purposes only. Xometry makes no representation or warranty of any kind, be it expressed or implied, as to the accuracy, completeness, or validity of the information. Any performance parameters, geometric tolerances, specific design features, quality and types of materials, or processes should not be inferred to represent what will be delivered by third-party suppliers or manufacturers through Xometry’s network. Buyers seeking quotes for parts are responsible for defining the specific requirements for those parts. Please refer to our terms and conditions for more information.
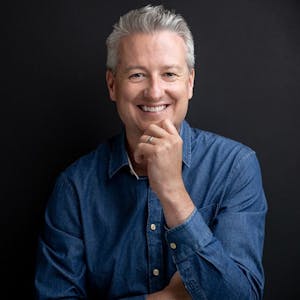