Custom Online Laser Cutting Service
High-quality laser cut Parts in days | Free standard shipping on U.S. and international orders | International prototype pricing includes tariffs
Cost-Effective Laser Cut Parts
Xometry offers an online custom laser cutting service in metal, plastic, rubber, foam, and wood. Xometry's laser cutting offers a cost-effective, on-demand solution for your manufacturing needs. Our laser cutting service supports a variety of materials, including many different types of metal, plastic (including acrylic), rubber, foam, and wood. We can meet your needs, whether it's prototype, low-volume, batch, or high-volume production runs.
You can get an instant quote from a 3D CAD file (file formats include: STEP, STP, SLDPRT, DXF, IPT, PRT, or SAT files) through our Instant Quoting Engine. What you see is what you pay. Your price for prototypes includes tariffs and shipping for standard parcels.
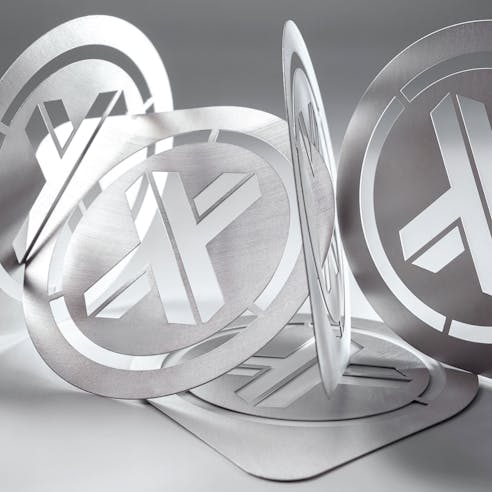
Metal Laser Cutting Service
Xometry offers a high quality metal laser cutting service. Our metal laser cutting services support a variety of metal materials, including: Steel, Stainless Steel, Tool Steel, Spring Steel, Aluminum, Brass, Bronze, Copper, and Titanium. Our laser cutting machines use both fiber lasers and CO2 lasers and can cut through up to 4 inches of metal material. Xometry offers instant quotes on metal laser cutting services, and free shipping on orders in the US.
For more information see our Metal Laser Cutting Service page, or simply Start a Quote Now.
Metal Laser Cutting Materials List
For a list of the metal materials supported by Xometry's metal laser cutting service, see below. Other materials may also be available for quote.
- 1075 Spring Steel, annealed
- 1075 Spring Steel, Blue Tempered
- 1095 Spring Steel, annealed
- 1095 Spring Steel, blue tempered
- 4130 chrome-moly steel, annealed
- Aluminum 2024-T3
- Aluminum 5052 H32
- Aluminum 6061 T6
- Aluminum 7075 T6
- Aluminum MIC6
- AR400 Steel, hardened
- AR500 Steel, hardened
- Bearing Bronze 932 M07
- Brass 260
- Brass 353 H02
- Brass 464 H01
- Bronze 220 H02
- Bronze 510 H08 (spring)
- Carbon Fiber
- Copper 101, H00 to H01
- Copper 110, Annealed
- Copper 110, H01
- Copper 110, H02
- Corten A588 (Weathered) Steel
- Hot Rolled Steel 1045
- Hot Rolled Steel A569/ASTM A1011
- Nickel 200, annealed
- Nickel 625, annealed
- Pre-Anodized 6061-T6, Black
- Silicon Bronze 655
- Stainless Steel 17-4 PH, annealed
- Stainless Steel 17-7 shim, hardened
- Stainless Steel 301, spring temper
- Stainless Steel 304
- Stainless Steel 304 shim, hardened
- Stainless Steel 304, #4 brushed
- Stainless Steel 316
- Stainless Steel 410, annealed
- Stainless Steel 430, #3 brushed
- Stainless Steel 440C
- Stainless Steel CPM 154
- Stainless Steel S30V, annealed
- Steel 1008, zinc-galvanized
- Steel 1018
- Steel 4140, hardened
- Steel 80CRV2
- Steel A36
- Steel A36, pickled and oiled
- Steel A366/1008
- Steel A572 Grade 50
- Steel G90, galvanized
- Titanium (Grade 2)
- Titanium 6Al-4V (Grade 5)
- Tool Steel D2, annealed
- Tool Steel O1, annealed
Plastic Laser Cutting Service
Our plastic laser cutting services support a variety of plastic materials, including: Acrylic, Foam, and Elastomer. Our laser cutting machines use both fiber lasers and CO2 lasers and can cut through up to 4 inches of plastic material.
For more information see our Plastic Laser Cutting Services page, or simply Start an Instant Quote Now.
Plastic Laser Cutting Material List
- ABS, Black
- ABS, White
- Acetal, Black
- Acetal, White
- Acrylic, Clear
- Acrylic, Colored
- Buna-N Rubber, Adhesive-Backed, Black
- Buna-N Rubber, Black
- EPDM
- EVA Foam, Black
- EVA Foam, Blue
- Extra Soft PU Foam, Adhesive Backed, Black
- Extra Soft PU Foam, Black
- Fiberglass
- Flame-Retardant PU Air Filter Pad, Gray
- Flame-Retardant Silicone Foam, Gray
- Garolite G-10 (FR4), Black
- Garolite G-11 (FR5), Green
- Garolite LE (Phenolic), Brown
- HDPE, White
- High Temp Silicone Foam, Adhesive Backed, Red
- High Temp Silicone Rubber, Adhesive-Backed, Red
- High Temp Silicone Rubber, Red
- Nylon 6/6, Black
- Paper Fiber and Buna-N Blend, Gray
- PETG Plastic, Clear
- Polycarbonate, Clear
- Polypropylene, White
- PTFE Gasket Material
- PTFE, White or Black
- PVC, Gray
- UHMW-PE, White
Acrylic Laser Cutting Service
Xometry offers a high quality Acrylic Laser Cutting service. We offer clear (transparent) acrylic materials, as well as a variety of colors. Advantages of laser cutting with acrylic include strength, easy of use, transparency, and waterproof/moisture resistance.
For more information see our Acrylic Laser Cutting Service page, or simply Start an Instant Quote Now.
Wood Laser Cutting Service
Xometry offers a high quality Wood Laser Cutting service. We offer a variety of wood materials including Cherry Hardwood, Hardboard, MDF, Poplar Hardwood, Red Oak Hardwood, Uncoated Wood Laminate (Plywood), Chipboard, and Birch.
For more information see our Wood Laser Cutting Service page, or simply Start an Instant Quote Now.
Alternatives to Laser Cutting
Alternatives to Laser Cutting for sheet cutting projections include waterjet cutting services and plasma cutting services. Laser Cutting has limitations on the thickness of the material being cut. Laser cutting can cut up to 4 inches of material. For materials thicker than 4 inches, use waterjet cutting or plasma cutting services.
Types Of Laser Cutters Available From Xometry
C02 Laser Cutting Machines
The most common laser cutter type because of their relatively high energy efficiency and high power output ratio. Best suited for cutting, boring, and engraving services.
Nd Laser Cutting Machines
Nd lasers have a high energy, and are used for boring and welding.
A disadvantage of Nd lasers are their low repetition efficiency.
Nd:Yag Laser Cutting Machines
Nd:Yag Lasers are high powered lasers and suitable for cutting thick materials. Nd:Yag lasers can be used for boring, welding, and engraving.
A disadvantage of Nd:Yag lasers is that they are more expensive to operate.
Ready to get started on your laser cutting quote?
Free shipping available for domestic laser cutting orders ; learn more!
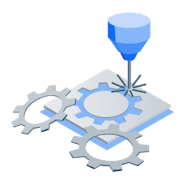
Blank Preparation
Laser cutters can cut many materials with high precision, making it perfect for preparing flat patterns or material blanks.
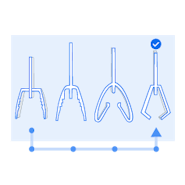
Rapid Prototyping
The range of materials available, low cost per unit, and speed of production makes laser cutting a great option for prototyping.
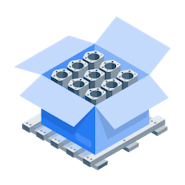
End-Use Production
Large format cutting, vast material options, and high throughput have made laser cutting a favorable technology for end-use parts.
Advantages of Laser Cutting
Durability
Laser Cutting produces highly durable parts well-suited for both functional laser-cut prototypes and end-use production.
Scalability
All sheet metal parts are built on-demand and with lower setup costs compared to other manufacturing processes. Depending on your needs, order as little as a single prototype up to 10,000 production parts.
Material Selection
Choose from a variety of materials across a wide range of strength, conductivity, weight, and corrosion resistance.
Rapid Turnaround
Combining the latest cutting, bending, and punching with automated technologies, Xometry provides instant sheet quotes that can often ship the same week.
Laser Cut Metal General Tolerances
Description | General Tolerance |
---|---|
Description General Tolerances | General Tolerance For full details on tolerances offered by Xometry's sheet cutting service, including edge to edge tolerance and taper, please consult our manufacturing standards. |
Description Thickness Dimension | General Tolerance Thickness tolerances are determined by the material blank. |
Description Minimum Recommend Part Size | General Tolerance 1.000" |
Description Minimum Feature Size | General Tolerance 2X material thickness with a minimum of 0.062" |
Description Kerf (slit size) | General Tolerance Approximately 0.020" |
Description Edge Condition | General Tolerance Laser cut parts will have a vertical striation on the cut face. |
This table contains general information concerning Xometry’s laser cutting services. Learn more about our official sheet cutting manufacturing standards.
Design Guide: Laser and Sheet Cutting
An Overview of Laser Cutting
The Basics Of Laser Cutting
Laser cutting directs a high-powered laser through optics to cut materials for industrial applications. Laser cutting is both more precise and less energy-consuming than plasma cutting but has an upper threshold on the thickness of the material being cut.
A laser cutting machine is a type of CNC machine that uses a thin, high-powered focused laser beam to cut materials. Laser cutters are commonly used for quality welding and to cut industrial sheet metal, but laser cutters can also be used for other materials such as plastic, rubber, glass, wood, and aluminum.
The Laser Cutting Process
Laser cutters focusing optics are used to direct electrical energy into a high-density light beam, and CNC is used to manage either the workpiece or the laser beam. The material processed by the laser cutter is then melted, burned, vaporized, or blown away by a jet of oxygen or nitrogen.
Advantages of Laser Cutting Services
The laser cutting process offers several advantages over traditional mechanical cutting or CNC machining processes, including quicker production, decreased contamination of the workpiece, and reduced chance of warping. A laser cutter produces clean laser cut parts and has a small chance of operator error making them great for fast prototyping.
Xometry's custom laser cutting services offer a cost-effective on-demand solution for your sheet metal fabrication needs, including the material, details, and size of the project. From fast, low-volume prototypes to high-quality, high-volume production runs, Xometry’s massive partner network has the ideal shop and the ideal machines for the job.
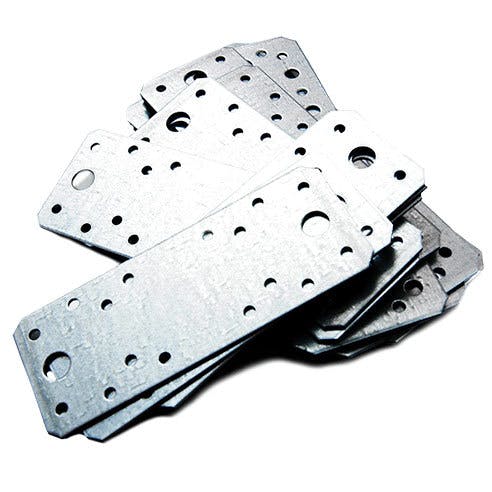
Why Xometry?
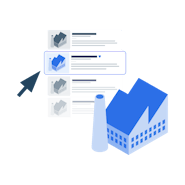
Endless Options
Choose from millions of possible combinations of materials, finishes, tolerances, markings, and certifications for your order.
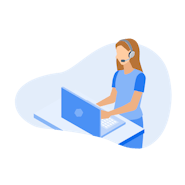
Easy to Use
Get your laser cut parts delivered right to your door without the hassle of sourcing, project management, logistics, or shipping.
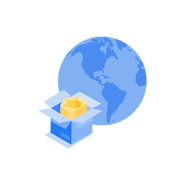
Vetted Network
We are ISO 9001:2015, ISO 13485, IATF 16949:2016, and AS9100D certified. Only the top shops that apply to become Suppliers make it through our qualification process.