Case Study: Entrepreneur Levels the Field in the Aerospace Industry With Miniature Propulsion System.
Applied Ion Systems is leveling the playing field in the aerospace industry by using CNC machined and 3D printed parts from Xometry to build cost-efficient, electric propulsion systems for nano and pico satellites.
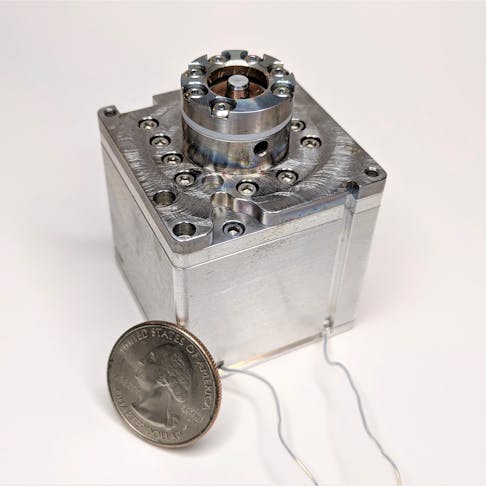
At a Glance
Industries | Manufacturing Services Utilized | Project Brief | Solution |
---|---|---|---|
Industries | Manufacturing Services Utilized | Project Brief Applied Ion Systems (AIS) is making tiny electric propulsion systems to lower the barrier of entry for small teams in the aerospace industry. AIS needed a way to source increasingly complex parts while saving time and money. | Solution By ordering CNC machined and 3D printed parts through Xometry, AIS dramatically reduced their costs and lead times. Xometry’s network capabilities empower AIS’s rapid prototyping projects and help them develop revolutionary propulsion systems faster. |
The Final Frontier
At 10:29 PM Moscow time on October 4th, 1957, the Soviet Union launched the world’s first satellite into low orbit. It was named Sputnik 1. Humanity’s first foray into Earth’s orbit also kicked off the space race between the United States and the Soviet Union. When the space race began, competing nation-states were the only entities that could pool the necessary financial and technological resources to create satellites like Sputnik. But times change, and the barrier to participate in satellite launches wouldn’t remain high forever.
More than half a century later, at 5:30 pm EST on March 22 of 2021, Michael Bretti was sitting in his living room. He was eagerly watching a live stream of a satellite launch. The satellite, christened “Care Weather Hatchling Veery 1U Cubesat”, was equipped with an AIS-gPPT3-1C Micro Pulsed Plasma Thruster. This plasma thruster would help the satellite make very small maneuvers in orbit. Michael built that thruster through months of trial and error. And he did it in the basement of his New York home.
Michael is the founder of Applied Ion Systems (AIS), a research startup specializing in open-source R&D, engineering, and testing of plasma and ion thruster systems. Michael is constantly developing and testing new iterations of these thruster systems. Xometry’s network capacity makes it ideal for engineers like Michael who need a service that can meet their rapid prototyping needs. When asked why he exclusively uses Xometry’s services for his current projects, Michael cited many reasons, including
- Xometry provides access to every service Michael needs all in one place.
- Xometry offers a high level of precision required for all of his projects.
- Xometry is significantly quicker and cheaper than local options.
- Xometry’s Instant Quoting Engine℠ helps Michael quickly set his budget.
- Last but certainly not least, Xometry offers a wide variety of high-performance engineering materials that are essential for each prototype.
Applied Ion Systems services are especially valuable to teams that need cost-efficient propulsions for their nano and picosatellites. To understand the impact of Applied Ion Systems, you first must understand why nanosatellites are so helpful. Typical satellites can range in size from a refrigerator to a bus. By comparison, nano and pico satellites are much smaller. They are measured by Units or U’s for short. A unit consists of a space of 10cm x 10cm x 10cm. The size of a typical nanosatellite is commonly in the range of 1U - 12U’s, with picosatellites such as PocketQubes ranging even smaller, with units measured in P’s, or 5x5x5cm in size, and in the range of 1-3P. Not exactly bus-sized. These tiny satellites can perform many of the same functions as their larger cousins and their smaller size makes them significantly more cost-effective.
That may sound ideal for smaller teams who can’t afford to send a refrigerator-sized piece of tech into orbit, but there is a problem. While these smaller satellites are more cost-effective, they need propulsion systems. Unfortunately, the electric propulsion systems on the market are still not cost-effective for most smaller organizations and individuals. These propulsion systems can add $50,000 or more to the cost of the project. They can even be more expensive than the nanosatellites they are attached to and launch to get the nanosatellite in orbit! Space may be the final frontier, but only for those who can afford to go there. This high bar to entry hasn’t stopped many aspiring researchers and hobbyist engineers from coming together and sharing their insights to learn more about the subject and find solutions to this issue.
The Hobbyist Becomes an Entrepreneur
When Michael first started working on high vacuum physics projects and sharing these projects with his maker community, nobody specifically focused on electric propulsion systems. Although electric propulsion may still sound intimidating to a lay audience, it is quite commonly used by those sending satellites into space. Sputnik may not have had one, but electric propulsion systems have still been around for decades. In Michael’s mind, these decades-old systems shouldn’t be nearly as ethereal or expensive as they currently are. These factors keep people from learning about the underlying science and engaging with the hobby that has given so much to him. So Michael set about designing a propulsion system that would be significantly more cost-effective than others on the market. In addition, he decided to share his progress and insights with the world to help others learn more about this technology and the science surrounding it. Through years of research, hard work, trial, and error, he finally designed an electric propulsion system that made it inside Earth’s orbit.
Don’t be fooled by this triumphant telling of Michael’s story; it wasn’t always easy. Today, Applied Ion Systems exclusively use Xometry’s services for machining and 3D printing, but this wasn’t always true. Michael drilled his first designs by hand on his kitchen table. He eventually began reaching out to local machine shops when that process became too impractical. And while there were plenty of available suppliers, their services were very costly. This process worked well enough to get his first thruster design into orbit, but he knew it wasn’t sustainable. His thruster designs kept growing in complexity, iteration by interaction, and he needed a service that could keep up. And the assistance would need to be faster and more cost-effective than what his local machine shops provided.
Xometry Fast Tracks AIS’s Rapid Prototyping
When asked about how he found out about Xometry, Michael replied, “I found out about Xometry actually purely by chance. I was researching online 3D printing services and immediately saw Xometry had a fantastic range of materials available. I signed up and was really drawn to the real-time pricing and quoting on the Xometry site, which helped immensely with planning and budgeting. After, I began exploring CNC services and have been using it for both professional and personal projects ever since!”
We are glad he found us. Xometry’s vision is to accelerate innovation by providing real-time, equitable access to global manufacturing capacity and demand. The world is full of intelligent, inspiring engineers like Michael, and the manufacturing capabilities of Xometry help them to get the high-quality parts they need in time without breaking the bank. Our CNC machining and 3D Printing capabilities allow customers like Michael to prototype with ease. The strength of our network gives customers a diverse suite of options to address the complex challenges in their work.
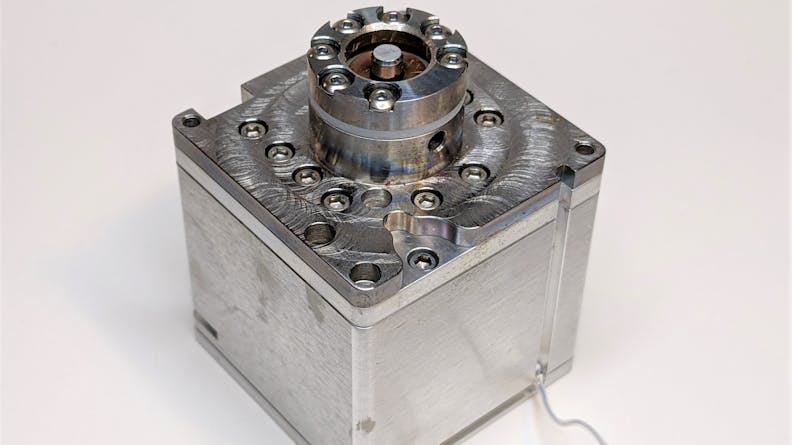
Introducing the AIS-AHT1-PQ Pico Anode Layer Hall Thruster
The AIS-AHT1-PQ Pico Anode Layer Hall Thruster is the latest project out of Applied Ion Systems. “With the AHT1-PQ, Applied Ion Systems aims to defy convention and redefine scaling and accessibility of Hall thrusters to a level never before realized or seen in the EP field prior, providing the lowest cost, most compact, and most accessible Hall thruster to hit the nanosatellite market.” (Source). From the CNC machined steel Hall thruster head to the 3D printed insulator inside the thruster, every single custom machined part is sourced from Xometry.
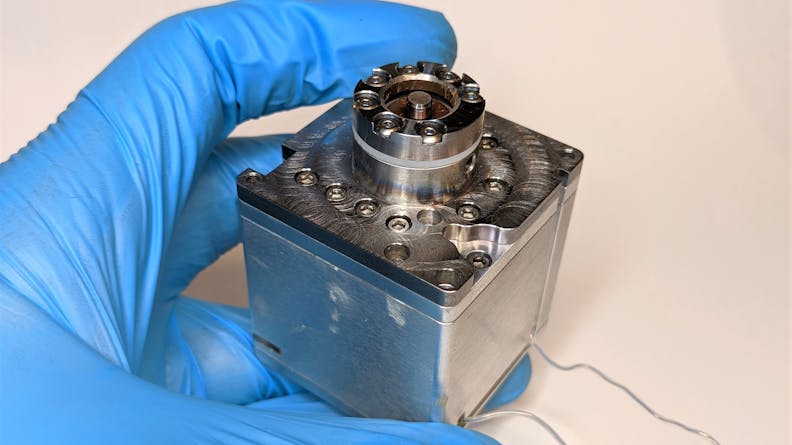
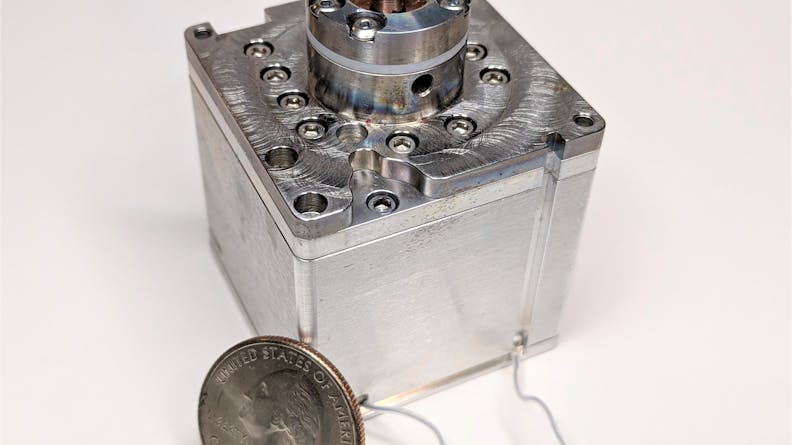
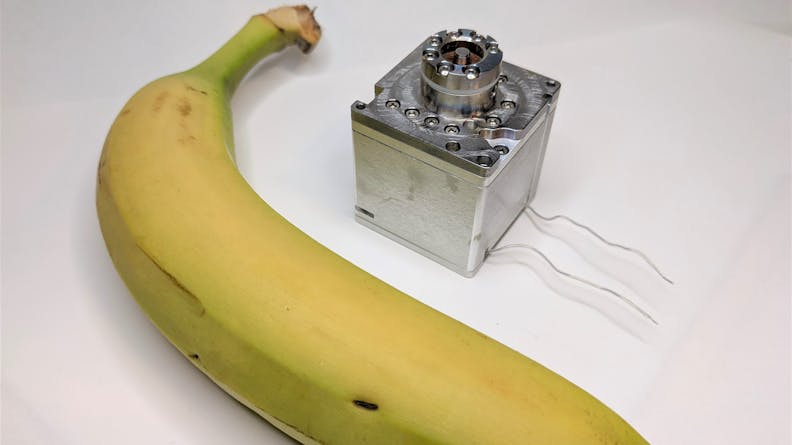
The thruster itself is incredibly light, weighing in at less than 300 grams and measuring only 42x42x56mm in volume, making it especially useful for pocket cube satellites. It is also small enough to fit in the palm of your hand! Through the use of Adamantane fuel, Michael was able to reduce the size of the thruster dramatically. Adamantane is a diamondoid hydrocarbon that exhibits similar properties to the more classically studied and popularly used molecular fuel alternative Iodine. Both fuels have solid storage, low-temperature sublimation in vacuum, and a large ionization cross-section. However, unlike Iodine, Adamantane is relatively safe to handle, non-toxic, and non-corrosive. The reduced power consumption and overall size makes it much more accessible for smaller teams and much more cost-effective. Coming in at about 1/8U in volume for the complete system (1P for PocketQube standards), Michael believes the AIS-AHT1-PQ Pico Anode Layer Hall Thruster is the smallest fully integrated Hall thruster system being developed on the market based on publicly available knowledge.
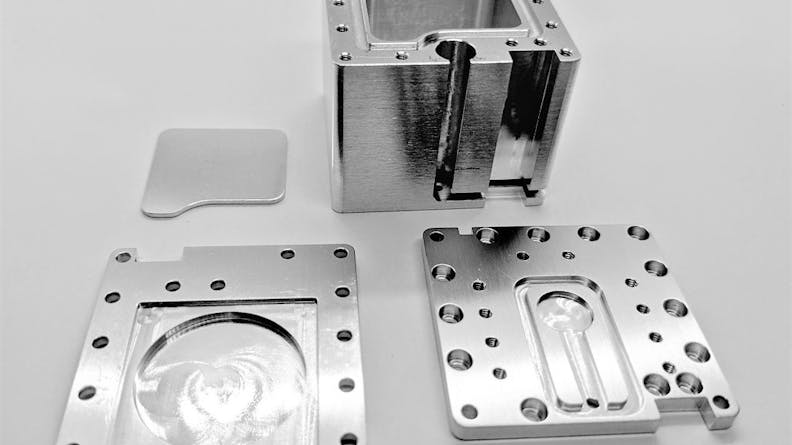
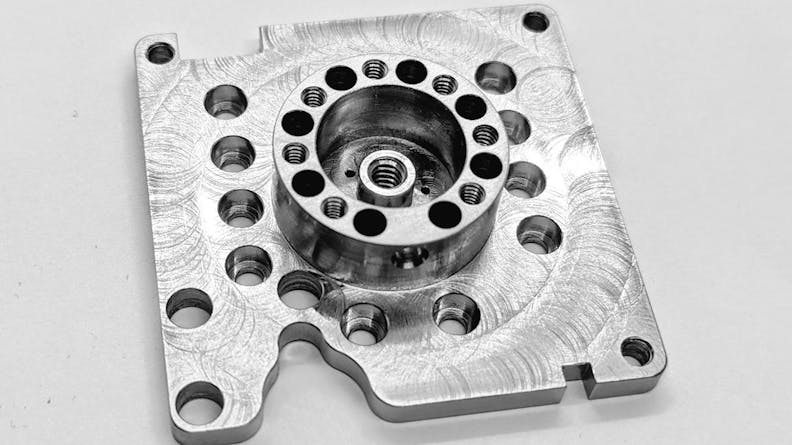
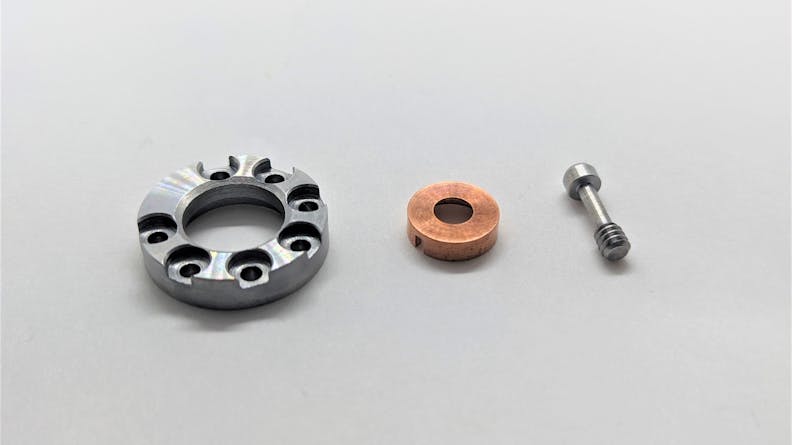
Tech Dissection: Examining the CNC Machined fuel Tank and 3D Printed Insulator
The full thruster system combines several tightly integrated subsystems, which are directly assembled to keep the assembly as compact as possible. There are two main subsystems: the fuel tank and the Hall thruster head. Each subsystem is made from several complex custom components, all made through Xometry’s CNC machining service.
The fuel tank consists of a solid Adamantane fuel storage, a fuel compression mechanism, a sublimation heater, an integrated microvalve, and an adapter plate to direct fuel to the thruster head. The main fuel tank and tank cover were manufactured from 7075-T6 aluminum. 7075-T6 has a lower weight and higher strength than other aluminum alloys like 6061, which is advantageous given the dozens of small threaded holes that keep the parts sealed and assembled. By contrast, The tank baseplate was made from 6061 because it costs less than 7075, and its extra strength was unnecessary.
The thruster head assembly revolves around the main thruster head plate, which consists of a complex single machined multipurpose part. The thruster head is machined directly into the adapter plate, which bolts directly on top of the fuel tank cover, providing a direct fuel flow path from the valve to the thruster head without the need for external lines. This design is what keeps the system highly compact. The head was machined from 1018 steel. Its low cost and high iron content made it the ideal material to complete the magnetic circuit used for the Hall thruster. The head includes fuel feed channels, mounting points for the tank, electronics, pole pieces, and features for embedding permanent magnets for the magnetic circuit. The inner pole piece and upper pole cap were also made from 1018 steel for the same reasons. The anode is machined from copper, selected for its non-magnetic properties and ease of connection to the anode wire feed.
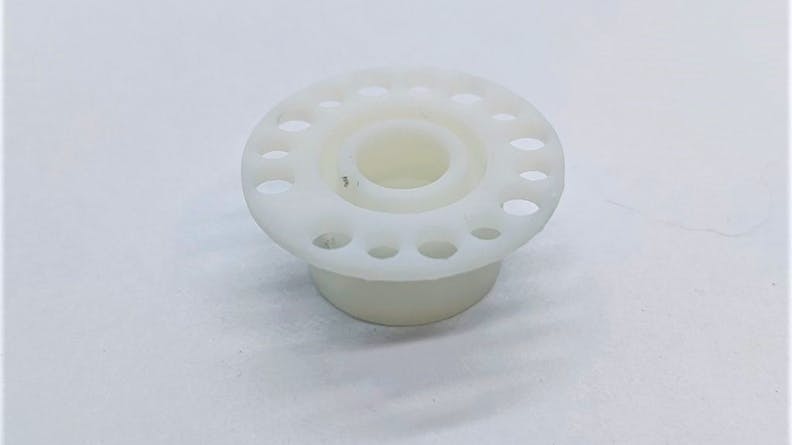
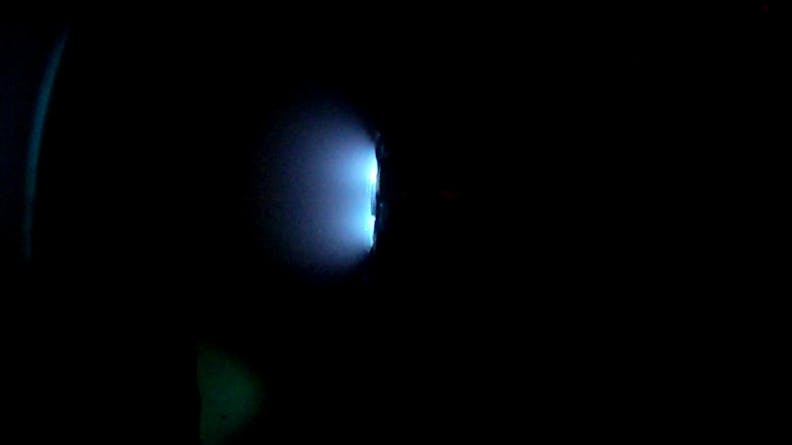
This is the 3D printed Somos PerFORM insulator.
Michael’s design didn’t just benefit from Xometry’s CNC machining service; our broad range of 3D printing capabilities were instrumental for each iteration. One of Micheal’s favorite 3D printing materials that Xometry offers is SLA resin Somos PerFORM. Its ability to hold up as it undergoes plasma bombardment, as well as its high dielectric strength, high-temperature resistance, high printing precision, and resolution, make it ideal for rapid prototyping new iterations of the 3D insulator, seen above. This multifunction piece serves as the anode holder, insulator, power feed, and fuel flow channel, helping direct the fuel between the anode and the central pull piece. And Somos Perform’s ceramic particles embedded in the resin and overall heat-resistant qualities make it ideal for withstanding the plasma bombardment and thermal gradients seen during operation. This quality comes in handy every time Michael tests new iterations of the Hall thruster.
The Future of Applied Ion Systems
In addition to his work on AHT1-PQ, Applied Ion System’s is developing many new projects, including:
- a micro vacuum arc thruster called (AIS-VAT1),
- a new experimental carbon nanotube neutralizer cathode for the next iteration of the AHT1-PQ (both of which will utilize Xometry’s Somos PerFORM for the housing),
- And the beginnings of a liquid metal field emission electric propulsion thruster.
With our easy-to-use platform, Xometry is ideal for companies of any size for their rapid prototyping needs. We provide custom parts made from various materials and processes while remaining cost-effective and providing fast lead times. We are excited to work with entrepreneurs like Michael, who revolutionize industries and change the world. If you want to learn more about how we can serve others in aerospace, check out this NASA case study, our aerospace industry page, or check out our guide to quoting flight parts. As for Michael, We want him to have the last word.
Thank you, Michael! We look forward to working with you on your future endeavors.