Creep is a form of time-dependent plastic deformation that occurs in a material subjected to constantly applied stress. If enough creep damage accumulates, the material can fail due to excessive deformation or fracture. Creep is caused by the localized movement of atoms within the grain structure or along grain boundaries over a period of time. Creep failure can occur in all types of materials including metals, polymers, and ceramics. It typically occurs at elevated temperatures, but can also occur at ambient temperatures. From the deformation of gas turbine blades in aircraft to the deformation of concrete slab sidewalks, creep is common in many applications. Understanding creep and creep failure, and their effects on different materials, is essential to the successful and safe implementation of parts and structures. This article will focus on the definition of creep failure, how it works, and examples in different materials.
What Is Creep Failure?
Creep is the time-dependent plastic deformation that occurs when a material is subjected to a continuously applied stress, typically in the presence of elevated temperatures. Creep failure is the failure of a material due to excessive accumulation of creep, or when the material no longer satisfies its intended function due to deformation or fracture. As stresses are applied at increased temperatures (typically about 30-40% of a metal’s melting point or 40-50% of a ceramic’s melting point) the dislocation of atoms, either by diffusion or atomic glide and climb, occurs within grains or along grain boundaries. With time, the rate of plastic creep deformation is initially rapid, then slows to a stable rate, and then finally speeds up again in what is called "tertiary creep." This last stage is when internal voids in the material, micro-cracks, and the separation of grain boundaries lead to final failure.
Creep deformation can begin at elevated temperatures, between 30 and 50% of a material’s melting point depending on the type of material, and is hastened as temperatures or stresses increase further. Creep failure can occur at stresses lower than yield stress, and thus creep tests cannot always accurately predict when creep failure will occur.
Is Creep Failure the Same as Creep Fatigue?
No, creep failure is not the same as creep fatigue although creep damage can be a component of creep fatigue. Creep failure is characterized by the permanent deformation of a material due to constantly applied stress at elevated temperatures. Whereas, creep fatigue is characterized by the permanent deformation of a material due to cyclically applied stresses at low or moderate temperatures. The indications of creep failure and creep-fatigue are different. In creep failure, materials will slowly deform over time and often occur without notice due to changes occurring in the material’s microstructure. Regardless of whether creep damage or fatigue damage conditions predominate, the combination of accumulating creep damage and fatigue crack propagation can eventually lead to material failure.
How Does the Creep Failure Process Work?
The creep failure process works by the gradual deformation of a material’s microstructure. The atoms within a material’s crystal lattice cause the material’s lattice structure to deform either by diffusion or dislocation. Different types of creep deformation, including Nabarro-Herring creep, dislocation creep, Coble creep, and Harper-Dorn creep, characterize different atomic movements. For instance, Nabrro-Herring creep and Coble creep are two types of creep that are characterized by the diffusion of atoms. When a material is at a high temperature and is subjected to constantly applied stress, atoms diffuse into vacancies within the crystal lattice. For dislocation creep and Harper-Dorn creep, atoms move due to the movement of dislocations within the crystal lattice either by glide or slip mechanisms.
As force is constantly applied at an elevated temperature, atoms continuously move and the material’s microstructure continuously deforms. Eventually, excessive deformation will lead to the formation of micro-cracks, voids, and grain boundary separation which inevitably leads to material failure. Methods to mitigate the effects of creep include selecting materials for parts to perform under the critical temperature at which creep starts or repairing and replacing creep-affected parts before the damage becomes too much.
How Does Creep (Deformation) Cause Creep Failure?
Creep deformation is time-dependent, occurs at heightened temperatures, and can eventually cause failure due to the accumulated creep damage. Creep deformation occurs in three stages which are listed and described below:
- Primary Creep: Primary creep is the first stage of creep. It is characterized by the instantaneous or continuous application of a force, followed by elastic deformation, and eventually plastic deformation at temperatures that are at least 35 to 45% of the material’s melting point. Increased temperatures increase the internal energy of atoms in a material’s microstructure and make it easier for atoms to overcome barriers to their movement within the crystal lattice structure. Deformation in the primary creep stage occurs rapidly and then slows as time goes on due to the work hardening of the material as it deforms.
- Secondary Creep: During secondary creep, the material’s strain rate stabilizes as strain increases nearly linearly with time. Deformation at this stage is much slower compared to deformation in the primary creep and tertiary creep stages. As plastic deformation occurs during this stage, damage to the microstructure accumulates as atoms and vacancies dislocate.
- Tertiary Creep: Tertiary creep is the last stage of creep deformation and concludes with the material’s failure. During this stage, grain boundary separation, internal void form, and microcracks initiate and grow as a result of the constant movement of dislocations and diffusion of atoms occurring in the part. These three things result in an eventual reduction in the cross-sectional area of the part which consequently leads to the development of stress concentrations and acceleration of the strain rate in the material as it responds to the continuing application of a constant stress. Eventually, the material fails to satisfy its intended function and may even catastrophically rupture or fracture.
To learn more, see our guide on Creep (Deformation).
How Is Creep Life Determined?
The onset of creep failure can be determined by conducting a creep test. A creep test enables engineers to understand the relationship between stress, temperature, and strain rate and how these phenomena affect part behavior. A creep test entails applying a constant tensile stress to a test specimen held at a particular temperature. The accumulating strain in the material is graphed as a function of time until the material ruptures or until some other predetermined test-end criterion is met, such as a certain percent strain, or completion of a specified number of hours with total material strain less than a given value.
Creep tests provide valuable insight into materials since they characterize creep rates and the time to rupture. Data from a creep test can help engineers to successfully design parts and structures with the required durability for high-stress, high-temperature service environments.
How Important Is It to Predict Creep Life?
It is very important to try to predict creep life and to analyze any failures to determine what role creep may have played in them. Failure to use all available tools to predict creep life and to monitor in-service equipment for creep damage can lead to creep failures. These failures can be catastrophic and can lead to property damage, injury, and even death. For this reason, the design of parts and structures that operate under stress at high temperatures, such as steam turbine blades and boilers, must be based on rigorous materials testing under conditions similar to service conditions. They must also be inspected regularly for evidence of accumulating creep damage during their in-service lives.
Can Parts Which Fail Due to Creep Be Repaired?
No, parts that fail due to creep damage cannot be repaired. Once creep failure has occurred, the part has permanently deformed and cannot be restored to its original dimensions. While failures due to creep cannot be repaired, creep deformation can be slowed by selecting materials with higher melting temperatures or larger grains. Once a selected material is operating in its planned service environment, the creep rate can be slowed, if necessary, by lowering stresses (reducing pressure in a boiler, for example) or lowering operating temperatures. Mitigation strategies may or may not be possible for a given application. Therefore, proper design and careful material selection are the two biggest defenses against creep failure.
What Materials Are Prone to Creep Failure?
Some materials are more prone to creep failure than others. At a given service temperature, materials with lower melting temperatures will be more susceptible to the effects of creep than materials with higher melting temperatures. Three materials prone to creep failure are listed and described below:
1. Zinc
Zinc has a melting temperature of 419.5 °C. Since creep can begin at temperatures that are approximately 35-45% of the material’s melting temperature, creep in zinc can begin at temperatures as low as 147 °C. Because of its low melting temperature and consequent susceptibility to creep, zinc is undesirable for use in load-bearing applications at operating temperatures higher than 35% or 146.8 °C of its melting temperature.
2. Lead
Lead has a relatively low melting temperature (327 °C). Therefore, lead is susceptible to creep at temperatures as low as 114.5 °C. This is much lower than steel, for which creep does not begin until temperatures in the range of 480 °C.
3. Tin
Tin has a melting temperature of 232 °C. Tin has an even lower melting temperature than zinc or lead. That being the case, the creep of tin can begin at temperatures as low as 81 °C — lower than the boiling point of water! This limits the use of tin for load-bearing applications at temperatures above 80 °C.
How Do Plastics Fail by Creep?
Creep failure in plastics occurs when polymer parts are subjected to continuing stress and elevated temperatures. The primary creep mechanism for plastics is the movement of atoms by either dislocation slide or glide. Creep is more likely in plastics with amorphous structures since their molecular chains slide past each other more easily than the molecules in plastics' crystalline structures.
How Does Concrete Fail by Creep?
Creep failure can occur in concrete at both ambient and elevated temperatures. Concrete creep failure can occur in concrete columns, beams, and large structures like dams. Excessive creep in concrete can lead to buckling columns, deformed beams, or cracks in the concrete structure. Higher aggregate percentages can reduce the creep strain rate while higher concentrations of water in the mix can lead to higher creep strain rates.
What Is an Example of Creep Failure?
Creep failure occurs in many different industries and applications. An example of creep failure in the aerospace industry is the slow deformation of jet turbine blades. Jet turbine blades are subjected to high temperatures — up to 600 °C — and heavy loads when in use. Over time, the constant application of a load at high temperatures causes the turbine blades to warp, necessitating replacement.
Another example of creep failure is the rupture of pipes that transport oil in the oil and gas industry. These pipes carry oil under pressure at elevated temperatures. The increased temperature and pressure gradually cause pipes to bulge and eventually rupture.
Common FAQs About Creep Failure
How Can Creep Failure Be Prevented?
The two main strategies for preventing creep failure are careful material selection and continuous monitoring of parts in service. Creep failure is inevitable if parts are continuously subjected to loads at increased temperatures, even if it may take a long time to occur. In any industry that operates safety-critical metal components at high temperatures and stress, scheduled maintenance for part inspection and replacement can avoid catastrophic creep failures. This allows manufacturers to have more control over their operations.
Alternatively, using parts with higher melting temperatures and larger grain boundaries can reduce the creep rate and help prevent creep failure. This is because parts are less prone to the effects of creep if the material’s melting temperature is higher. Additionally, larger grain sizes help prevent creep from deforming a material’s microstructure.
What Will Happen if Creep Failure Is Not Prevented?
If creep failure is not prevented, severe consequences may occur. From reduced load-bearing capacity and loss of functionality to deformation and distortion of parts, to catastrophic rupture, creep failure is something that should be avoided. Additionally, damage to property and life can result in enormous legal costs.
How Can 3D Printing Help Prevent Creep Failures?
3D printing with metals or plastics can benefit engineers in avoiding creep failures in several ways. For one, 3D printing enables manufacturers to design parts in such a way that the effects of creep are mitigated — either by manipulating part geometry or tailoring microstructures. Manipulating part geometries to mitigate the effects of creep can be achieved by designing parts capable of sustaining the stresses that will be experienced due to creep while tailoring microstructures can be achieved by printing amorphous plastics compared to crystalline and semi-crystalline plastics. Secondly, 3D printing can allow manufacturers to test and validate different part geometries and examine the effects of creep on them. 3D printing helps contribute to the scientific and engineering communities’ understanding of creep.
To learn more, see our guide on What Are 3D Printers Used For.
Summary
This article presented creep failure, explained it, and discussed how it works and its various examples. To learn more about creep failure, contact a Xometry representative.
Xometry provides a wide range of manufacturing capabilities and other value-added services for all of your prototyping and production needs. Visit our website to learn more or to request a free, no-obligation quote.
Disclaimer
The content appearing on this webpage is for informational purposes only. Xometry makes no representation or warranty of any kind, be it expressed or implied, as to the accuracy, completeness, or validity of the information. Any performance parameters, geometric tolerances, specific design features, quality and types of materials, or processes should not be inferred to represent what will be delivered by third-party suppliers or manufacturers through Xometry’s network. Buyers seeking quotes for parts are responsible for defining the specific requirements for those parts. Please refer to our terms and conditions for more information.
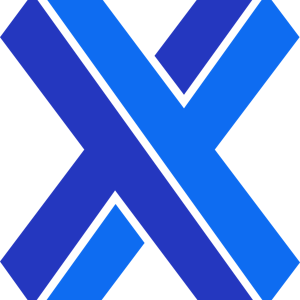