Duplex stainless steels are a family of corrosion-resistant alloys known for their exceptional combination of strength and resistance to corrosion. These materials exhibit a dual-phase microstructure of austenite and ferrite, which imparts unique properties suitable for a wide range of applications. Duplex stainless steels find extensive use in industries such as: oil & gas, chemical processing, marine engineering, and construction, offering robust solutions for challenging environments. In this article, we explore the key characteristics, compositions, and applications of duplex stainless steel.
What Is Duplex Steel?
Duplex steel, or duplex stainless steel, is a type of stainless steel that has a two-phase microstructure consisting of approximately equal amounts (~50%) of austenite and ferrite phases, although in commercial alloys the ratio may be 40/60. This combination of phases gives duplex steel its name "duplex," meaning "two-fold" or "double." The key characteristic of duplex steel is its excellent combination of properties from both austenitic and ferritic stainless steels which are known for their corrosion resistance as well as their mechanical strength.
Similar to other stainless steel families, the specific metallurgical composition of duplex steel varies depending on the grade. However, typical components found in duplex stainless steel include: carbon, manganese, silicon, chromium, nickel, phosphorus, and sulfur. Additionally, molybdenum, nitrogen, and copper may be incorporated to tailor the material's properties further, allowing for a customized final product with desired characteristics.
In general, duplex stainless steel can be categorized into four main groups: lean, standard, super, and hyper.
To learn more, see our guide on Carbon Steel Material Properties.
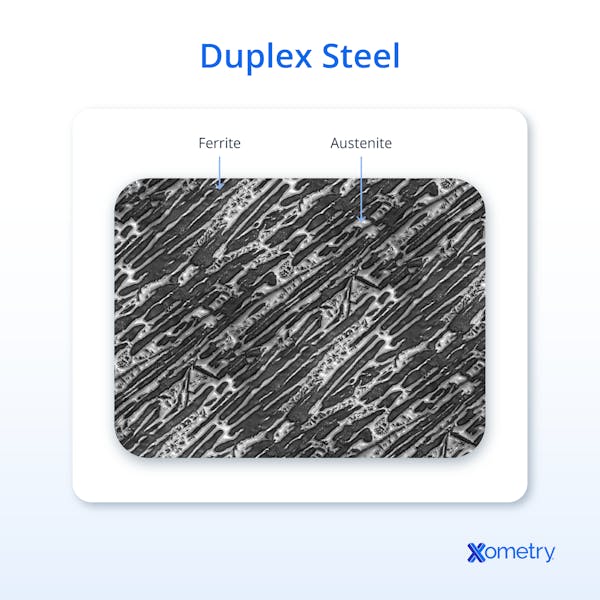
What Is Duplex Steel Used For?
Duplex stainless steels have a wide range of practical applications across industries. They are used in: chemical processing for pressure vessels, tanks, piping, and heat exchangers due to their corrosion resistance and strength. In the oil & gas sector, duplex stainless steels are employed in tubing, piping, and heat exchangers for their ability to withstand harsh conditions. Marine environments benefit from their resistance to chloride-induced corrosion, while the paper and pulp industry uses them in critical equipment.
How Is Duplex Steel Made?
The production of duplex stainless steel is a multistage process of steelmaking and forming. It begins with the combination of raw materials containing: nickel, iron ore, chromium, molybdenum, and other alloying elements in an electric arc furnace, in which they are melted and mixed together. This melted steel is moved to an argon oxygen decarburization (AOD) converter, in which critical metallurgical processes take place. In the AOD converter, gasses are removed from the molten steel, and the final composition is adjusted by adding alloying elements. Afterwards, the steel is transferred to a ladle furnace, so that modifications can be made to its inclusions.
Once the molten steel is prepared, it can be cast into continuously cast blooms or solid ingots. The molten mixture of duplex steel initially solidifies as a completely ferritic solid. However, as it cools to room temperature, approximately half of the material undergoes a phase transformation from ferritic to austenitic.
These blooms or ingots are then processed further, typically by reheating and forging or rolling to achieve the required diameter. Afterward, solution annealing, a heat treatment process, is applied to ensure the consistency of the bar’s internal structure. Following annealing, the bars are quenched to achieve the desired properties. Finally, to provide a consistent surface finish, the bars undergo mechanical peeling to remove the irregular surface, resulting in the finished duplex stainless steel product.
What Is the Chemical Composition of Duplex Steel?
The chemical composition (% by weight) and PREN number of some common duplex steels are outlined in Tables 1-4:
Name | UNS | En No. | C | Mn | Si | Cr | Ni | Mo | N | Cu | Other | PREN |
---|---|---|---|---|---|---|---|---|---|---|---|---|
Name 2101 | UNS S32101 | En No. 1.4162 | C 0.04 | Mn 4.0–6.0 | Si 1 | Cr 21.0–22.0 | Ni 1.35–1.70 | Mo 0.1–0.8 | N 0.20–0.25 | Cu 0.1–0.8 | Other - | PREN 25–27 |
Name 2202 | UNS S32202 | En No. 1.4062 | C 0.03 | Mn 2 | Si 1 | Cr 21.5–24.0 | Ni 1.00–2.80 | Mo 0.45 | N 0.18–0.26 | Cu - | Other - | PREN 25–28 |
Name 2304 | UNS S32304 | En No. 1.4362 | C 0.03 | Mn 2.5 | Si 1 | Cr 21.5–24.5 | Ni 3.0–5.5 | Mo 0.05–0.6 | N - | Cu - | Other - | PREN 25–28 |
Name 2102 | UNS S82011 | En No. - | C 0.03 | Mn 2.0–3.0 | Si 1 | Cr 20.5–23.5 | Ni 1.0–2.0 | Mo 0.1–1.0 | N 0.15–0.27 | Cu 0.50–0.60 | Other - | PREN 25–27 |
Table Credit: https://www.imoa.info/molybdenum-uses/molybdenum-grade-stainless-steels/duplex-stainless-steel.php
Name | UNS | En No. | C | Mn | Si | Cr | Ni | Mo | N | Cu | Other | PREN |
---|---|---|---|---|---|---|---|---|---|---|---|---|
Name 2205 | UNS S31803 | En No. 1.4462 | C 0.03 | Mn 2 | Si 1 | Cr 21.0–23.0 | Ni 4.5–6.5 | Mo 2.5–3.5 | N 0.08–0.20 | Cu - | Other - | PREN 33–35 |
UNS S32205 | En No. 1.4462 | C 0.03 | Mn 2 | Si 1 | Cr 22.0–23.0 | Ni 4.5–6.5 | Mo 3.0–3.5 | N 0.14–0.20 | Cu - | Other - | PREN 35–36 |
Table Credit: https://www.imoa.info/molybdenum-uses/molybdenum-grade-stainless-steels/duplex-stainless-steel.php
Name | UNS | En No. | C | Mn | Si | Cr | Ni | Mo | N | Cu | Other | PREN |
---|---|---|---|---|---|---|---|---|---|---|---|---|
Name 255 | UNS S32550 | En No. S32760 | C 0.04 | Mn 1.5 | Si 1 | Cr 24.0–27.0 | Ni 4.5–6.5 | Mo 2.9–3.9 | N 0.10–0.25 | Cu 1.5–2.5 | Other - | PREN 38–41 |
Name 2507 | UNS S32750 | En No. 1.441 | C 0.03 | Mn 1.2 | Si 0.8 | Cr 24.0–26.0 | Ni 6.0–8.0 | Mo 3.0–5.0 | N 0.24–0.32 | Cu 0.5 | Other - | PREN 40–43 |
Name Z100 | UNS S32760 | En No. 1.4501 | C 0.03 | Mn 1 | Si 1 | Cr 24.0–26.0 | Ni 6.0–8.0 | Mo 3.0–4.0 | N 0.20–0.30 | Cu 0.50–1.00 | Other W 0.5–1.0 | PREN 40–43 |
Table Credit: https://www.imoa.info/molybdenum-uses/molybdenum-grade-stainless-steels/duplex-stainless-steel.php
Name | UNS | En No. | C | Mn | Si | Cr | Ni | Mo | N | Cu | Other | PREN |
---|---|---|---|---|---|---|---|---|---|---|---|---|
Name 2707 | UNS S32707 | En No. - | C 0.03 | Mn 1.5 | Si 0.5 | Cr 26.0–29.0 | Ni 5.5–9.5 | Mo 4.0–5.0 | N 0.30–0.50 | Cu 1 | Other Co 0.5–2.0 | PREN 49–50 |
UNS S33207 | En No. - | C 0.03 | Mn 1.5 | Si 0.8 | Cr 29.0–33.0 | Ni 6.0–9.0 | Mo 3.0–5.0 | N 0.40–0.60 | Cu 1 | PREN 52–53 |
Table Credit: https://www.imoa.info/molybdenum-uses/molybdenum-grade-stainless-steels/duplex-stainless-steel.php
What Is the Carbon Content of Duplex Steel?
The carbon content of duplex steel is typically below 0.04%. The chromium (Cr) and nickel (Ni) content can be adjusted within the ranges of 20% to 30% and below 9.5%, respectively. Duplex stainless steel also contains minor alloying elements such as: molybdenum, nitrogen, tungsten, and copper.
What Are the Properties of Duplex Steel?
The physical and mechanical properties of duplex stainless steel are listed in Tables 5 and 6, respectively:
Property | 2205 | UR52N+ |
---|---|---|
Property Density (g/cm^3) | 2205 7.805 | UR52N+ 7.81 |
Property Electrical Resistivity (Ω.m) | 2205 0.85 x 10^-6 | UR52N+ 0.85 x 10^-6 |
Table Credit: https://www.azom.com/article.aspx?ArticleID=2870
Grade | ASTM A789 Grade S32520 Heat-Treated | ASTM A790 Grade S31803 Heat-Treated | ASTM A790 Grade S32304 Heat-Treated | ASTM A815 Grade S32550 Heat-Treated | ASTM A815 Grade S32205 Heat-Treated |
---|---|---|---|---|---|
Grade Elastic Modulus | ASTM A789 Grade S32520 Heat-Treated 200 GPa | ASTM A790 Grade S31803 Heat-Treated 200 GPa | ASTM A790 Grade S32304 Heat-Treated 200 GPa | ASTM A815 Grade S32550 Heat-Treated 200 GPa | ASTM A815 Grade S32205 Heat-Treated 200 GPa |
Grade Elongation | ASTM A789 Grade S32520 Heat-Treated 25 % | ASTM A790 Grade S31803 Heat-Treated 25 % | ASTM A790 Grade S32304 Heat-Treated 25 % | ASTM A815 Grade S32550 Heat-Treated 15 % | ASTM A815 Grade S32205 Heat-Treated 20 % |
Grade Tensile Strength | ASTM A789 Grade S32520 Heat-Treated 770 MPa | ASTM A790 Grade S31803 Heat-Treated 620 MPa | ASTM A790 Grade S32304 Heat-Treated 600 MPa | ASTM A815 Grade S32550 Heat-Treated 800 MPa | ASTM A815 Grade S32205 Heat-Treated 655 MPa |
Grade Brinell hardness | ASTM A789 Grade S32520 Heat-Treated 310 | ASTM A790 Grade S31803 Heat-Treated 290 | ASTM A790 Grade S32304 Heat-Treated 290 | ASTM A815 Grade S32550 Heat-Treated 302 | ASTM A815 Grade S32205 Heat-Treated 290 |
Grade Yield Strength | ASTM A789 Grade S32520 Heat-Treated 550 MPa | ASTM A790 Grade S31803 Heat-Treated 450 MPa | ASTM A790 Grade S32304 Heat-Treated 400 MPa | ASTM A815 Grade S32550 Heat-Treated 550 MPa | ASTM A815 Grade S32205 Heat-Treated 450 MPa |
Table Credit: https://whatispiping.com/duplex-stainless-steel-dss/?expand_article=1
Is Duplex Steel Magnetic?
Yes. Duplex stainless steel possesses a microstructure that combines both austenitic and ferritic grains. While austenitic microstructures are non-magnetic, ferritic microstructures are magnetic. Consequently, duplex grades are also regarded as magnetic due to this dual-phase composition.
Machinability Rating of Duplex Steel
Duplex stainless steels are often regarded as challenging materials for machining, with a machinability rating of around 28%. This is primarily due to their high austenite content, elevated nitrogen levels, and increased alloy composition. The difficulty in machining duplex stainless steel stems from factors such as: a high work-hardening rate, exceptional strength, low thermal conductivity, limited fracture toughness, and the propensity for built-up-edge (BUE) formation.
What Are the Thermal Properties of Duplex Steel?
The thermal properties of duplex steels are given in Table 7:
Grade | ASTM A789 Grade S32520 Heat-Treated | ASTM A790 Grade S31803 Heat-Treated | ASTM A790 Grade S32304 Heat-Treated | ASTM A815 Grade S32550 Heat-Treated | ASTM A815 Grade S32205 Heat-Treated |
---|---|---|---|---|---|
Grade Thermal Expansion coefficient | ASTM A789 Grade S32520 Heat-Treated 1 x 10-5 /K | ASTM A790 Grade S31803 Heat-Treated 1 x 10-5 /K | ASTM A790 Grade S32304 Heat-Treated 1 x 10-5 /K | ASTM A815 Grade S32550 Heat-Treated 1 x 10-5 /K | ASTM A815 Grade S32205 Heat-Treated 1 x 10-5 /K |
Grade Specific Heat capacity | ASTM A789 Grade S32520 Heat-Treated 440–502 J/(kg·K) | ASTM A790 Grade S31803 Heat-Treated 440–502 J/(kg·K) | ASTM A790 Grade S32304 Heat-Treated 440–502 J/(kg·K) | ASTM A815 Grade S32550 Heat-Treated 440–502 J/(kg·K) | ASTM A815 Grade S32205 Heat-Treated 440–502 J/(kg·K) |
Grade Thermal Conductivity | ASTM A789 Grade S32520 Heat-Treated 13–30 W/(m·K) | ASTM A790 Grade S31803 Heat-Treated 13–30 W/(m·K) | ASTM A790 Grade S32304 Heat-Treated 13–30 W/(m·K) | ASTM A815 Grade S32550 Heat-Treated 13–30 W/(m·K) | ASTM A815 Grade S32205 Heat-Treated 13–30 W/(m·K) |
Table Credit: https://whatispiping.com/duplex-stainless-steel-dss/?expand_article=1
What Are the Common Forms of Duplex Steel Material?
Duplex steel is available in various forms to meet diverse industrial and engineering needs including:
Fittings and Flanges
Duplex steel fittings and flanges are essential components in piping systems, providing robust connections that can withstand harsh environments. Their corrosion resistance and strength make them suitable for applications in industries such as: oil & gas, chemical processing, and marine engineering.
Pipe
Duplex steel pipes are widely used for conveying fluids and gasses in demanding settings. They offer superior resistance to corrosion, making them ideal for transporting corrosive substances in industries like: petrochemicals, pulp and paper, and desalination.
Plate
Duplex steel plates are flat, broad sheets of material that find applications in structural and industrial projects. Their high strength and corrosion resistance make them valuable for constructing pressure vessels, storage tanks, and various structural components.
Sheet
Duplex steel sheets are thinner than plates and are often used in applications requiring lightweight yet durable materials. They are commonly employed in architectural cladding, kitchen equipment, and decorative panels.
Tube
Duplex steel tubes are used for conveying liquids or gasses, especially in situations in which corrosion resistance is paramount. They are integral in industries like: chemical processing, offshore drilling, and heat exchanger manufacturing.
Bar
Duplex steel bars come in various shapes, including: round, square, and hexagonal, and are used in applications such as: shafts, fasteners, and valves. Their combination of strength and corrosion resistance makes them versatile in mechanical and industrial contexts.
Hot-Rolled
Hot rolling is a processing method used to form duplex steel into various shapes, such as: plates, sheets, and bars. The material is heated and passed through rollers to achieve the desired shape and dimensions. Hot-rolled duplex steel is characterized by improved mechanical properties.
Annealed
Annealing is a heat treatment process that involves heating duplex steel to a specific temperature and then slowly cooling it to relieve stress and improve its ductility. Annealed duplex steel is more malleable and suitable for forming and machining.
Cold-Drawn
Cold drawing is a cold-working process that involves pulling duplex steel through a die to reduce its diameter or achieve a specific shape. Cold-drawn duplex steel is known for its enhanced surface finish and dimensional accuracy, making it suitable for precision applications.
What Are the Equivalents of Duplex Steel?
The most commonly used duplex stainless steel is 2205, renowned for its outstanding corrosion resistance and impressive strength. The name "2205" derives from its typical composition, consisting of 22% chromium and 5% nickel. Additional designations for 2205 are detailed in the table provided below:
Grade | Euronorm | UNS | BS |
---|---|---|---|
Grade 2205 | Euronorm 1.4462 | UNS S31803
S32205 | BS 318S13 |
Table Credit: https://www.azom.com/article.aspx?ArticleID=2870
What Are the Advantages of Using Duplex Steel?
Duplex stainless steel offers many advantages compared to traditional austenitic and ferritic stainless steel grades. These are:
- Often exhibit up to twice the strength of both austenitic and ferritic stainless steel grades.
- Impressive formability under pressure, surpassing that of ferritic grades, and offers superior toughness.
- Depending on the specific grade, duplex stainless steels provide comparable or even superior corrosion resistance when compared to common austenitic grades. Alloys with elevated levels of nitrogen, molybdenum, and chromium exhibit remarkable resistance to crevice corrosion and chloride pitting.
- Offers superior mechanical properties when compared to ferritic stainless steel, especially in terms of plastic toughness.
- Exhibits significantly improved cold-working and cold-forming capabilities compared to ferritic stainless steel.
- Generally, no preheating or post-weld heat treatment is required, simplifying the welding process.
- The versatility of duplex stainless steel extends to a broader range of applications compared to ferritic stainless steel.
What Are the Disadvantages of Using Duplex Steel?
While duplex stainless steel offers numerous advantages, it is not without its disadvantages. Here are some of the disadvantages associated with using duplex steel:
- Can be more expensive than standard austenitic stainless steel. The higher costs are primarily due to the increased alloying elements, such as chromium, nickel, molybdenum, and nitrogen, which enhance its corrosion resistance and mechanical properties.
- May not be as readily available as some other stainless steel grades, such as 304 or 316.
- Has temperature limitations, and its use above a certain temperature range (typically above 250 °C) can lead to embrittlement caused by spinodal decomposition and a reduction in its corrosion resistance and mechanical properties.
What Is the Difference Between Duplex Steel and 304 Stainless Steel?
Duplex stainless steel, particularly duplex 2205 stainless steel, stands apart from austenitic 304 stainless steel primarily in three key aspects. First, its yield strength is notably higher—more than double that of regular austenitic stainless steel. This elevated strength allows for the construction of storage tanks and pressure vessels with thinner walls, ultimately reducing material costs. Second, it boasts exceptional resistance to stress corrosion cracking, surpassing the capabilities of austenitic stainless steel in this regard. Finally, its mechanical properties are superior, with the capacity to absorb more energy under dynamic or static loading conditions, making it more resilient in scenarios involving sudden accidents like collisions or explosions.
However, it's essential to consider some drawbacks when comparing duplex stainless steel to austenitic stainless steel. Duplex steel has limited versatility in applications, necessitating temperature control below 250 °C. Its plastic toughness is lower, resulting in inferior cold and hot processing and forming performance compared to austenitic stainless steel. Furthermore, it has a medium-temperature brittle zone, requiring strict control in heat treatment and welding processes to prevent harmful phase formation and performance deterioration.
What Is the Difference Between Duplex Steel and 316 Stainless Steel?
The main difference between duplex and 316 stainless steel is in their composition. Duplex stainless steel has more chromium, molybdenum, and nitrogen, making it stronger and corrosion-resistant at higher temperatures. While 316 stainless steel exhibits excellent resistance to corrosive environments within the 300 family, duplex stainless steel offers significantly greater resistance to corrosive pitting, especially in the presence of chloride. Duplex steel is also more ductile, allowing for complex shaping.
In terms of strength and durability, duplex steel outperforms 316, due to its resistance to various corrosive environments. It's ideal for high-stress applications like valves and pumps that need longevity.
To learn more, see our guide on 316 Stainless Steel Properties.
What Is the Difference Between Duplex Steel and 201 Stainless Steel?
Duplex steel and 201 stainless steel exhibit distinct differences in composition, properties, and applications. Duplex stainless steel is characterized by its dual-phase microstructure, comprising both austenitic and ferritic phases, typically in a 50-50 ratio. It contains higher levels of chromium, nickel, molybdenum, and nitrogen, providing exceptional corrosion resistance, especially in chloride-rich environments, and superior mechanical properties, including strength and toughness. Consequently, duplex steel finds its niche in demanding applications like: chemical processing, marine environments, and structural components in which both corrosion resistance and strength are critical.
In contrast, 201 stainless steel is an austenitic stainless steel with a simpler alloy composition, primarily consisting of iron, chromium, and nickel. While it offers good general corrosion resistance, it doesn't match the corrosion resistance and mechanical properties of duplex stainless steel. As a result, 201 stainless steel is commonly used in less-demanding applications, including: kitchen appliances, cookware, utensils, and decorative trim, for which corrosion resistance and mechanical strength requirements are less stringent.
Summary
This article presented duplex steel, explained it, and discussed its various uses and composition. To learn more about duplex steel, contact a Xometry representative.
Xometry provides a wide range of manufacturing capabilities and other value-added services for all of your prototyping and production needs. Visit our website to learn more or to request a free, no-obligation quote.
Disclaimer
The content appearing on this webpage is for informational purposes only. Xometry makes no representation or warranty of any kind, be it expressed or implied, as to the accuracy, completeness, or validity of the information. Any performance parameters, geometric tolerances, specific design features, quality and types of materials, or processes should not be inferred to represent what will be delivered by third-party suppliers or manufacturers through Xometry’s network. Buyers seeking quotes for parts are responsible for defining the specific requirements for those parts. Please refer to our terms and conditions for more information.
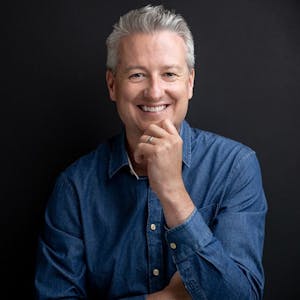