Polyethylene (as a class of materials) is manufactured in a range of densities and commercial and scientific names. Commonly referred to as polythene, its IUPAC (International Union of Pure and Applied Chemistry) names are polyethylene or poly(methylene). Manufacturers produce PE of various densities; this property is heavily influenced by the degree and form of side branching from the polymer chain. Side branches reduce crystallinity and density, so produced material can range from ultra-low to ultra-high molecular weight; with many densities in between being achieved by blending various densities. The range of densities of polyethylene represents a spectrum of properties and suitability for wide and overlapping applications, including HDPE (High-Density Polyethylene). This article will compare polyethylene vs. HDPE in terms of applications, costs, and properties.
It must be noted that, in this article, polyethylene is used as the name for the originally manufactured version of the material, which is a heavy side-branched and highly amorphous form that has the lowest density in the polymer family.
What is HDPE?
HDPE (high-density polyethylene) is the generic name for a spectrum of higher molecular weight polyethylene variants. These differ from the Ultra-High Molecular Weight form, UHMWPE, which is a material class. All polyethylene forms are chemically similar, being long chains of CH2 which have been created by high temperature and high pressure, catalyzing breakdown byproducts of diazomethane in a reaction chamber. For more information, see our guide on High-Density Polyethylene.
HDPE is characterized by particularly low levels of side-branching groups on the main polymer chains, and no long side branches at all. This allows the chains to lie close together in very orderly, pseudo-crystalline arrangements that allow higher-density materials. The degree of side branching is a result of variations in process conditions and catalysts, and it is now a highly controllable property; so materials with a range of molecular weights can be manufactured, with properties that are dependent on this variance. The increased density and crystallinity make HDPE stronger, less elastic, and more resistant to load distortion than LDPE. Typical HDPE densities are between 0.933 and 1.27 g/cm3
What Is Polyethylene?
Polyethylene (PE) is a thermoplastic polymer made from ethylene gas. It is chemically identical to HDPE in that it is formed from long chains of CH2 but differentiated by the regularity and size of side branches of shorter or longer chains of CH2 monomer. The side branches are randomly orientated and can be extensive, making networks of attached chains. PE should not be confused with Linear Low-Density Polyethylene (LLDPE) which is characterized by frequent, randomly oriented side branches of a single CH2 monomer.
The effect of the extensive side branching present in PE is to force greater distance between chains, which reduces the density and increases the potential for chains to tangle, pushing them further apart. The reduced density compared with HDPE makes PE a softer and weaker material, but more elastic and more resistant to shock loading. Typical PE densities are between 0.915 and 0.926 g/cm3. For more information, see our guide on PE material.
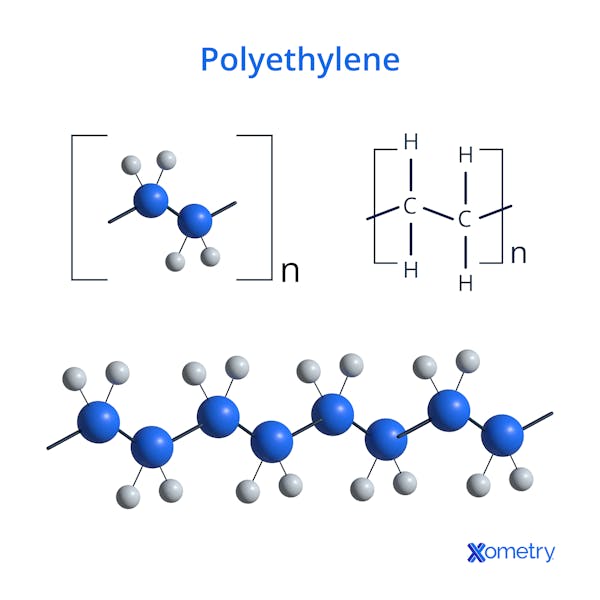
HDPE vs. Polyethylene: Applications and Uses
HDPE applications include:
- Packaging: Used for crates, trays, milk bottles, caps for PET bottles, fuel cans, drums, and industrial fluid containers.
- Consumer Goods: trash bins, garden equipment and furniture, storage bins, children's toys, and playground equipment.
- Fibers and Textiles: Because of its generally high tensile strength, HDPE is used for agricultural applications, such as ropes, fishing nets, ball-sports goal nets, and industrial fabrics.
- Plumbing: Pipes and fittings for LPG gas supply, water supply, sewage handling, drainage, outfalls, rain collectors, and septic tanks.
- Automotive: Fuel tanks (both entire tanks and liner coatings), cable insulation, cable ties and retainers, and body-mounted clips.
Polyethylene on the other hand is commonly applied in:
- Packaging: Packs for pharmaceuticals, household chemicals, and food items (squeeze bottles). Also caps and hinged closures, tamper-evident caps with shear tabs, bin liners, and food packaging films.
- Pipes and Fittings: Water pipes, garden hoses, piping, and fittings in food production due to plasticity and low taint risk.
- Various Goods: Kitchenwares, toys, agricultural films, wiring sheaths, insulators, cable ducting.
HDPE vs. Polyethylene: Physical Properties
Table 1 below lists the differences between HDPE and polyethylene in terms of physical properties:
Property | HDPE value (metric) | Polyethylene value (metric) |
---|---|---|
Property Density | HDPE
value (metric) 0.933–1.27 g/cm3 | Polyethylene
value (metric) 0.915–0.96 g/cm3 |
Property Hardness, Shore D | HDPE
value (metric) 55–69 | Polyethylene
value (metric) 42–56 |
Property Tensile strength, ultimate | HDPE
value (metric) 15.2–45 MPa | Polyethylene
value (metric) 8.96–54 MPa |
Property Tensile strength, yield | HDPE
value (metric) 2.69–200 MPa | Polyethylene
value (metric) 7.6–14 MPa |
Property Elongation at break | HDPE
value (metric) 3–1900% | Polyethylene
value (metric) 226–650% |
Property Modulus of elasticity | HDPE
value (metric) 0.483–1.45 GPa | Polyethylene
value (metric) 0.152–0.29 GPa |
Property Flexural yield strength | HDPE
value (metric) 16.5–91 MPa | Polyethylene
value (metric) 14–21 MPa |
Property Flexural modulus | HDPE
value (metric) 0.5–4.83 GPa | Polyethylene
value (metric) 0.07–0.276 GPa |
Property Dielectric constant | HDPE
value (metric) 2.0–2.6 | Polyethylene
value (metric) 2.27–2.29 |
Property Melting point | HDPE
value (metric) 120–130 °C | Polyethylene
value (metric) 102–113 °C |
Property Max service temperature | HDPE
value (metric) 80–120 °C | Polyethylene
value (metric) 80–100 °C |
HDPE vs. Polyethylene: Recyclability and Sustainability
PE (polyethylene) in film form can be effectively recycled into second-grade production material once sorted. But sorting issues and the processing before pellet extrusion prevent much of this from being commercially viable. The film waste must be well sorted, to reduce the incidence of mixed material being reprocessed; otherwise, the properties of the resultant material are easily degraded. This sorting is not easy, as very low levels of colored films will significantly devalue a “clear” end product. The film materials also cause chronic tangling in the shredding process, requiring high labor costs to correct.
The sorted film is shredded, washed, dried, and extruded to form “new” pellets which are of high quality. They are unlikely, however, in the second incarnation to be used in film manufacturing or in food-grade applications. Most are used for low-grade applications in building and agricultural materials.
Recycled material maintains a fairly high price, but the process is barely profitable because of the handling difficulties. Very little PE (polyethylene) is effectively recycled; instead, it ends up in incineration or landfill. Most kerbside recycling collection points do not accept PE (carrying any recycling mark or the ♶ identifier) but treat that which is left by consumers as waste material to be removed and disposed of.
HDPE (high-density polyethylene) film materials are generally used in heavier (or thicker) sections and colored, and are relatively easy to sort for high purity. The process does not require the separation of colored, natural, and clear materials at the sorting stage—all colors are processed together.
Like PE, sorted plastic is first washed, then dried, and shredded to produce greater uniformity and easier processing. The shredded material is then heated to a melting point and extruded to form a standard molding-pellet feedstock. The equipment to perform this process is low cost, but there is considerable labor in the sorting stage—where much of the market value is added—as multi-polymer blend material has virtually zero value.
The end result is high-quality, second-grade material that generally has a dark color and can be used for a range of otherwise normal applications, substituting for virgin material, or more often as a second-grade minority component with otherwise new material.
All PE (polyethylene) materials are commercially produced from hydrocarbon source materials and represent a significant environmental burden. Very little HDPE (high-density polyethylene) is recycled, though claims of 28% recycling of milk containers are made in some markets. Despite this, overall estimates of recycling volume are unreliable and very low.
Overall, PE materials are highly recyclable and can produce good resultant products for 10 or more cycles (potentially many more, if perfectly sorted and treated gently). However, real recycling rates worldwide are minimal as a percentage of the total made. Most are lost to the environment, put in landfills, or burned for disposal or power generation.
HDPE vs. Polyethylene: Cost
Like all of the PE family, HDPE is a low-price material that is manufactured in huge quantities and is generally considered a commodity material. The price for virgin material is around $8.50 per kg, reduced to $2.50 for recycled material.
Polyethylene (PE) has a considerably lower cost than HDPE, generally selling as granules in the $0.90–$1.10 price range. Recycled clear PE is available at a similar or slightly lower price, and it is generally used as a 10–20% addition to virgin material, saving a few cents per kg.
Alternative Materials to HDPE and Polyethylene
Polyethylene (PE) has a wide range of applications and these suit different alternative materials. For films, some available options are: BOPP (biaxially oriented polypropylene), PVC (polyvinyl chloride), polycaprolactone, PET, and PLA (polylactic acid). For pipes and fittings, the alternative materials are: UPVC (unplasticized polyvinyl chloride), HDPE, PEX (radiation cross-linked PE), metal—copper, iron, plated and stainless steel, etc. For homewares, some alternative materials are: ABS (acrylonitrile butadiene styrene), PET, HIPS (high impact polystyrene), and PP (polypropylene).
HDPE (high-density polyethylene) has a wide range of applications, but they are narrower in scope, and alternatives are more straightforward. For most applications, alternatives are PE, PET, PEX, ABS, PP, and rubber-modified PP.
Summary
This article presented HDPE and polyethylene, explained each of them, and discussed their various applications. To learn more about HDPE and polyethylene, contact a Xometry representative.
Xometry provides a wide range of manufacturing capabilities and other value-added services for all of your prototyping and production needs. Visit our website to learn more or to request a free, no-obligation quote.
Disclaimer
The content appearing on this webpage is for informational purposes only. Xometry makes no representation or warranty of any kind, be it expressed or implied, as to the accuracy, completeness, or validity of the information. Any performance parameters, geometric tolerances, specific design features, quality and types of materials, or processes should not be inferred to represent what will be delivered by third-party suppliers or manufacturers through Xometry’s network. Buyers seeking quotes for parts are responsible for defining the specific requirements for those parts. Please refer to our terms and conditions for more information.
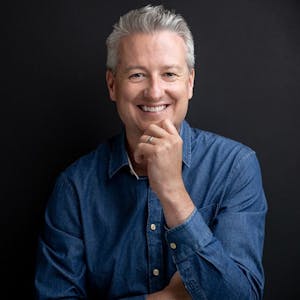