Manufacturers around the world love fiber lasers, and so do many of our customers—but this doesn’t come as a surprise. These lasers have extremely high optical gain, even able to produce a kilowatt of continuous output power. They are very accurate, even on complex designs, and don’t really leave behind any burns, rough edges, or thermal deformation. Because the beam is produced in the fiber’s small core, it doesn’t require a separate optical medium making it very stable and simple to maintain, as well as high in quality and straight, without much diffraction. They have fairly low operating costs, and there are no blowers or moving parts—another plus for maintenance.
To learn more about fiber lasers, how they work, and when to use them, read on.
What Are Fiber Lasers?
A fiber laser is a solid-state type of laser, meaning that it uses solid materials to make a beam instead of liquids or gases. The beam that comes out is extremely focused, and it works with pump laser diodes that give the laser the power to create light. A very thin optical fiber is what guides this light, which then gets absorbed and amplified into the concentrated beam. The optical fiber itself is doped, which adds a rare-earth element to it, making the process possible. Changing the doping substance, like dysprosium (2600–3400 nm), holmium (2025–2200 nm), or thulium (1900–2500 nm), will create different wavelengths. Here’s a diagram of a fiber laser:
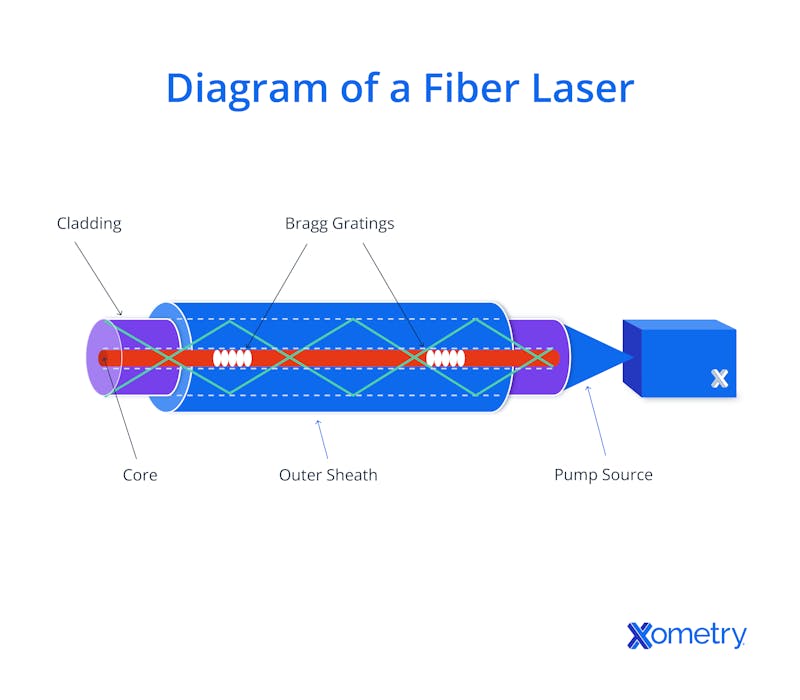
You can use fiber laser beams to cut, weld, engrave, and clean materials, although it’s mostly used on metals like carbon steel, copper, and stainless steel. You can also use it on certain plastics like acrylic and polyoxymethylene, as well as graphite (but not glass fiber, leather, ceramics, polycarbonate, ABS, HDPE, polystyrene, or polypropylene foam).
Fiber lasers consist of several components that differ between types, but if we take a fiber laser cutting machine as an example, we’ll find that it’s made up of eight primary parts: the laser source, the laser cutting head, the servo motor, a cooling device, an air cutting system, a laser host (bed, beam, table, and Z-axis system), the control system, and a stabilizer. With a 30–50% power conversion rate, they’re way more energy efficient than CO2 lasers’ 10–15% (which is why they’re so often used in sectors like automotive, home appliances, fitness equipment, lighting, and decor/metal art).
They can usually be manual or automated and come in handy in so many situations, like laser marking, where 1064 nm emission wavelength ytterbium-doped fiber lasers can leave sharp and durable imprints on metal and plastic surfaces. Another is laser cleaning where they’re used to remove paint, oxide, and rust from metal surfaces. There’s also laser welding that’s fast, precise, and without much distortion, and laser cutting for difficult cuts and tight tolerances. Although operating costs are relatively low, it’s worth noting that the components can be quite pricey, and the delivery fiber can’t be separated from the source, so replacement can be tricky.
How it Works
Several things need to happen before the laser shoots out and gets to work. First, the laser diodes, aka the pump source, convert electricity to light (technically photons), which is injected into the fiber optic. These make the light by using two oppositely charged semiconductors. The positively charged electrodes take spare electrons from the negative side, and as the electron jumps from one electrode to the other, it releases a photon.
The light is then pumped through the fiber optic cables—these use a fiber core and cladding to concentrate the light in one single direction and produce a laser beam. The light travels through the fiber’s core which is made from silica glass. When it gets to the doped fiber, it interacts with the rare-earth elements, raising the electron’s energy levels and causing a population inversion to make the beam. During this phase, several electrons are in an excited state and they release photons when they calm back down. Some of them can only produce photons with a certain wavelength, but when those photons come into contact with other excited electrons, those electrons release photons of a similar wavelength (this is always different depending on the doping component of the laser cavity, which is why each type of fiber laser will only produce a single wavelength).
These then drop down to a lower energy level in a phase referred to as “stimulated emission”—the “SE” part of the “LASER” acronym. When it passes through, the light re-excites the electrons that have relaxed, and they release photons before relaxing again. The process repeats until it eventually reaches a steady state, creating a stable stream of light.
Once that’s sorted, the next thing to think about is shaping the laser light, which can be done using things like beam expanders and lenses. If you’re working on a project that requires the laser to actually penetrate the material—like laser texturing and engraving—then you’ll want to use a short focal lens.
Types
Fiber lasers are not all the same. They can be categorized based on several factors, which we list below.
- Source: The type of chemical used to dope the laser source.
- Operation: Lasers with a high peak strength could be q-switched, mode-locked, or gain-switched. Some are even set to a predetermined repetition rate, like pulsed lasers, and others can continuously churn out the same amount of energy, like continuous wave fiber lasers.
- Mode: This is the size of an optical fiber’s core. Multi-mode ranges from 50–100 micrometers in width, and single-mode produces the most efficient beam between 8–9 micrometers.
- Power: This is the average power of the laser beam measured in watts. The higher the power, the more energy it will produce (and quickly, too).
Fiber Laser Machines
There are lots of fiber laser machines on the market today, and we’ve put the most common ones in the comparison table below.
Machine | Power (W) | Material Compatibility | Approximate Cost | Size |
---|---|---|---|---|
Machine Omtech | Power (W) 20, 30, 50 | Material Compatibility Metals, precious metals, brick, stone, hard plastics | Approximate Cost $3,099 | Size Varies (commonly 175x175 mm or 200x200 mm) |
Machine Cloudray AirMarker2 | Power (W) 20 | Material Compatibility Metals, some hard plastics | Approximate Cost $2,100 | Size 110x110 mm |
Machine Triumph 3D | Power (W) 30, 50 | Material Compatibility Metals, precious metals, laminates, foils, hard plastics, films | Approximate Cost From $4,999 | Size 110x110 mm or 210x210 mm |
Machine Dihorse Desktop | Power (W) 20 | Material Compatibility Most metals, some nonmetals | Approximate Cost From $4,769 | Size 110x110 mm up to 300x300 mm |
Machine Ten-High Portable | Power (W) 20–50 | Material Compatibility Most metals, some nonmetals | Approximate Cost $3,242 | Size 150x150 mm or 200x200 mm |
Fiber Laser Machines
How Does a Fiber Laser’s Power Scale?
Fiber lasers can only produce more power up to a certain point because of constraints like Brillouin and Raman scattering (SBS or SRS), as well as their own short length. For more power, special setups and extra components (i.e., amplifiers, switches) are needed. SBS interacts with low-frequency vibrations (acoustic phonons) and only happens when going backward, and SRS goes with high-frequency vibrations (optical phonons) and can happen in both directions along the fiber.
Optical fibers go through two main types of nonlinear effects. The first is the Kerr effect, where the refractive index of the fiber will change based on the light’s intensity, which can cause three things to happen depending on the signal: CPM (cross-phase modulation), SPM (self-phase modulation), and FWM (four-wave mixing). The second is when the light transfers some of its energy to the fiber material through inelastic scattering, which could cause stimulated SBS or SRS. Any type of stimulated scattering can increase the amount of light in the fiber. When the input power goes beyond a certain point, the scattered light’s intensity can increase massively. SRS is usually considered better because it has a larger frequency shift and a wider bandwidth.
Are There Any Alternatives to Fiber Lasers?
Yes, gas/CO2 lasers and crystal laser cutters are a couple of alternatives. CO2 lasers have a wavelength of 10.6 mm and can cut through materials like acrylic, leather, some plastics and foams, glass, paper-based materials, and wood. When compared to a fiber laser of the same output, a CO2 laser has more energy to go through thicker materials and can leave a smoother finish.
Compared to CO2 lasers, crystal laser cutters have shorter wavelengths, which means they have a higher intensity and can cut through even thicker and stronger materials. The downside of these, though, is that they can deteriorate quicker because of their high power output. They’re good for things like metals, ceramics, and plastics.
How Long Do Fiber Lasers Last Compared to Other Types?
Fiber lasers can last a very long time; much longer than CO2 and crystal lasers, and that’s mainly because they don’t have any moving parts. Usually, fiber lasers last around 50,000 to 100,000 hours of operation before any major maintenance is needed. To give you an idea of how impressive this is, CO2 lasers usually require maintenance after around 20,000 to 30,000 hours of operation, and crystal lasers require maintenance quite often. That’s why fiber lasers are perfect for industrial use.
How Xometry Can Help
If you have any questions about fiber lasers or anything else related to manufacturing, one of Xometry’s representatives will be happy to help you. We also offer a huge variety of manufacturing services like CNC machining, 3D printing, and laser cutting. You can get started today by requesting a free, no-obligation quote.
Disclaimer
The content appearing on this webpage is for informational purposes only. Xometry makes no representation or warranty of any kind, be it expressed or implied, as to the accuracy, completeness, or validity of the information. Any performance parameters, geometric tolerances, specific design features, quality and types of materials, or processes should not be inferred to represent what will be delivered by third-party suppliers or manufacturers through Xometry’s network. Buyers seeking quotes for parts are responsible for defining the specific requirements for those parts. Please refer to our terms and conditions for more information.
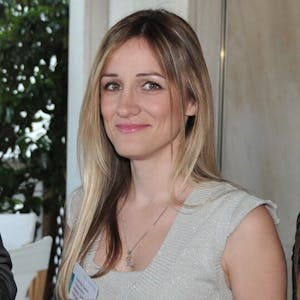