Injection molding is a popular manufacturing process used to make parts in high volumes with consistent quality. The process involves injecting molten plastic into the cavity of a mold in the shape of the final part, which is typically made from metal. As anyone familiar with the process will tell you, the traditional mold-making method can be time-consuming and expensive—not really worth the effort for small runs or custom parts. Enter 3D-printed molds: a cheaper and faster alternative ideal for low-volume production and prototyping.
What Are 3D-Printed Molds for Injection Molding?
Molds shape molten plastic into final products, which take on the shape and finish of the mold’s cavity. Making these molds via 3D printing has been a game-changer. Unlike CNC machining, 3D printing doesn’t need any specialized expertise, reducing labor costs. The materials used—typically plastic—are far less expensive than aluminum or steel, and the overall cost can be up to 90% lower than traditional molds. While traditional molds can take weeks or months (yes, months!) to make, even the most complex 3D-printed molds can be ready in a matter of days. This means that any changes needed can quickly and easily be made before you scale up the production. Although 3D-printed molds have a shorter lifespan, they can still make up to 10,000 parts, depending on the material.
3D-printed molds are best suited for components up to 164 cm³ (metal molds win this round as they can accommodate much larger parts). Another area where metal molds are superior is in durability—3D-printed molds tend to struggle under the high temperatures and pressures of injection molding. They’re also prone to shrinkage and warping during cooling, which is especially a nuisance for tight-tolerance parts. In general, polymers have lower thermal conductivity than metal, so 3D-printed molds slow down the injection molding process (although making the mold is undoubtedly much quicker). Basically, you’ll want to stick to your metal molds for high-precision, high-volume manufacturing.
Considerations
The success of the injection molding process depends largely on the quality of the 3D-printed mold, so there are a few things to keep in mind when you’re making it. Firstly, the mold material must be able to withstand high temperatures and pressure without warping or melting, so choose wisely. The mold’s design is equally as important. Uniform wall thickness helps prevent warping and defects, while avoiding sharp corners reduces stress points and improves durability. Gate location should be optimized to ensure proper material flow, and runner systems should be incorporated to prevent flash, or excess material escaping the mold. Tweaks like adjusting clamping force and injection pressure can further improve results.
Surface quality is also an important consideration. 3D-printed molds tend to have a rougher surface than aluminum or steel molds. This can impact the final product’s texture and may require post-processing to achieve a smoother finish. For parts requiring a high-quality surface, metal molds are the better choice. Refining the surface finish minimizes roughness and enhances part quality. Finally, draft angles of 1.5° to 2° make part ejection easier and prevent damage to the molded piece, improving both mold longevity and product quality. Before full production, the mold needs to be thoroughly tested and validated to find any design flaws or weaknesses so that you can make the adjustments before going ahead with production. You’ll also have to choose a mold that matches the scale of the part you want to make.
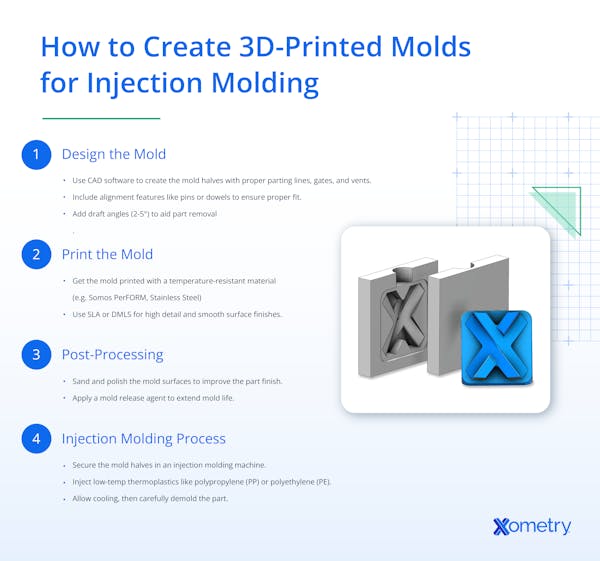
Step-by-Step Guide
So, let’s take a look at the 5 steps involved in creating a 3D-printed mold for injection molding.
1. Design the Mold in CAD
Start by creating the mold design in CAD software, considering part geometry, material choice, gate location, and cooling channels. Choose a heat-resistant, rigid material to withstand injection pressure, and design the mold to minimize support contact for a smoother finish. Adding air vents helps prevent defects like trapped air, and cooling channels speed up production.
2. Export the CAD File
Once the design is finalized, export it as an STL file, the standard format for 3D printing. Other supported file types include FBX, OBJ, 3MF, PLY, G-Code, X3G, and AMF.
3. 3D Print the Mold
Import the STL file into 3D printing software and choose a printing method based on cost, strength, and surface finish. FDM (Fused Deposition Modeling) is a cost-effective method but may need sanding or chemical smoothing. For smoother, high-detail molds, SLA/DLP (Stereolithography/Digital Light Processing) is best, while material jetting can create multi-material/color molds with fine detail. For strong molds with good surface quality, you can use nylon with the SLS (Selective Laser Sintering) process.
4. Fit the Mold to a Metal Frame
Once printed, the mold needs to be secured in a metal mold base for support during injection molding. This can either be done with mold inserts in an aluminum frame, which are more precise, reduce defects like warping, and ensure even pressure distribution, or fully 3D-printed molds that don’t need a frame. These do, however, require more material, increasing both the cost and risk of warping.
5. Start the Process
Once the mold is fitted to the metal frame, it is ready for the injection molding process. During the injection molding process, the mold is clamped shut, and molten material is injected into the mold through the sprue bushing. The liquid fills the mold cavities and takes on the shape of the part to be produced. After the material cools and solidifies, the mold is opened, and the part is removed.
FAQs on 3D-Printed Molds for Injection Molding
Can you 3D print molds for all injection molding methods?
Not quite. While 3D-printed molds are great for prototyping and small production runs, they’re not suitable for every injection molding method—especially those requiring high precision, extreme durability, or high-volume output. Plastic 3D-printed molds can’t always withstand the high pressures and temperatures used in certain injection molding processes. Metal 3D-printed molds are stronger but still have limitations compared to traditionally machined steel molds.
3D-printed molds degrade faster, making them less ideal for high-volume manufacturing. Some injection molding techniques require ultra-smooth or complex mold surfaces that 3D printing can’t always achieve. Although 3D-printed molds work well for certain applications, traditional molds are a better choice for processes like gas-assisted molding, metal injection molding (MIM), or high-temperature thermoplastics.
What post-processing can be done on 3D-printed injection molding molds?
To improve the surface finish and accuracy of 3D-printed molds, many manufacturers perform some post-processing techniques, like sanding and polishing, which can help smooth out the surface. You could also use a protective ceramic coating on the printed mold to reduce heat degradation issues, in addition to getting a smoother finish.
Can you make 3D-printed injection molding molds with PLA?
Unfortunately not. While PLA (polylactic acid) is a popular thermoplastic material for 3D printing, it has a relatively low melting temperature compared to materials like ABS, polycarbonate, and nylon. PLA is brittle and lacks the impact strength needed for injection molding, making it prone to cracking under high stress. It also degrades at high temperatures and can release toxic fumes, which makes it unsafe for the high-temperature, high-pressure environment of injection molding.
How Xometry Can Help
We have instant quoting available at Xometry for both injection molding and various types of 3D printing methods. Get a better idea of pricing for HP MJF, SLS, fused deposition modeling, injection-molded surface finishes, and more by uploading your designs to the Xometry Instant Quoting Engine®!
Disclaimer
The content appearing on this webpage is for informational purposes only. Xometry makes no representation or warranty of any kind, be it expressed or implied, as to the accuracy, completeness, or validity of the information. Any performance parameters, geometric tolerances, specific design features, quality and types of materials, or processes should not be inferred to represent what will be delivered by third-party suppliers or manufacturers through Xometry’s network. Buyers seeking quotes for parts are responsible for defining the specific requirements for those parts. Please refer to our terms and conditions for more information.
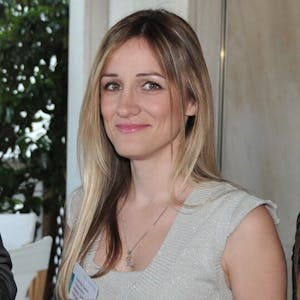