3D printing uses a wide array of materials, each with unique properties and applications. Choosing the right material for 3D printing is crucial, as it directly impacts the quality, durability, and functionality of your printed objects. Each material has its unique properties and use cases, making it essential to understand the strengths and weaknesses of each option. This article will discuss the most common and best materials used for 3D printing, their properties, and their applications.
Material | Advantages | Disadvantages |
---|---|---|
Material ABS (Acrylonitrile Butadiene Styrene) | Advantages Impact- resistant, wear-resistant, low cost | Disadvantages Difficult to print due to warping, poor bed adhesion |
Material ASA (Acrylic Styrene Acrylonitrile) | Advantages UV-resistant, impact-resistant, wear-resistant | Disadvantages High cost, dangerous fumes during printing |
Material PP (Polypropylene ) | Advantages Impact-resistant, fatigue resistant, good surface finish, good chemical resistance | Disadvantages Difficult to print due to warping and poor bed adhesion |
Material PLA (Polylactic Acid) | Advantages Cheap and easy to print | Disadvantages Brittle, degrades in outdoor environments |
Material Carbon Fiber Filled | Advantages High-strength parts | Disadvantages Can block nozzles, high cost |
Material Nylon (Synthetic Polymers) | Advantages Excellent mechanical properties, low friction | Disadvantages Absorbs moisture |
Material HIPS (High Impact Polystyrene) | Advantages Low weight, can be dissolved with a solvent | Disadvantages High printing temperature |
Material PC (Polycarbonate) | Advantages One of the strongest 3D printer filaments, transparent | Disadvantages Difficult to print, high cost |
Material PVA (Polyvinyl Alcohol) | Advantages Dissolves in water | Disadvantages Can only be used for support material |
Material Resins | Advantages Smooth surface, versatile | Disadvantages Design limits, high cost |
Material Nitinol | Advantages Withstand substantial bending, one of the strongest materials | Disadvantages Difficult to print |
Material Flexible (made of Thermoplastic Elastomers) | Advantages Rubber-like behavior | Disadvantages High cost, difficult to print |
Material Wood-Based Filament | Advantages Aesthetically pleasing finish | Disadvantages Poor overall strength, can block nozzle |
Material Metal Filled Filaments | Advantages Aesthetically pleasing finish | Disadvantages Poor overall strength |
Material PETG (Glycol Modified version of PET) | Advantages Excellent mechanical properties, easier to print than ABS | Disadvantages Imperfect interlayer adhesion |
Material Graphite and Graphene | Advantages High strength, remarkable electrical conductivity | Disadvantages High cost, poor efficiency |
The Best Materials for 3D Printing
Listed below are some of the best materials for 3D printing:
1. ABS (Acrylonitrile Butadiene Styrene)
ABS (Acrylonitrile Butadiene Styrene) is one of the most widely adopted 3D printing materials available today. Derived from petroleum feedstocks, ABS boasts a prominent role in injection molding and finds its application in numerous household commodities. Notable examples include its use in: crafting enduring Lego bricks, protective phone cases, and resilient bicycle helmets. These products benefit from ABS's remarkable attributes such as outstanding durability, robustness, and resistance to elevated temperatures.
In commercial applications, ABS shines in rapid prototyping. However, in the hobbyist 3D printing arena, it receives somewhat less attention. This is primarily attributed to its slightly trickier printing characteristics, with a tendency to warp unless printed within an enclosed and heated build chamber.
ABS boasts affordability and an impressive strength-to-weight ratio. In addition, it facilitates straightforward post-processing and offers a diverse color palette. It's important to note that ABS emits odorous and potentially harmful volatile organic compounds (VOCs) during the printing process. To mitigate this, it's advisable to print in well-ventilated spaces or within an enclosure, and maintaining distance from the printing area is a prudent precaution.
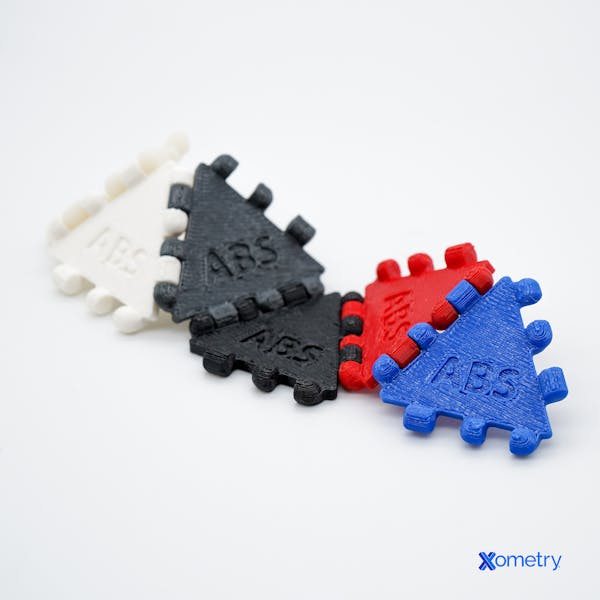
2. ASA (Acrylic Styrene Acrylonitrile)
ASA (Acrylonitrile Styrene Acrylate) is a 3D printing material positioned as a superior alternative to ABS. It boasts enhanced thermal resistance, improved mechanical properties, and heightened resistance to a broader spectrum of chemicals. Unlike ABS, ASA retains its color even under UV exposure. Moreover, ASA exhibits reduced warping tendencies compared to ABS, simplifying the printing process significantly.
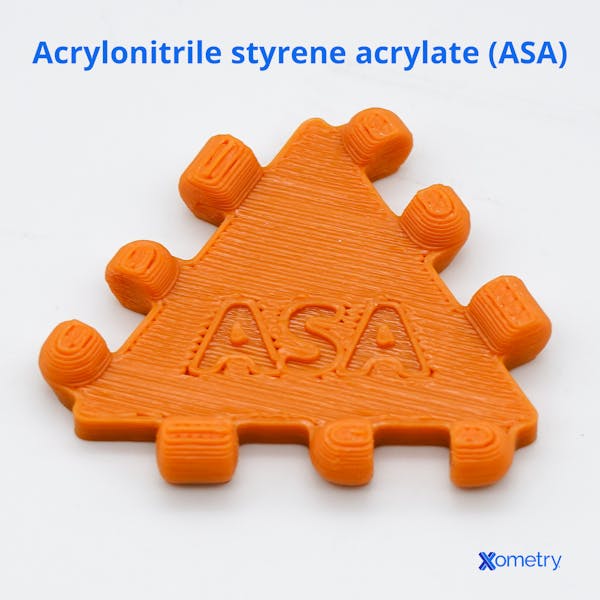
3. PP (Polypropylene )
Polypropylene (PP) is a versatile material with numerous applications beyond 3D printing. It is primarily renowned for its exceptional chemical resistance and resistance to fatigue. This semi-crystalline plastic has a tendency to warp easily during the 3D printing process and struggles to adhere to the build plate. Despite these challenges, PP is highly valuable for for creating living hinges, leveraging its impressive fatigue resistance.
For more information see our guide on PP (Polypropylene).
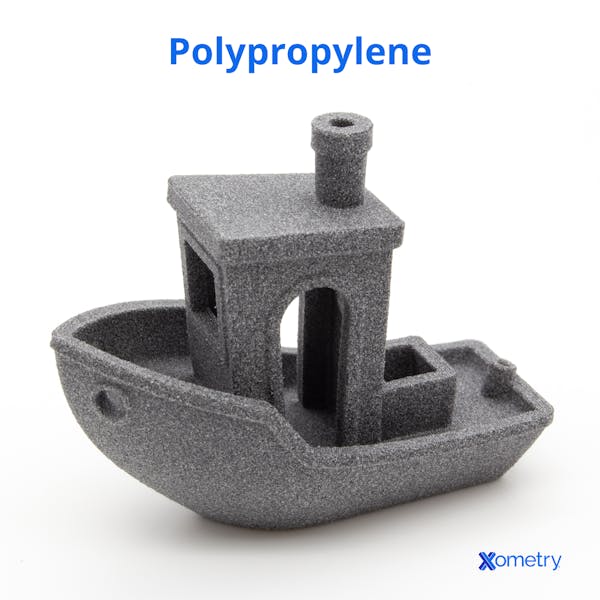
4. PLA
PLA, short for polylactic acid, is the most popular 3D printing filament material. It's ideal for prototypes and objects that won't be exposed to high temperatures or heavy stress. Derived from renewable sources like corn starch or sugar cane, PLA is hailed for its eco-friendly origins. While it can be recycled at industrial facilities, it's important to note that it's not biodegradable in standard home environments. What sets PLA apart is its remarkable ease of use. It has a relatively low printing temperature (190–215 °C) and minimal warping tendencies. Moreover, PLA is virtually odorless during printing, providing a pleasant and comfortable experience. Its compatibility with single-use food contact further broadens its applications. However, PLA does come with limitations, such as lower durability compared to materials like ABS or PETG and sensitivity to high temperatures.
Some variations of PLA include: silk-like PLA, lightweight PLA, recycled PLA, color-changing PLA, glitter or sparkly PLA, wood PLA, biodegradable PLA, flexible and soft PLA, carbon-fiber-infused PLA for added strength, glow-in-the-dark PLA, conductive PLA for electronics projects, high-temperature PLA for improved heat resistance, translucent PLA for a unique aesthetic, and even metal-infused PLA for a metallic finish.
To learn more, see our guide on PLA (Polylactic Acid).
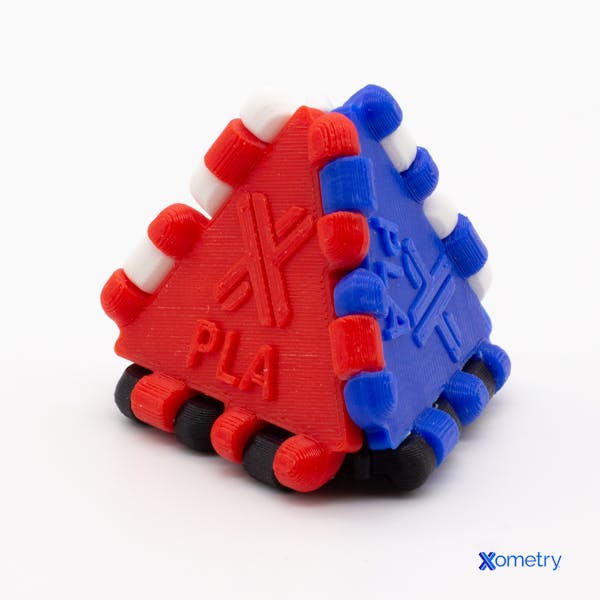
5. Carbon Fiber
Carbon fiber particles, when incorporated into common 3D printing materials like ABS, PLA, or PETG, enhance the material's overall strength, setting it apart from fillers like wood or metal which typically reduce strength. However, it's important to note that carbon-fiber-filled plastics can lead to nozzle clogging and increased wear on standard 3D printing nozzles. To mitigate these issues, it is advisable to use hardened steel nozzles when working with carbon-fiber-infused materials.
6. Nylon
Polyamide (PA), commonly referred to as nylon, is a robust and enduring 3D printing material renowned for its exceptional toughness and resistance to both high temperatures and impacts. It boasts commendable tensile and mechanical strength, making it a favored choice for a wide spectrum of applications.
Nylon is frequently reinforced with various fibers such as carbon, glass, and Kevlar®, or it can be embedded with continuous carbon fiber for enhanced reinforcement. Its utilization is widespread in high-end engineering domains, encompassing the creation of gears, jigs, fixtures, and tooling. Additionally, nylon is available in powder form, expanding its range of applications.
While not as easy to print with as materials like PLA or PETG, nylon remains a viable choice. To work with nylon effectively, a high-temperature nozzle, capable of reaching up to 300 °C, may be necessary. Furthermore, proper storage is very important, as nylon readily absorbs moisture when exposed to open air. Moisture absorption can lead to material degradation, resulting in subpar print quality and reduced strength.
7. HIPS
High impact polystyrene (HIPS) is a unique 3D printing material composed of a blend of polystyrene plastic and polybutadiene rubber. This combination yields a material that boasts impressive toughness and flexibility.
While HIPS shares similarities with ABS, it distinguishes itself by its exceptional resistance to high-impact forces. Additionally, it offers versatility through ease of painting, machining capabilities, and compatibility with a wide range of adhesives. HIPS also holds an FDA-compliant status for food processing applications.
In 3D printing, HIPS is mainly used as a support material. Its key advantage lies in its solubility in limonene solution, eliminating the need for labor-intensive removal methods like abrasives or cutting tools. This property simplifies the printing process. Moreover, HIPS can be smoothed to achieve glossy surfaces, a feat often challenging with PLA. It's worth noting that while limonene is an accessible solution derived from lemon peels, it may have adverse effects on 3D printing materials other than HIPS.
8. Polycarbonate
Polycarbonate filament, often referred to as PC, is a transparent and durable material well-suited for high-temperature applications due to its exceptionally high transition temperature (approximately 150 °C). PC exhibits natural flexibility, making it suitable for various situations, even those involving significant stress on the printed object.
Nevertheless, it's important to note that PC filament is prone to absorbing moisture from its environment. This moisture absorption can lead to issues such as warping or layer separation during printing. To mitigate these challenges, it's advisable to store PC filament in an airtight container whenever possible. Additionally, given the high printing temperatures required, using heat protection measures is essential when working with PC.
For more information, see our guide on PC (Polycarbonate).
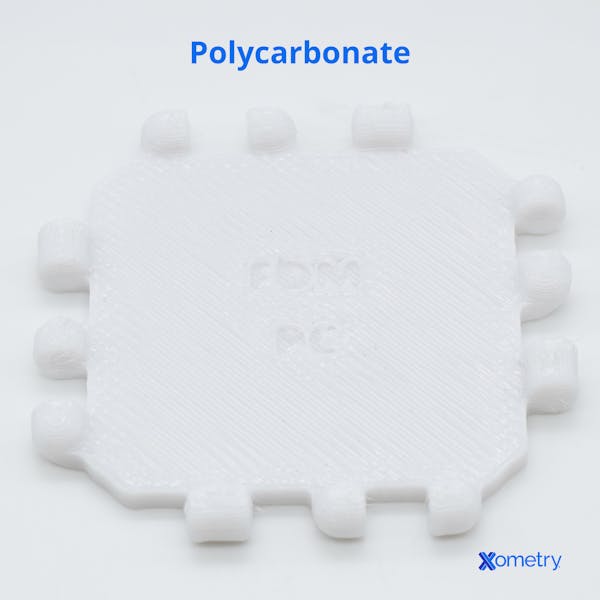
9. PVA
Similar to HIPS, Polyvinyl Alcohol (PVA) is primarily used as a support material in 3D printing. It isn't particularly suitable for creating standalone objects due to its soft and biodegradable nature. However, the key distinction between PVA and HIPS is that PVA completely dissolves in warm water. This eliminates the need for additional solutions or products, simplifying the 3D printing process.
One notable drawback of PVA is its tendency to clog the nozzle if heated without active printing. Additionally, it's essential to store any surplus PVA in an airtight container to prevent moisture absorption.
10. Resins
Resin is a versatile material in 3D printing. It encompasses various technologies like stereolithography (SLA), digital light processing (DLP), and liquid crystal display (LCD) in vat polymerization, as well as material jetting methods like PolyJet. Resin excels in high-detail printing and is often strong enough for post-print machining.
High-temperature resins are cost-effective for creating injection molds for small-scale prototypes. Standard resins suit applications like conceptual and functional models. Rapid resins, also known as "raft resin," cure quickly and prevent part deformation. Tough resins mimic ABS and are ideal for functional parts. Water-washable resins simplify cleaning with water instead of alcohol. Flexible resins offer elasticity, similar to TPU, for applications requiring high flexibility. Plant-based resins use eco-friendly sources like soybeans. Castable and wax resins facilitate jewelry manufacturing by creating wax molds. Transparent/clear resins, although requiring post-processing, are suitable for medical and model-making applications. Glow-in-the-dark resin produces luminescent models, and biocompatible and dental resins meet medical and dental requirements, but compliance with varying regulations is essential for medical applications.
FREE SLA 3D Printing Design Guide
11. Nitinol
Nitinol is a widely used material in medical implants and is highly prized for its remarkable super-elasticity. Comprising a blend of nickel and titanium, nitinol can withstand substantial bending without fracturing. Remarkably, even when folded in half, the material can effortlessly revert to its initial shape. Consequently, nitinol stands out as one of the strongest materials distinguished by its exceptional flexibility.
12. Flexible Filaments
TPEs, or thermoplastic elastomers, belong to a class of materials that combine plastic and rubber properties. Notable examples include TPU (thermoplastic polyurethane) and TPC (thermoplastic copolyester), among others. These plastics exhibit remarkable softness and flexibility. This makes them increasingly popular in additive manufacturing for creating deformable parts that can be stretched or bent without losing their shape. TPUs, in particular, offer exceptional durability and excel in resisting abrasion, oils, chemicals, and extreme temperatures, outperforming TPE filaments. On the other hand, TPC stands out with its high-temperature resilience and excellent UV resistance, finding valuable applications in the biomedical field, wearable tech, and medical devices. TPEs are also available in powder and resin forms.
While these materials offer versatility, achieving successful 3D prints requires precise control over the printing process, including the use of properly dried filament, appropriate bed heating, nozzle temperatures, and print speeds.
13. Wood
Wood 3D filament is a composite material typically consisting of PLA infused with wood fibers. There's a wide variety of wood-PLA 3D printer filaments available today, offering options like pine, cedar, birch, ebony, willow, cherry, bamboo, cork, coconut, and olive. However, using wood-based filament comes with trade-offs. While it provides an aesthetically pleasing and tactile appeal, it sacrifices some flexibility and strength compared to other materials. Additionally, wood-filled filament can accelerate the wear and tear of your 3D printer's nozzle, so be mindful when using it. It's essential to control the printing temperature, as excessive heat can lead to a burnt or caramelized appearance. Nonetheless, you can enhance the final look of your wooden creations with post-print processing techniques such as cutting, sanding, or painting.
14. Metal
Metal is the second most popular material in 3D printing, primarily through the direct metal laser sintering (DMLS) process, although Selective Laser Melting (SLS) and metal FDM (Fused Deposition Modeling) can also be used. DMLS has been adopted by aerospace manufacturers to streamline the production of component parts, reducing time and complexity.
DMLS is revolutionizing machine manufacturing, enabling unprecedented speed and volume, potentially producing metal parts with superior strength compared to conventionally refined metals. In this process, metal is used as dust and hardened through firing, eliminating the need for casting. Metal dust is commonly employed for prototyping metal instruments but has also produced finished products and field-ready parts, including medical devices. This method reduces the number of components required in the final product.
DMLS covers a range of metals, including: titanium, stainless steel, aluminum, tool steel, bronze, and nickel alloys.
15. PET and PETG Filaments
PETG is a filament derived from polyethylene terephthalate (PET), the same material found in plastic water bottles. However, in PETG, a portion of the ethylene glycol is substituted with CHDM (cyclohexanedimethanol), signified by the "G" in its name, which stands for "glycol-modified." This modification yields a filament that boasts greater clarity, reduced brittleness, and enhanced ease of use compared to its unmodified PET counterpart.
PETG serves as a suitable alternative to ABS, offering heat-resistant properties without the production of toxic fumes. Besides this, PETG is also popular for being food-safe. Additionally, PETG can be post-processed by sanding, akin to PLA. While most FDM printers compatible with PLA can also handle PETG, it may demand a bit more calibration and effort for optimal results.
The advantages of PETG include its ease of printing compared to ABS, the ability to maintain a smooth finish, and convenient storage properties. However, it comes with certain drawbacks, such as the requirement for high printing temperatures, which can potentially lead to wear and tear on printer components over time. While PETG may not excel in bridging due to its high stickiness, this attribute translates into excellent layer adhesion. It is worth noting that PETG is more hygroscopic than PLA, making it susceptible to issues like substantial stringing and moisture absorption from the air if left exposed.
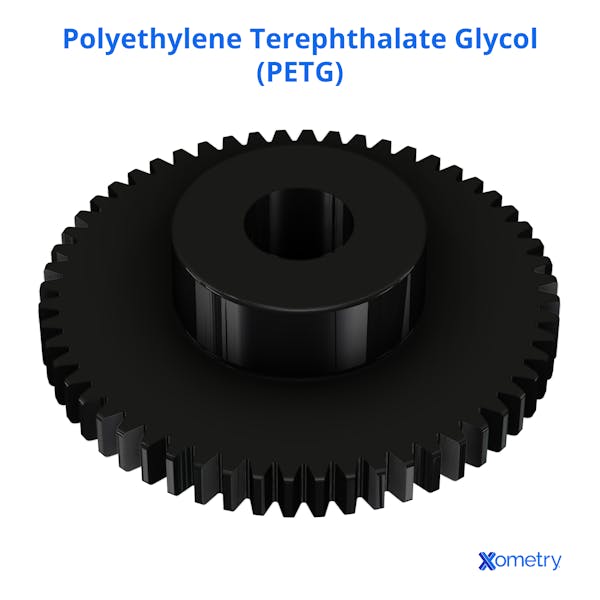
16. Graphite and Graphene
Graphene has gained widespread popularity in 3D printing due to its exceptional strength and electrical conductivity. This material is particularly suitable for crafting flexible components, like touchscreens. Beyond this, graphene is also used in the construction of solar panels and building components. Advocates of graphene tout its remarkable flexibility among 3D-printable materials, emphasizing its lightweight nature, formidable strength, and outstanding electrical conductivity.
Why You Should Know the Materials Used in 3D Printing
Knowing the different material options in 3D printing allows users to make informed decisions on which material will be best suited for different applications. This also ensures that the printed object meets the standards and functional requirements. Secondly, it helps users make cost-efficient choices, optimizing their printing processes and budgets. Thirdly, awareness of the environmental impact of different materials promotes sustainable and eco-friendly printing practices. Additionally, knowledge of material compatibility with specific 3D printers ensures a smooth printing process and minimizes equipment damage. Moreover, in industries like healthcare and aerospace, compliance with strict regulations regarding materials is essential to avoid legal and safety issues. For more information, see our article on the guide to 3D printing.
What are the Most Commonly Used Materials in 3D Printing?
PLA (Polylactic Acid) is the most popular 3D printing plastic for non-industrial use while nylon is the most common plastic for industrial applications.
The selection of material for a 3D printed component largely relies on its intended purpose, with crucial attributes tailored to the specific application. Here are several fundamental properties essential for general 3D printing:
- Elongation
- Melting Temperature
- Heat Deflection Temperature
- Impact Strength
- Flexural Strength
- Tensile Strength
- Hardness
The Best Materials for Stereolithography (SLA) 3D Printing
SLA 3D printing boasts exceptional versatility. It suits a variety of resin formulations with extensive optical, mechanical, and thermal properties that can align with standard, engineering, and industrial thermoplastics. Common resins that are used in 3D printing include:
- Standard resin.
- Clear resin.
- Draft resin.
- Tough and Durable resin.
- Rigid resin.
- Polyurethane resin.
- Flexible and elastic resin.
- Medical and dental resin.
- ESD (electrostatic discharge) resin.
- Flame retardant resin.
- Ceramic resin.
The Best Materials for Selective Laser Sintering (SLS) 3D Printing
While SLS has a more limited material selection compared to FDM and SLA, the available materials exhibit outstanding mechanical properties. The materials that can be printed with SLS 3D printing include:
- Nylon and composites
- TPU
The Best Materials for Fused Deposition Modeling (FDM) 3D Printing
The primary materials for FDM 3D printing are ABS and PLA, with various combinations available. Advanced FDM printers can also accommodate specialized materials known for enhanced characteristics such as increased heat tolerance, impact resistance, chemical resilience, and rigidity. Some of the other materials that can be used for FDM 3D printing include:
- PETG
- Nylon
- TPU
- PVA
- HIPS
- Composites (e.g., fiberglass, carbon fiber, Kevlar®)
The Best Materials for Digital Light Process (DLP) 3D Printing
Digital Light Processing (DLP) 3D printers typically work with photopolymer resins. These resins are specially formulated for use in DLP technology and are designed to be cured or solidified when exposed to UV light. Some common types of DLP resin materials include:
- Standard resins
- Engineering resins
- Dental resins
- Jewelry resins
- Castable resins
- Flexible resins
The Best Materials for Multi Jet Fusion (MJF) 3D Printing
Multi Jet Fusion (MJF) technology was initially compatible only with nylon PA 12 powders, which remains the most common choice. However, the range of compatible materials has grown over the years, thanks to MJF's popularity and industry collaborations. Some MJF-compatible materials include:
- Estane 3D TPU – M95A from Lubrizol.
- Estane 3D TPU M88A.
- High Reusability (HR) PA 12 Nylon.
- HR PA 11.
- HR PA 12 Glass Bead (GB).
- HR PA 12 W (white).
- HR PP enabled by BASF Production.
- TPA from Evonik/HP.
- Ultrasint® TPU01 from BASF.
The Best Materials for Direct Metal Laser Sintering (DMLS) 3D Printing
Direct Metal Laser Sintering (DMLS) is a metal 3D printing technology that uses powdered metal materials. DMLS is suitable for creating strong, complex metal components. Common materials for DMLS include:
- Stainless Steel
- Aluminum
- Titanium
- Cobalt Chrome
- Inconel®
The Best Materials for PolyJet 3D Printing
PolyJet is a 3D printing technology that utilizes an inkjet-style process to create highly detailed and precise 3D objects. It operates by jetting tiny droplets of photopolymer resin onto a build platform layer by layer, which are then cured with UV light to solidify. Here is a list of materials that can be printed with PolyJet 3D printing:
- Digital materials
- Digital ABS plastic
- Rubber-Like materials
- High-Temperature Materials
- Transparent materials
- Rigid Opaque Materials
- Simulated Polypropylene materials
- Biocompatible Materials
The Best Materials for Electron Beam Melting (EBM) 3D Printing
Electron Beam Melting (EBM) 3D printing is restricted to a specific set of metals due to its process requirements. Titanium and chromium-cobalt alloys are among the most common materials used in EBM. Additionally, certain steel powders and Inconel® 718 can be used for this method. It's important to note that EBM relies on electrically conductive materials to construct components, which excludes the use of polymeric and ceramic materials in this particular 3D printing process.
Materials That Can Be 3D Printed at Home
Here’s a list of some materials that have been successfully printed in a home environment:
- PLA
- ABS
- PVA
- Nylon
- Polycarbonate
- Ethylene
- Wood filament
- Printing pastes (e.g., sugar, chocolate, silicone, wax, and clay)
Materials That Cannot Be 3D Printed
The list of materials that cannot be 3D printed include:
- Flammable materials
- Stone or other hard natural materials
- Cloth/fabrics
- Liquids (other than resin) and gases
How to Select the Best 3D Printing Material
To select the correct material it is important to define the application. Below is a list of general rules to follow when choosing the best 3D printing material:
- If high strength is needed, a polycarbonate or carbon-fiber-filled material may be ideal.
- If a basic jig is required, then a cheaper material like PLA may be better suited.
- If the application is a safety-critical component, then it is always safest to consult with the machine supplier as well as the material supplier to understand how any given material will perform.
How Xometry Can Help
Xometry provides a wide range of manufacturing capabilities, including 3D printing and other value-added services for all of your prototyping and production needs. Visit our website to learn more or to request a 3D printing quote.
Copyright and Trademark Notices
- Kevlar® is a trademark of E. I. DuPont de Nemours and Company.
- Inconel® is a registered trademark of Special Metals Corporation.
- Ultrasint® is a registered trademark of the BASF Group
Disclaimer
The content appearing on this webpage is for informational purposes only. Xometry makes no representation or warranty of any kind, be it expressed or implied, as to the accuracy, completeness, or validity of the information. Any performance parameters, geometric tolerances, specific design features, quality and types of materials, or processes should not be inferred to represent what will be delivered by third-party suppliers or manufacturers through Xometry’s network. Buyers seeking quotes for parts are responsible for defining the specific requirements for those parts. Please refer to our terms and conditions for more information.
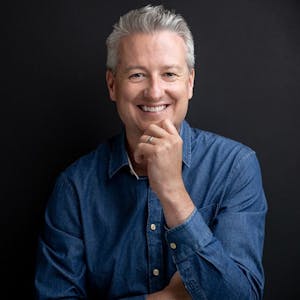