HDPE (high-density polyethylene) is a thermoplastic manufactured from petroleum byproducts. It represents a spectrum of properties and suitability for wide and overlapping applications. HDPE is widely employed in making packaging for household chemicals such as wet and dry detergents. It is also used for making caps/closures for LDPE bottles for similar applications and PET bottles for water and carbonated drinks.
Acrylonitrile Butadiene Styrene (ABS) is among the most widely used moderate-strength copolymers, employed in every market sector. It combines toughness, resilience, chemical stability, good cosmetic capability, and a low price. This has made ABS the go-to solution for domestic/consumer products and product enclosures across most sectors. It is also commonly found in automotive bumpers and external body components, automotive interior finishing, and many more applications. ABS comes in a variety of grades, with various additives that can enhance some characteristics. A prime example is a blend of ABS and 10–20% polycarbonate (ABS-PC) that increases the strength of ABS by 15–25%. This article will compare HDPE vs. ABS in terms of applications, uses, properties, and costs.
What Is HDPE?
HDPE (high-density polyethylene) is the generic name for a spectrum of higher molecular weight polyethylene variants. All polyethylene forms are chemically similar. They have long chains of CH2 which have been created by high temperature and high pressure, catalyzing breakdown byproducts of diazomethane in a reaction chamber.
HDPE is characterized by particularly low levels of side-branching groups on the main polymer chains, and no long side branches at all. This structure allows the chains to lie close together in very orderly, pseudo-crystalline arrangements that allow higher-density materials. The degree of side branching is a result of variations in process conditions and catalysts. It is now a highly controllable property, so a range of end-result materials of stipulated molecular weights can be manufactured; indeed their properties are dependent on this variance. HDPE’s relatively high density and crystallinity make it stronger, less elastic, and more resistant to load distortion. Typical HDPE densities are between 0.933 and 1.27 g/cm3, with a resultant range in properties. For more information, see our guide on What is High-Density Polyethylene (HDPE).
What Is ABS?
ABS (Acrylonitrile Butadiene Styrene) is a terpolymer (i.e., a triple-material polymerization) resulting from the copolymerization of styrene and acrylonitrile rubber, in association with butadiene rubber. The acrylonitrile component is generally between 15% and 35%, the butadiene between 5% and 30%, and the remainder is styrene. The result is long chains of polybutadiene, crossed with short chains of polystyrene-co-acrylonitrile. The nitrile groups are highly polarized, which creates a strong attraction between chains, considerably increasing the tensile capacity over basic polystyrene. The acrylonitrile adds significant fatigue resistance, chemical resistance, and rigidity, and also increases the maximum service temperature. The styrene brings a smooth, resilient surface, hardness, rigidity, and good melt-flow properties, making the material easy to process. The butadiene rubber improves toughness and ductility at low temperatures. For more information, see our guide on ABS (Acrylonitrile Butadiene Styrene).
ABS was first commercialized by Borg-Warner® in 1954. As the patenting expired, a large number of chemical companies developed their versions of the material, such that it is now manufactured by hundreds of competing companies. It is now a commodity material, and most grades of available ABS diverge very little from the standard form and properties. Figure 1 below is an example of Lego® made with ABS:
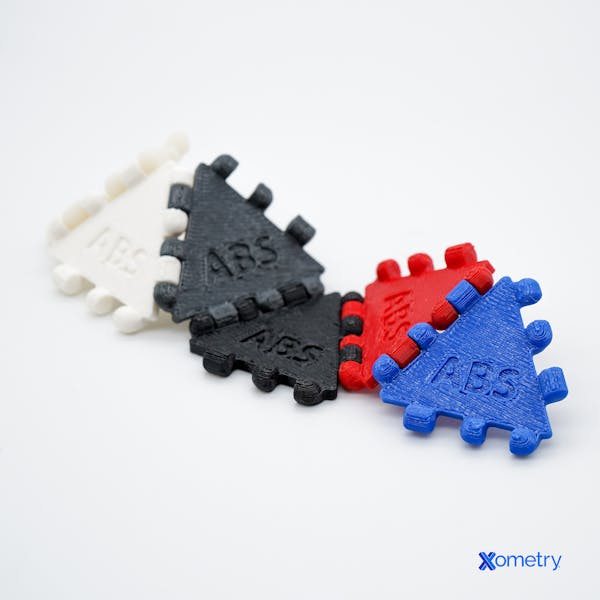
HDPE vs. ABS: Applications and Uses
Some HDPE applications include:
- Fuel tanks, wiring & cables, cable ties and retainers, body-mounted clips.
- Trash bins, garden equipment, furniture, storage bins, children's toys, and playground equipment.
- Crates, trays, milk bottles, caps for PET bottles, fuel cans, drums, and industrial fluid containers.
- Ropes, fishing and sports nets, as well as industrial and decorative fabrics.
- Product packaging.
ABS is a widely used structural/cosmetic material, with applications in most markets. Unusually, it falls between the “standard” polymers (HDPE, PVC, PS, etc.) and the engineering polymers (POM, nylon, PBT, PEEK, etc.) in properties, so it can serve in both moderate-stress engineering roles and consumer-level/cosmetic roles such as:
- Bumpers, exterior small panels, interior panels, and control parts for automotive.
- Consumer goods: all non-specialist parts in audio, kitchen, household, PC enclosures, laundry, refrigeration, lighting, furniture, and baby gear.
- Exterior and interior finishing parts, ducting, electrical gear, and piping for architecture.
- Medical-device enclosures, handles/grips, and cosmetic/hygiene covers.
- Tool components such as housings, handles, and low-stress functional parts.
HDPE vs. ABS: Physical Properties
Table 1 below lists the physical properties of HDPE and ABS:
Property | ABS value (metric) | HDPE value (metric) |
---|---|---|
Property Density | ABS value (metric) 1.0–1.2 g/cm3 | HDPE value (metric) 0.933–1.27 g/cm3 |
Property Hardness, Shore D | ABS value (metric) 55–100 | HDPE value (metric) 55–69 |
Property Tensile strength, ultimate | ABS value (metric) 22.1–74 MPa | HDPE value (metric) 15.2–45 MPa |
Property Tensile strength, yield | ABS value (metric) 13.6–65 MPa | HDPE value (metric) 2.69–200 MPa |
Property Elongation at break | ABS value (metric) 3–150% | HDPE value (metric) 3–1,900% |
Property Modulus of elasticity | ABS value (metric) 1–2.65 GPa | HDPE value (metric) 0.483–1.45 GPa |
Property Flexural yield strength | ABS value (metric) 0.379–593 MPa | HDPE value (metric) 16.5–91 MPa |
Property Flexural modulus | ABS value (metric) 0.2–5.5 GPa | HDPE value (metric) 0.5–4.83 GPa |
Property Dielectric constant | ABS value (metric) 2.6–3.3 | HDPE value (metric) 2.0–2.6 |
Property Melting point | ABS value (metric) 200 °C | HDPE value (metric) 120–130 °C |
Property Max service temperature | ABS value (metric) 80–100 °C | HDPE value (metric) 80–120 °C |
HDPE vs. ABS: Recyclability and Sustainability
Overall, HDPE materials are highly recyclable and can produce good resultant products for 10 or more cycles (potentially many more, if perfectly sorted and treated gently). However, real recycling rates worldwide are minimal as a percentage of the total made. Most are lost to the environment, put in landfills, or burned for disposal or power generation. HDPE film materials are generally used in heavier (thicker) sections and are colored. They are relatively easy to sort for high purity. The process does not require the thorough separation of colors at the sorting stage unless a color-controlled recycled material is required. For most recycled applications, a general brown color is accepted.
ABS is a widely recycled material that can tolerate the process through many cycles, due to its chemical resilience. Despite being labeled as “other” ♹, ABS is relatively easy to identify in the recycling stream and can be well sorted. Many recycled ABS components come from architectural, automotive, and consumer goods and the components are often relatively large and easy to pick. Sorted plastic is washed, dried, and then shredded into fine shards for easier processing. This material is then heated to the melt/flow point and extruded as pellet feedstock. The result is high-quality second-grade material that generally has a dark color and can be used for a range of otherwise normal applications. The feedstock pellets are used to substitute for virgin material, or more often serve as a second-grade minority component with otherwise new material.
HDPE vs. ABS: Cost
HDPE is a low-price commodity material manufactured in huge quantities. The price for virgin material is around $0.80–1.20 per kg, falling to $0.20 for recycled material. ABS is also a low price material. Commodity granules in white or basic color cost between $0.80 and $1.20 per kg. Custom masterbatch granules with specialist additives or unique colors cost around $4.00 per kg and upwards, depending on the nature of the additives. Recycled, high-quality basic granules are generally 10–20% lower in price than virgin material, reflecting the commodity nature of the market and the high recyclability.
Alternative Materials to HDPE and ABS
HDPE variants have a wide range of applications, but they are narrow in scope, and alternatives are straightforward. For most applications, HDPE alternatives are LDPE, PEX, ABS, PP, and rubber-modified PP.
ABS substitutes are the subject of wide-ranging research. Their generalized use in consumer and automotive applications makes them a headline case for bio-sourced and biodegradable alternatives across most sectors. Some examples are listed below:
- A Siemens research group has developed an as-yet-unnamed form of PHB (polyhydroxybutyrate) made from starch, palm oil, and CO2 .
- The US Department of Energy’s Oak Ridge National Laboratory is working on an ABS substitute that replaces the styrene component with wood-derived lignin. This is claimed to be stronger than ABS and moderately recyclable (3 cycles, with limited degradation).
- Eastman Chemical recently announced another lignin-based ABS equivalent.
- LEGO, perhaps the single largest user of ABS, is pouring money into bioplastic alternatives to ABS.
- As ABS substitutes from hydrocarbon and non-biodegradable sources, good options (depending on the details of the application) are PET (polyethylene terephthalate), PBT (polybutylene terephthalate), SPS (syndiotactic polystyrene), and AES (acrylonitrile ethylene styrene).
- For short-life applications, PLA (polylactic acid) can be used as a substitute for ABS.
Summary
This article presented HDPE and ABS, explained each of them, and discussed their differences and use cases. To learn more about HDPE and ABS, contact a Xometry representative.
Xometry provides a wide range of manufacturing capabilities and other value-added services for all of your prototyping and production needs. Visit our website to learn more or to request a free, no-obligation quote.
Copyright and Trademark Notice
- Borg-Warner® is a registered trademark of the Borg-Warner Corporation
- Lego® is a trademark of the LEGO Group.
Disclaimer
The content appearing on this webpage is for informational purposes only. Xometry makes no representation or warranty of any kind, be it expressed or implied, as to the accuracy, completeness, or validity of the information. Any performance parameters, geometric tolerances, specific design features, quality and types of materials, or processes should not be inferred to represent what will be delivered by third-party suppliers or manufacturers through Xometry’s network. Buyers seeking quotes for parts are responsible for defining the specific requirements for those parts. Please refer to our terms and conditions for more information.
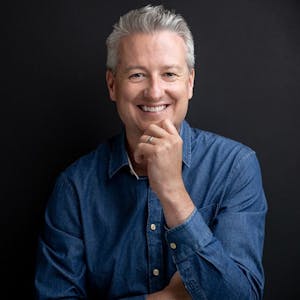