With just a quick look at a polycarbonate product and an acrylic one, it’ll be pretty difficult to tell these two materials apart, but at a deeper chemical level, their differences become a lot clearer. These plastics excel in different areas when it comes to their characteristics, and while both are abundant in automotive, consumer, and building industries, knowing what makes them different will help you manufacture a better product. Learn more about acrylic and polycarbonate in our brief breakdown below.
What is Polycarbonate?
Plastic often has a reputation for being cheap and relatively easy to break, which isn’t fully true for polycarbonate. Although it is indeed a rigid plastic, its strength is capable of standing strong against bullets, holding heavy objects without buckling, and handling drops or falls. Polycarbonate has a pretty high melting point (around 295 °C), and it’s not one to break and crack under stress, unlike other thermoplastics out there. It’s an amorphous material, which means it’s not very crystalline and its chemical compounds don’t have a structured chain — making it easy to mold, shape, and remain intact. To give you an idea of what it looks like, you can see a Xometry “X” below that was 3D printed in polycarbonate.
Polycarbonate is a common replacement for materials, like silicate glass, because it tends to be stronger and cheaper. Because of its ability to stay clear without deforming, it’s a great optical choice. It’s also popular for a variety of different manufacturing processes, whether you’re interested in injection molding or cutting sheets.
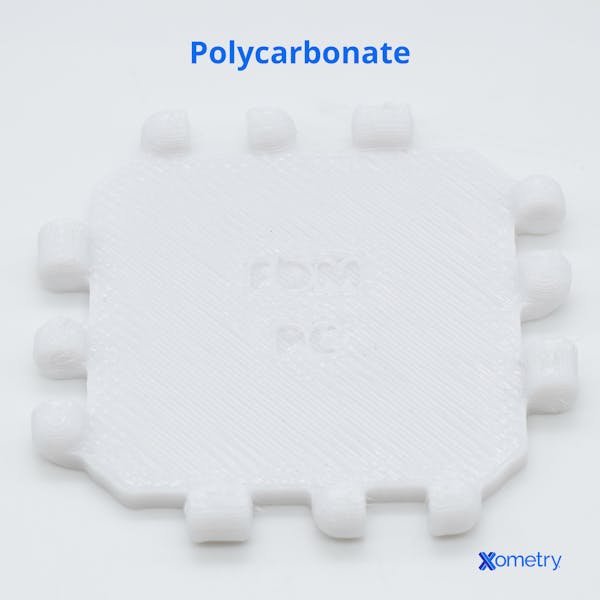
Applications
If you look around, you’d be surprised at the number of products that are made of or have some portion made of polycarbonate, including:
- Bulletproof barriers and windows
- Safety barriers for scientific or industrial workspaces
- Bus and train driver enclosures
- Safety goggles and glasses
- Eyepieces for telescopes and microscopes
- Mobile phone cases
- Molds and trays
What is Acrylic?
Officially titled polymethyl methacrylate, this is another popular plastic used in manufacturing—though its shortened name acrylic is much easier to remember and likely more familiar. Like polycarbonate, it’s a chameleon when it comes to the mediums it’s available in, and you can find it in a fiber, solid, glue, or paint format. To give you an idea of how it looks in a solid form, you can see a laser-cut acrylic sheet in the image below.
Although polycarbonate has a great level of transparency, acrylic is even more so. It’s also remarkably strong and resistant to impact like polycarbonate — although it only has 17 times the resistance of glass, compared to polycarbonate’s 250-times resistance.
Acrylic is slightly cheaper, and it, too, has plenty of manufacturing uses, whether it’s processed through molding or CNC machining.
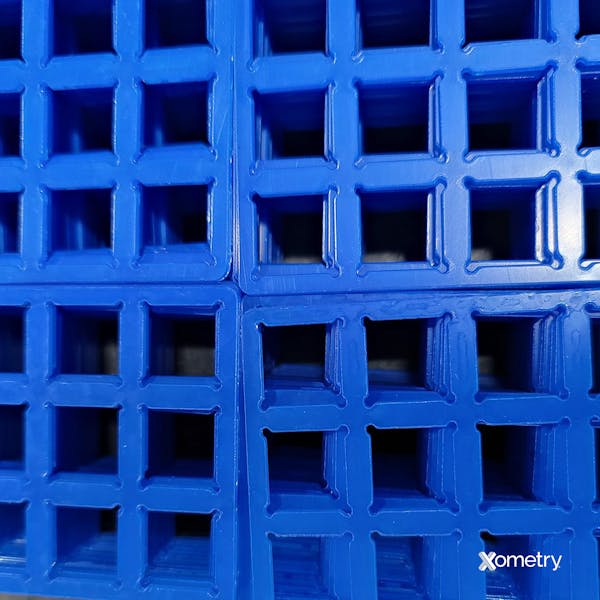
Laser Cut Acrylic at Xometry
Applications
There are many uses for acrylic, but we’ve listed just a few below:
- Windows
- Shelves and storage containers
- Light diffusers
- Toys
- Decor, furniture, and lampshades
- Signage and arts and crafts
- Safety glasses and goggles
Property Comparison
To give you a good idea of how polycarbonate and acrylic compare from a physical and mechanical standpoint, we’ve parsed it out in this table:
Property | Polycarbonate | Acrylic |
---|---|---|
Property Tensile Strength (Ultimate) | Polycarbonate 28–74 MPa | Acrylic 65–83 MPa |
Property Heat Deflection Temperature | Polycarbonate 127–147 ℃ | Acrylic 110–115 ℃ |
Property Water Absorption | Polycarbonate 0.03–0.30 | Acrylic 0.13–0.80 |
Property Hardness (Rockwell M) | Polycarbonate 70–75 | Acrylic 94–105 |
Property UV Resistance | Polycarbonate Fair — polycarbonate tends to degrade faster unless it’s coated, usually around 10% | Acrylic Very good — acrylic will only see around 3% degradation over the period of 10 years |
Property Elongation | Polycarbonate 10–138% | Acrylic 3.0–6.4% |
Property Transparency | Polycarbonate 47–92% | Acrylic 50–93% |
Property Chemical resistance | Polycarbonate Polycarbonate has good resistance against acids, salts, and organic grease or oils, but it’ll degrade when it’s exposed to methyl alcohol, acetone, hydrocarbons, and alkaline solutions. | Acrylic Acrylic has low resistance to salt, acids, alkalines, ethanol, and other undiluted alcohols. |
Polycarbonate vs. Acrylic Properties
Comparing Costs, Recyclability, and Other Factors
As far as strong materials go, these two plastics are inexpensive, but when up against one another, you’ll notice that acrylic tends to be cheaper than polycarbonate, which speaks to polycarbonate’s higher strength and melting point. Prices will vary depending on your location or the type of plastic you’re buying, but as a guide, you can expect to pay around $2.50 to $3.50 per kilogram of a polycarbonate sheet and around $1.50 to $2.00 per kilogram of an acrylic sheet.
Both are recyclable, but oftentimes acrylic isn’t accepted by every recycling program, so you have to find a center that has the means to break it down properly. A good chunk of recyclable plastic ends up in landfills, so it’s important that manufacturers and businesses keep a watchful eye on where waste goes. Energy-wise, both acrylic and polycarbonate are easier to produce than glass and require fewer resources.
Another important thing to note has to do with people’s health and the fact that polycarbonate was created over the last few decades. A good portion of it contains bisphenol A (BPA), which has been found to be harmful and continues to see bans in countries around the world. Keep this in mind when it comes to choosing the type of plastic you’re working with, especially if it’s destined to end up in a home or consumer environment.
Alternatives
Both of these materials are plastics, but they tend to be more expensive than similar options out there. If you’re looking to cut costs, the following alternatives might be worth exploring:
- Polyethylene terephthalate (PET): You’ll find this type of plastic is popular for water bottles, food containers, body care containers, and more. It just so happens to be a great alternative for acrylic and polycarbonate, especially if transparency isn’t a huge priority.
- Polyvinyl chloride (PVC): When it comes to windows, coverings, and outdoor uses, PVC is a great alternative to the former plastics.
How Xometry Can Help
We have polycarbonate 3D printing services here at Xometry, but there are many more services outside of that that might be applicable to you and your business. We also offer custom acrylic CNC machining, acrylic laser cutting, polycarbonate laser engraving, polycarbonate laser cutting, and more. You can get a free quote today for any of these services through our website.
Disclaimer
The content appearing on this webpage is for informational purposes only. Xometry makes no representation or warranty of any kind, be it expressed or implied, as to the accuracy, completeness, or validity of the information. Any performance parameters, geometric tolerances, specific design features, quality and types of materials, or processes should not be inferred to represent what will be delivered by third-party suppliers or manufacturers through Xometry’s network. Buyers seeking quotes for parts are responsible for defining the specific requirements for those parts. Please refer to our terms and conditions for more information.
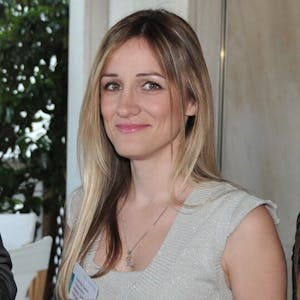