Custom Online CNC Machining Services
Instant quotes on custom metal and plastic machined parts | Quick turn prototypes and production parts in days | Free standard shipping on all US orders | International prototype pricing includes tariffs | ISO 9001:2015, ISO 13485, IATF 16949:2016, AS9100D certified. ITAR registered.
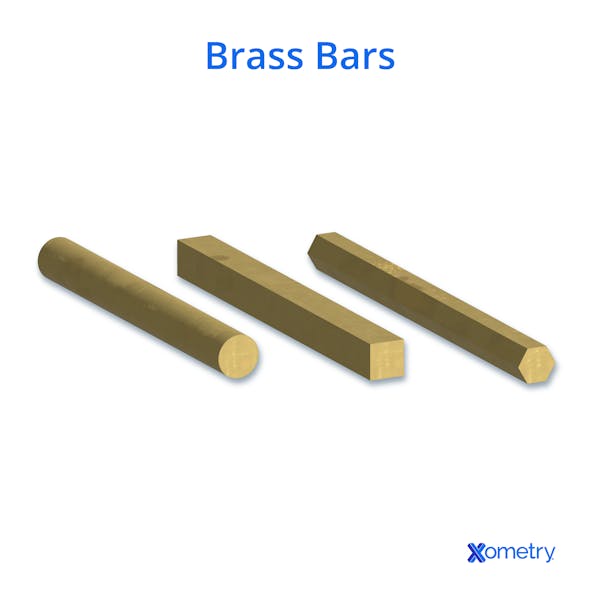
Why Use Xometry for Custom Online CNC Machining Services?
Xometry provides a custom online CNC machining service to engineers, product developers, designers, and more through our vetted network of 10,000+ suppliers. Our highly qualified and certified machine shops can make any custom design, simple or complex. We offer rapid machining, small-batch machining, and high-volume production, with all orders serviced by Xometry from end to end. Upload a CAD file to the Xometry Instant Quoting Engine® to get a price, lead time, and design-for-manufacturability feedback on your custom CNC parts. Our fast CNC machining capabilities include services for metals and plastics and flexible production and shipping options to meet you at the perfect price and product development stage. Your price for CNC-machined prototypes includes tariffs and shipping for standard parcels.
Xometry assures the quality of your machined parts with our ISO 9001:2015, ISO 13485, IATF 16949:2016, and AS9100D certified quality management system, ITAR registration, and options to add inspections, hardware traceability, material certifications, and CoCs. We accept technical drawings and have support teams to ensure you get quality CNC-machined parts on time.
What is CNC Machining?
CNC, or computer numerical control machining, is a widely used manufacturing process that uses automated, high-speed cutting tools to form designs from metal or plastic stock. Standard CNC machines include 3-axis, 4-axis, and 5-axis milling machines, lathes, and routers. Machines may vary in how CNC machined parts are cut—the workpiece may remain in place while the tool moves, the tool may remain in place while the workpiece is rotated and moved, or both the cutting tool and workpiece may move together.
Skilled machinists operate a CNC machine by programming tool paths based on the geometry of the final machined parts. The part geometry information is provided by a CAD (computer-aided design) model. CNC machines can cut almost any metal alloy and rigid plastic with high precision and repeatability, making custom CNC machined parts suitable for nearly every industry, including aerospace, medical, robotics, electronics, and industrial. Xometry provides CNC services and offers custom CNC quotes on over 40 materials ranging from commodity aluminum and acetal to advanced titanium and engineered plastics like PEEK and Teflon.
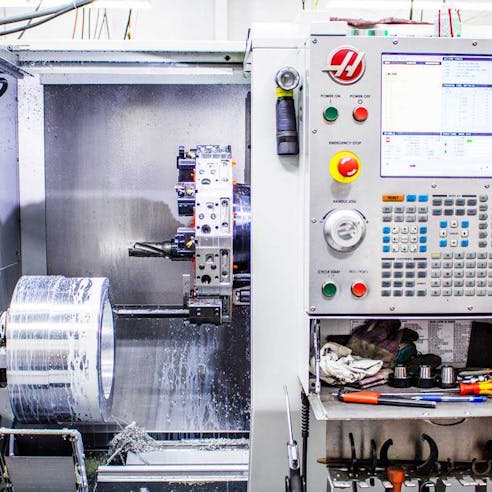
Custom CNC Machining Services: Machining, Turning, Milling, and Routing
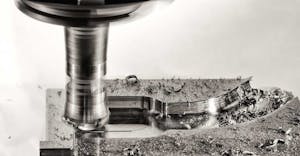
Custom CNC Milling Services
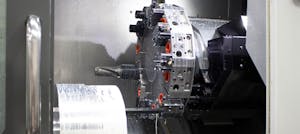
CNC Turning Service
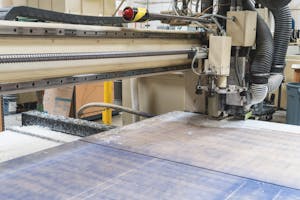
CNC Routing Services by Xometry
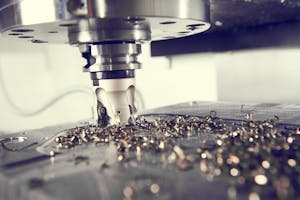
High Volume CNC Machining Services by Xometry
Feature | Description |
---|---|
Feature Maximum Part Size | Description Milled parts up to 80” x 48” x 24” (2,032 x 1,219 x 610 mm). Lathe parts up to 62” (1,575 mm) length and 32” (813 mm) diameter. |
Feature Standard Lead Time | Description 3 business days |
Feature General Tolerances | Description Tolerances on metals will be held to +/- 0.005" (+/- 0.127 mm) in accordance with ISO 2768 unless otherwise specified. Plastics and composites will be +/- 0.010”. |
Feature Precision Tolerances | Description Xometry can manufacture and inspect to tight tolerances, including sub +/- 0.001" tolerances, per your drawing specifications and GD&T callouts. |
Feature Minimum Feature Size | Description 0.020” (0.50 mm). This may vary depending on part geometry and chosen material. |
Feature Threads and Tapped Holes | Description Xometry can accommodate any standard thread size. We can also machine custom threads; these will require a manual quote review. |
Feature Edge Condition | Description Sharp edges are broken and deburred by default |
Feature Surface Finish | Description The standard finish is as-machined: 125 Ra or better. Additional finishing options can be specified when getting a quote. |
We are able to offer a precision machining service with a wide array of tolerances. The table below depicts the general tolerances for CNC machining:
For more information please see this guide to our manufacturing standards.
Metal CNC Machining Materials
CNC Machining Aluminum Alloys
Aluminum 6061
Aluminum 5052
Aluminum 2024
Aluminum 6063
Aluminum 7050
Aluminum 7075
Aluminum MIC-6
Learn more about aluminum for CNC machining.
CNC Machining Copper Alloys
CNC Machining Bronze Alloys
CNC Machining Brass Alloys
CNC Machining Stainless Steel Alloys
Nitronic 60 (218 SS)
Stainless Steel 15-5
Stainless Steel 17-4
Stainless Steel 18-8
Stainless Steel 303
Stainless Steel 316/316L
Stainless Steel 416
Stainless Steel 410
Stainless Steel 420
Stainless Steel 440C
Learn more about stainless steel for CNC machining.
CNC Machining Steel Alloys
Steel 1018
Steel 1215
Steel 4130
Steel 4140
Steel 4140PH
Steel 4340
A2 Tool Steel
O1 Tool Steel
Learn more about steel for CNC machining.
CNC Machining Titanium Alloys
CNC Machining Zinc Alloys
Custom
We can source additional alloys and tempers from within our network of 10,000 custom machine shops. If you do not see the material stock you are looking for, please choose "Custom" under the material drop-down in the Xometry Instant Quoting Engine℠. You can then submit your quote for manual review and our expert manufacturing team will reach out.
Plastic CNC Machining Materials
ABS
High-strength engineering plastic used for many commercial products.
Learn more about ABS for CNC machining.
Acrylic
A clear glass-like plastic. Good wear and tear properties. Great for outdoor use.
Learn more about acrylic for CNC machining.
Delrin (Acetal)
Acetal
Delrin 150
Delrin 100
Resin with good moisture resistance, high wear resistance, and low friction. Learn more about Delrin for CNC machining.
Garolite
Garolite G10 (FR4)
Garolite G10 (non-FR)
Garolite G11 (FR5)
Constructed of an epoxy resin with fiberglass fabric reinforcement, also called epoxy-grade industrial laminate and phenolic, this material offers high strength and low moisture absorption. Learn more about garolite G10 for CNC machining and phenolic machining.
HDPE
High-density polyethylene is a moisture and chemical-resistant plastic with good impact strength. The material is outstanding for outdoor applications as well as watertight containers or seals.
Learn more about HDPE for CNC machining.
Nylon 6/6
Offers increased mechanical strength, rigidity, good stability under heat and/or chemical resistance.
Learn more about Nylon 6/6 for CNC machining.
PC (Polycarbonate)
With almost twice the tensile strength of ABS, polycarbonate has superior mechanical and structural properties. Used widely in automotive, aerospace, and other applications that require durability and stability.
Learn more about PC for CNC machining.
PEEK
PEEK
PEEK (USP Class VI TECAPEEK)
PEEK GF30
Offering excellent tensile strength, PEEK is often used as a lightweight substitute for metal parts in high-temperature, high-stress applications. PEEK resists chemicals, wear, and moisture. Learn more about PEEK for CNC machining.
Polypropylene
Has excellent electrical properties and little or no moisture absorption. It carries light loads for a long period in widely varying temperatures. It can be machined into parts requiring chemical or corrosion resistance.
Learn more about polypropylene for CNC machining.
PTFE (Teflon)
This material surpasses most plastics when it comes to chemical resistance and performance in extreme temperatures. It resists most solvents and is an excellent electrical insulator.
Learn more about PTFE for CNC machining.
UHMW PE
Ultra-high molecular weight polyethylene. A general-purpose material. It offers a unique combination of wear and corrosion resistance, low surface friction, high impact strength, high chemical resistance, and does not absorb moisture.
Learn more about UHMW-PE for CNC machining.
PVC
Polyvinyl chloride (Type 1) is a highly chemical-resistant synthetic plastic, PVC is commonly in environments exposed to liquids or requires electrical insulation.
Learn more about PVC for CNC machining.
ULTEM
ULTEM 2300
ULTEM (Polyetherimide) is a stiff, robust, performance-grade thermoplastic that can operate continuously in high-temperature environments (up to 340°F). It has one of the highest dielectric strengths of commercially available thermoplastics, making it an excellent electric insulator. Since ULTEM is also resistant to chemicals, easily cleaned, and does not absorb moisture, it is often used for medical applications.
Custom CNC
We can source additional CNC plastics from within our network of 10,000 machine shops. If you do not see the material stock you are looking for, please choose "Custom" under the material drop-down in the Xometry Instant Quoting Engine℠. You can then submit your quote for manual review and our expert manufacturing team will reach out.
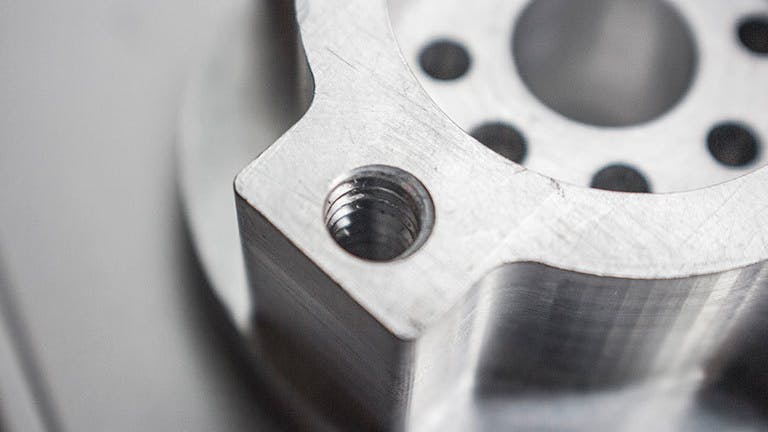
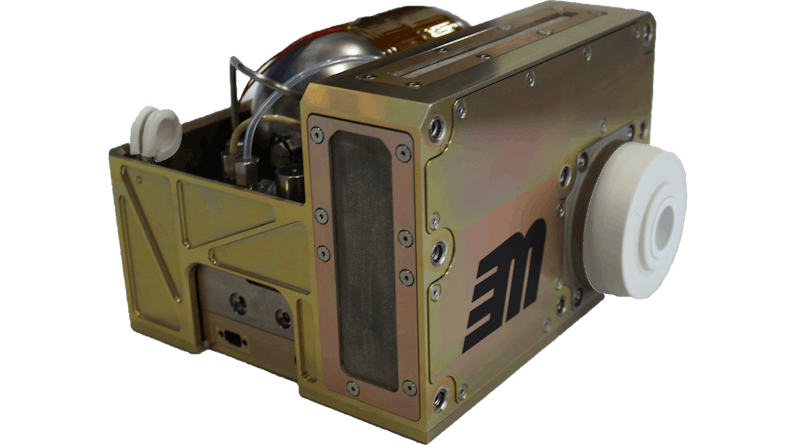

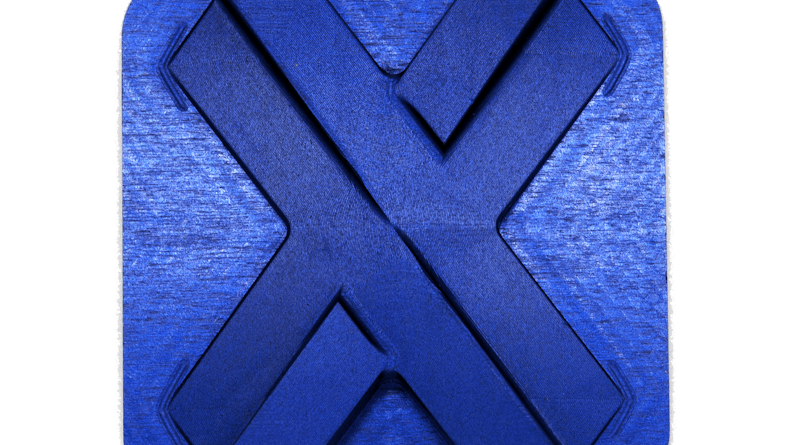
CNC Threads
CNC Machining Finishes
Standard (As-Milled)
The finish option with the quickest turnaround. Machined parts are left with visible tool marks and potentially sharp edges and burrs, which can be removed upon request. CNC machining surface finish is comparable to 125 uin Ra finish.
Bead Blast
The part surface is left with a smooth, matte appearance.
Tumbled
This is a batch-based process that tumbles vibrating media to remove sharp edges and burrs on CNC parts. Tumbling can remove machine marks on exterior surfaces. Parts over 8” may require a manual review.
Anodized (Type II Or Type III)
Type II (MIL-A-8625, Type II) creates a corrosion-resistant finish. Parts can be anodized in different colors—clear, black, red, and gold are most common—and are usually associated with aluminum. Type III (MIL-A-8625/MIL-PRF-8625, Type III, Class 1/2 "hardcoat") is thicker and creates a wear-resistant layer in addition to the corrosion resistance seen with Type II. See examples of our anodized finishes in our metal finishes gallery.
Titanium Anodize
A surface finish for titanium per AMS-2488 Type 2 specification. Also called Tiodize, this finish increases fatigue strength and the wear resistance of a part. Titanium anodized parts are common in aerospace and medical device manufacturing. Non-pigmented titanium anodize finishes will dull shine.
PTFE Impregnated Hard Anodize
A hard coat anodize process that embeds PTFE to create a self-lubricating, dry contact surface with Type 3 hard coat’s protective properties. This finish can be used on aluminum alloys or titanium and increases the service life of the product. This finish conforms to the AMS-2482 Type 1 Hard Coat Anodizing with Teflon (Non-Dyed).
Chem Film (Chromate Conversion Coating)
Provides corrosion resistance and good conductivity properties. Can be used as a base for paint. Can leave surface yellow/gold. Adds very little thickness, about 0.00001”-0.00004”. Chem film will conform to MIL-DTL-5541, TYPE I/II.
Passivation
Improves corrosion resistance for 200 and 300 series and precipitation hardened corrosion-resistant steels. Thickness is negligible, about 0.0000001”. Conforms to ASTM A967, AMS-QQ-P-35, MIL-STD-171, ASTM A380, or AMS 2700.
Powder Coat
This process is where powdered paint is sprayed onto a part and baked in an oven. This creates a strong, wear- and corrosion-resistant, more durable layer than standard painting methods. A wide variety of colors are available to create the desired aesthetic. See examples in our powder coating finishes gallery.
Electropolishing
An electrochemical process cleans steel parts to reduce corrosion and improve appearance, by making the metal brighter. Removes about 0.0001”-0.0025” of the metal. Conforms to ASTM B912-02.
Electroless Nickel Plating
Provides uniform nickel coating which offers protection from corrosion, oxidation, and wear on irregular surfaces. The finished part will be brighter. Thickness starts at .0001”. Conforms to MIL-C-26074.
Silver Plating
Silver offers high solderability and electrical conductivity but is susceptible to tarnish. Conforms to AMS QQ-S-365D. Thickness is about 0.00002” - 0.0003.”
Gold Plating
Gold Plating provides good corrosion and tarnish resistance with excellent solderability. Default application specification is MIL-G-45204 and ASTM B488, CLASS 00, 0, OR 1. Thickness is about 0.00002" - 0.00005."
Zinc Plating
Provides uniform zinc coating which offers protection from corrosion, oxidation, and wear on irregular surfaces. Conforms to ASTM B633-15.
Feature | Description |
---|---|
Feature Internal corner fillets | Description Design internal corner fillets to be 0.020” - 0.050” greater than a standard drill size for the radii. Follow a drill diameter to depth ratio of 1:6 (1:4 recommended) as a guideline for internal corner radii. |
Feature Floor fillets | Description Design floor fillets smaller than corner fillets to allow the same tool to clear material from the interior. |
Feature Undercuts | Description Always design undercuts to standard sizes and away from corners so they are accessible by the cutting tool. |
Feature Tapped/threaded hole depth | Description Provide tool clearance slightly beyond the tapped hole depth to ensure complete threads. |
Feature Complexity | Description Keep the number of small cuts to a minimum to reduce the CNC machining service cost; only design in the necessary features to balance function with aesthetic. |
Get More Tips With Our Complete Design Guide
CNC Machining FAQs
How does CNC machining work?
CNC machining uses subtractive processes, which means feedstock is machined to its final form by subtracting and removing material. Holes are drilled, lots and pathways are bored, and metal stock is shaped into new material with varying tapers, diameters, and shapes.
For subtractive manufacturing, shapes are achieved by the subtraction of material. This contrasts with other types such as additive manufacturing — where materials are added, layered, and deformed to a specified shape. It also contrasts with injection molding where the material is injected in a different state of matter, using a mold, and formed to a specified shape.
CNC machining is versatile — and can be used with various materials, including metals, plastics, wood, glass, foam, and other composite materials. This versatility has helped make CNC machining a popular choice across industries, enabling designers and engineers to fabricate products efficiently and precisely.
How does CNC machining differ from traditional machining?
In traditional machining, a skilled machinist operates a machine, removing or forming metal. This is done according to specifications provided by designers and engineers, usually through an engineering drawing or blueprint. They use turn wheels, dials, switches, chucks, vices, and a variety of cutting tools made of hardened steel, carbide, and industrial diamond, then use measurement instruments to ensure all of the dimensions are correct.
CNC machining performs the same function as traditional machining — metal cutting, drilling, milling, boring, grinding, and other metal forming and removal functions — but CNC machines use computer numerical control rather than manual control by a machinist. It is automated, driven by code, and developed by programmers. It is about as precise the first time of cutting as the 500th. Widely used in digital manufacturing (and sometimes in low-volume production runs), it can be revised and altered for modifications and different materials.
This type of machining is much more precise and has superseded traditional machining (though not entirely) in manufacturing, fabrication, and industrial production. It uses mathematical coordinates and computing power to achieve the same end with the greatest accuracy. Specifically, computer numerical control uses Cartesian coordinates. These are spatial coordinates — in several dimensions — using coordinates and axes. The automation of cutting tool machines controls its cutting, boring, drilling, or other operation using the numerical control of a computer that reads the coordinates. These coordinates were designated by engineers in the product’s digital drawing and design.
What industries use CNC machining?
CNC machining is widely used across industries. It is common in aerospace, automotive, consumer electronics, robotics, agriculture, and other fields that frequently use metal parts. It is also widely used in medical devices, household goods, energy, oil and gas, and other consumer applications. It is one of the most common manufacturing processes in the world.
What is the history of CNC machining?
During World War II, the United States was quickly churning out ships, aircraft, and vehicles for the military. And even once the war ended, production kept up as the country experienced a post-war boom in home construction, infrastructure expansion, and transportation. Naturally, engineers and designers needed tools to help them efficiently meet the growing demand for industrial products.
Enter CNC machining. John T. Parsons, who worked in the production of helicopter rotor blades, was one of the first people to champion CNC machining. He and his colleagues at Wright-Patterson Air Force Base in Dayton, Ohio used interpolation curves, which could be applied to machining with computational methods, to achieve the complex tapers required for rotor blades. As Parsons’ company got called upon to make more and more complex aircraft parts, they turned to computational methods and cnc machined parts to achieve their desired shapes.
This was partly the genesis of CNC machining. Building off of Parsons’ innovations, MIT’s Servomechanisms Laboratory later developed a working machine able to use computational methods to fabricate precise machine parts. Their servo-mechanisms were able to use the Cartesian coordinates — the numerical control — to steer the machine and its moving parts, to fabricate with automated precision. Such automation only grew more sophisticated through the rest of the twentieth century and continues to develop today.
What are your inspection options for CNC machining?
We offer (6) different inspection options on the Modify Parts window under the Inspection tab in the quoting platform. All machined and sheet metal parts will receive a standard inspection included in the part price and lead time. See more on our inspection services.
What are your tolerances for CNC machined parts?
- +.005”/-.005” local tolerances across most geometries in metals, +/- 0.010" for plastics. Will vary for large parts, specifically when holding flatness over large parts after heat treatment.
- Finish requirements for “As Milled” finish will have a minimum 125 surface finish for CNC parts.
- All fabricated parts have a 0.010” dimensional and 1° angular tolerance.
- Tapped holes not explicitly called out as Features on the quoted CAD model may be machined to the diameters specified in that model.
- No surface treatments (e.g. anodize, bead blast, iridite, powder coat, etc.) will be applied unless you have paid for them and we have specifically acknowledged them.
What are your CNC machining & turning capabilities?
Xometry has significant CNC capabilities in machining through our shop services and the Manufacturing Partner Network. In general, here are some guidelines for machine size but if you do have a quote that pushes to RFQ please make sure to request a quote review so we can take a look!
‣ 5 Axis Machining up to 26″
‣ 4 Axis Machining up to 36″
‣ 3 Axis Machining up to 60″
‣ Dual Spindle Lathes with 32″ Swing, 18″ Max Diameter, and 8″ Chuck
‣ Wire EDM with a part depth of 18″
Do you offer Quick-Turn CNC Machining?
Yes! Xometry offers fast lead times on quick-turn parts, with many parts available in 3-4 days. We offer an expedite option, and our team works closely with you to meet your most urgent deadlines.
Will I need to pay tariffs on internationally produced parts?
Xometry's checkout price for internationally produced prototypes shipped to the U.S. includes tariffs and shipping for standard parcels. You can learn more by reading our article on understanding international shipping costs.
Advantages and Challenges of CNC Machining
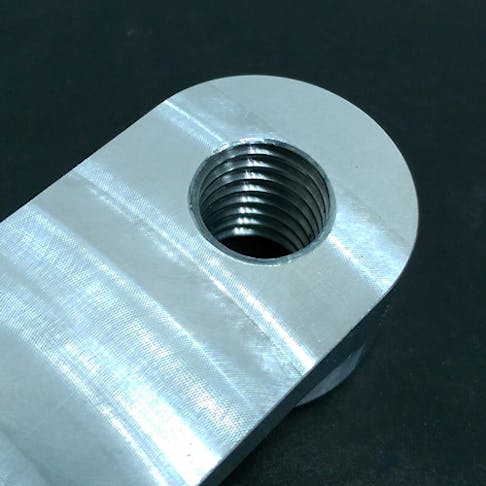
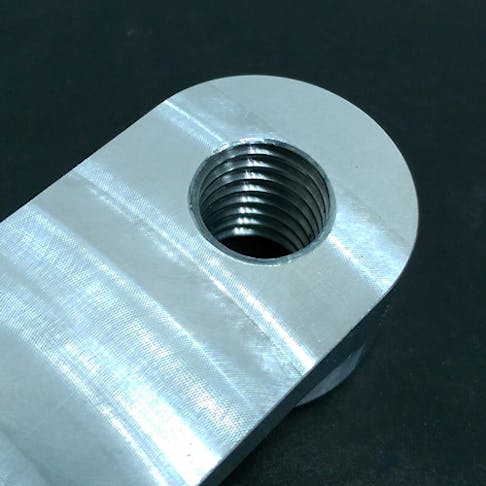
CNC milling and turning are highly accurate and repeatable processes. Tight tolerances between +/-0.001″ – 0.005″ can be achieved, depending on specifications. Machines can be programmed to reliably run for 24 hours, 7 days a week if necessary, so CNC milling is a good way of getting parts produced on demand.
Using standard tooling, a CNC machining service is particularly valuable for creating one-off parts, custom CNC parts, i.e., for replacing legacy components or delivering a specialized upgrade to a customer. It is also conceivable to scale single-part production to runs exceeding 10,000 units. Depending on the unit number, size, and complexity, the turnaround for CNC machined parts can be as short as one day. With shipping and delivery, deadlines can be met within a week.
Another primary advantage of CNC technology is its achievable mechanical properties. By cutting away from bulk material, rather than thermally transforming it as in injection-molding or additive manufacturing, all desirable mechanical properties of the metal or plastic of choice are retained. More than 50 industrial-grade metals, alloys, and plastics can be machined using CNC milling and turning. This selection includes aluminum, brass, bronze, titanium, stainless steel, PEEK, ABS, and zinc. The only material requirement for CNC machining is that the part has an adequate hardness to be fixtured and cut.
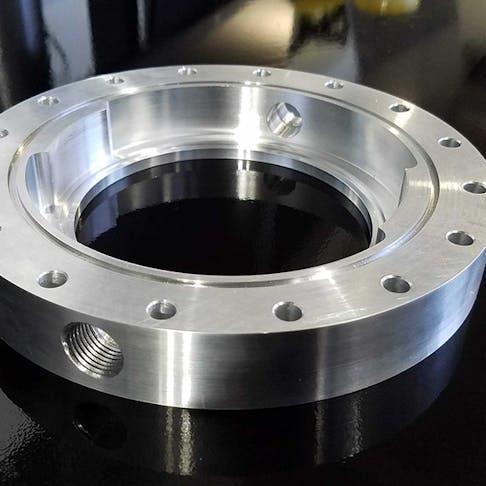
One trade-off when taking advantage of the high performance of CNC manufacturing services is that geometric complexity comes at a cost. Simple, chunky parts are the best designs for CNC milling and turning. There will always be some design limitations due to tool access, although the degree of this effect is relative to the number of axes on the machine. In other words, the more axes used, the more complex the features can be achieved.
Another trade-off is that start-up CNC machining costs can be expensive. It is necessary to have a trained professional perform the setup, tool loading, and programming on CNC mills and lathes. Luckily this cost is fixed, so by taking advantage of the same setup for multiple parts, it becomes more economical. Saving money is also achieved by keeping part repositioning to a minimum. Machining at 5-axis and above can sometimes be more economical on multi-faceted geometries because it eliminates the need to manually reposition the part.
The wire EDM method of machining can be slow and expensive relative to other processes, and the range of materials that can be used is shortened as they must be electrically conductive.
CNC Machining Applications
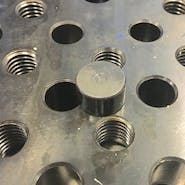
Rapid Tooling
Because CNC machining can cut a high variety of fully dense, durable materials like aluminum 5052 and stainless steel, it is perfect for creating fixtures or molds.
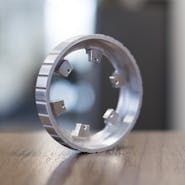
Rapid Prototyping
The range of affordable metal alloys (like aluminum 6061) and plastics (like acetal or ABS) combined with the speed of our skilled machinists makes our online CNC machining service a great option for prototyping.
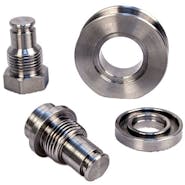
End-Use Production
Performance-enhancing finishes, precision tolerances as low as +/- 0.001”, and certifiable material options make CNC machining an excellent technology for end-use parts.
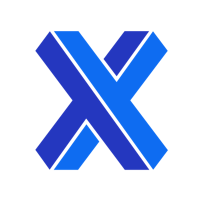
Ready to Get a CNC Machining Online Quote?
Free shipping available for domestic CNC machining orders ; learn more!