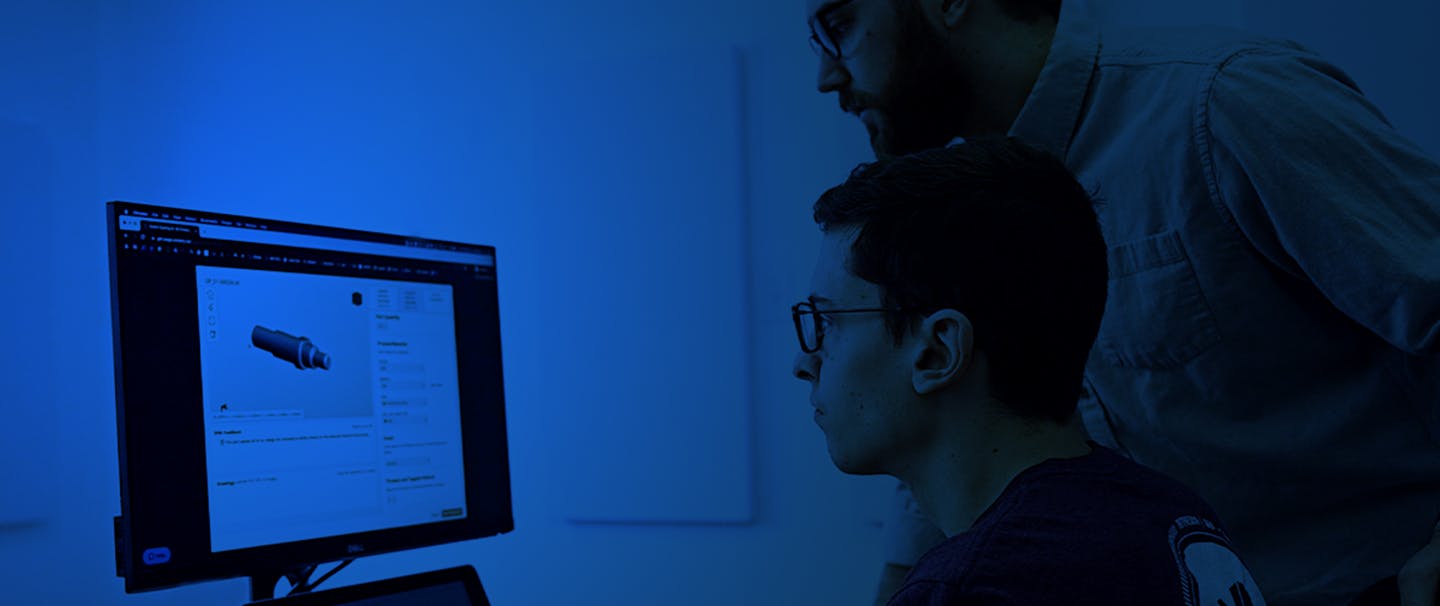
Xometry Resources
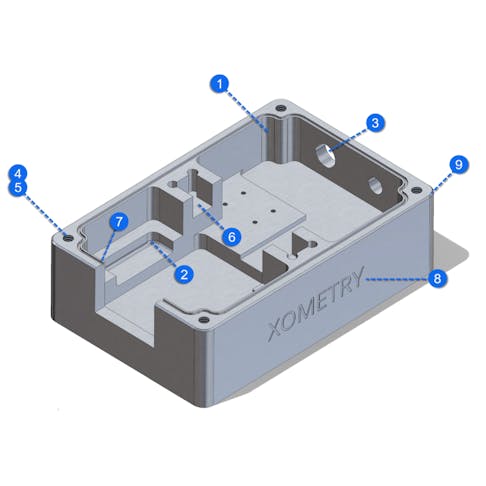
Webinar Recording - Trimming Costs, Keeping Quality: Smart Design Tips for CNC Machining
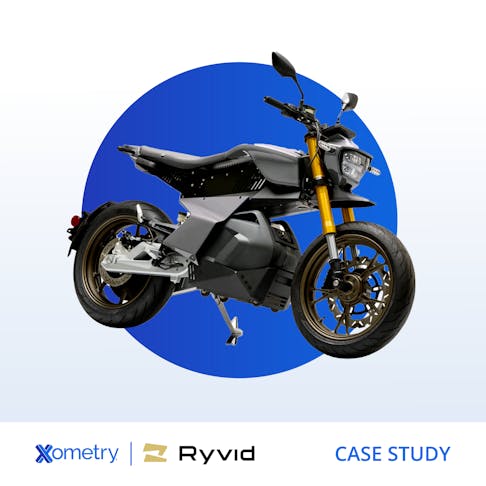
Case Study: Ryvid’s Anthem EV Bike Races Through Production With Xometry's Horizontal Supply Chain
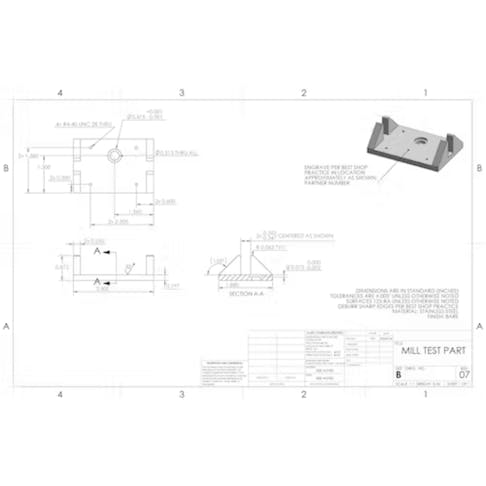
eBook: How to Make a Good Technical Drawing
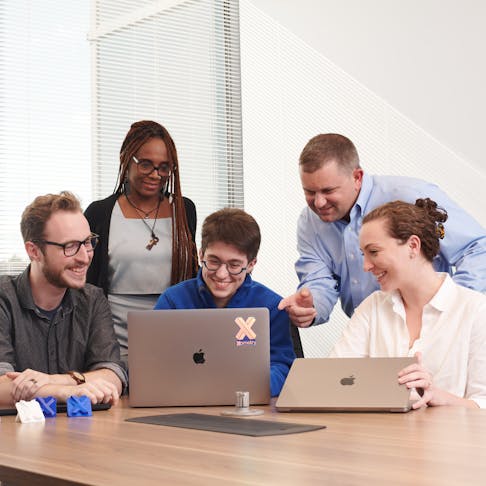
Industry Design
View All Industry Design ContentDesign tips for our top industries like aerospace and defense, automotive, energy, medical and dental, robotics, supply chain, and more.
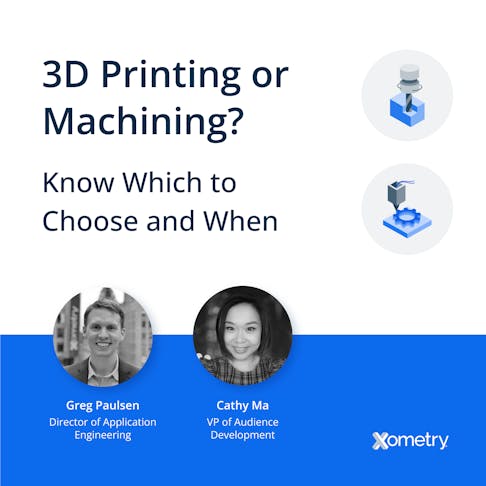
On-Demand Webinar: 3D Printing or Machining? Know Which to Choose and When

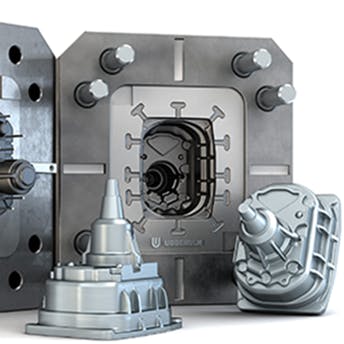
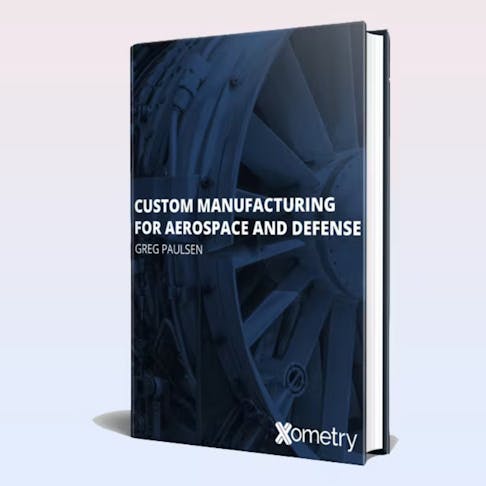
eBook: Custom Manufacturing for Aerospace and Defense
Case Studies
View All Case Studies ContentExamples of Xometry's work with customers across various industries and manufacturing processes.
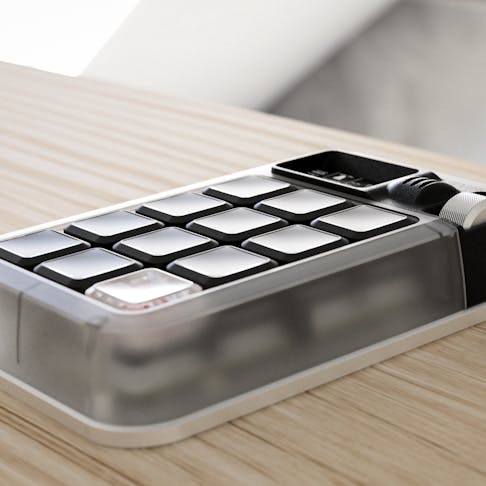
Case Study: Xometry Helps Autodesk Take Its Macro Keypad to the Next Level
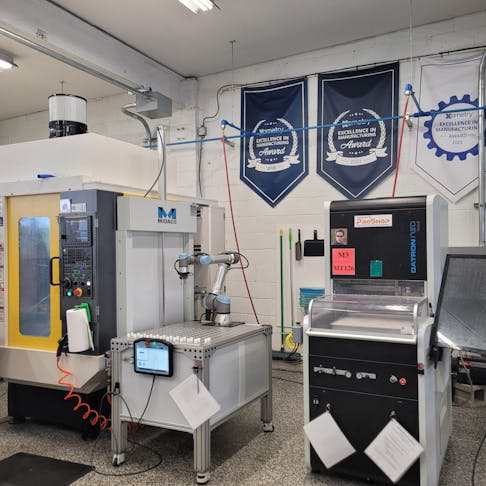
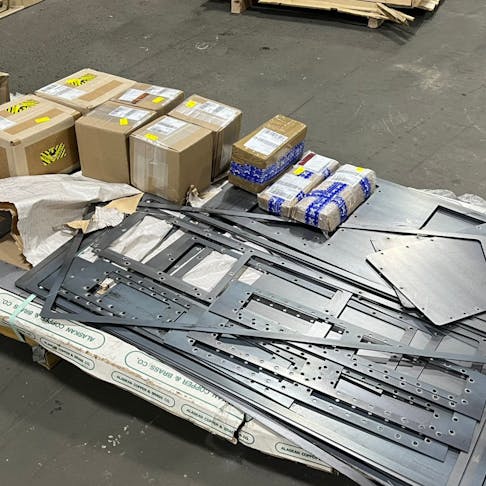
Case Study: Xometry’s Precise Laser Tube Cutting Helps Sea Box Build, Scale Up a Big Project for a Defense Customer
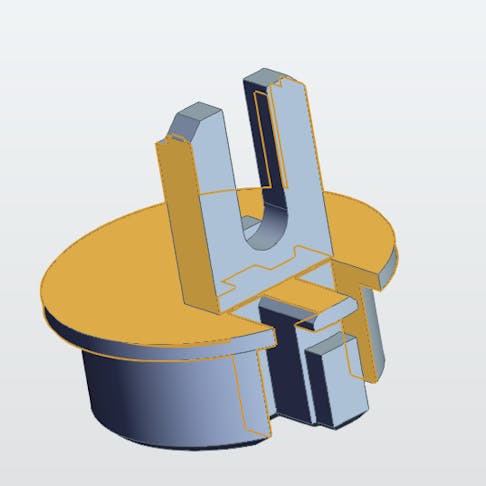
Case Study: KPM Analytics Turns to Xometry’s Instant Quoting Engine for a Quick and Affordable Custom Part
Supplier Shop Tips
View All Supplier Shop Tips ContentTips for machine shops, fabrication shops, 3D printing bureaus, and manufacturers in Xometry's Partner Network.
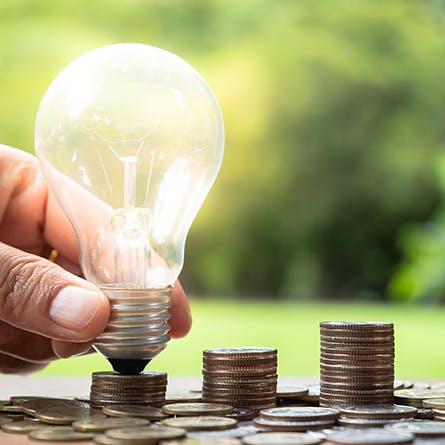
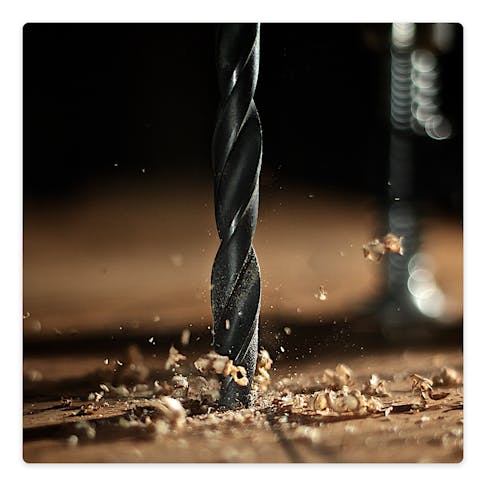
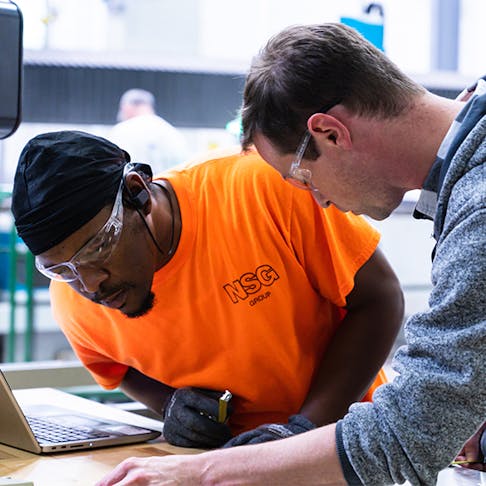
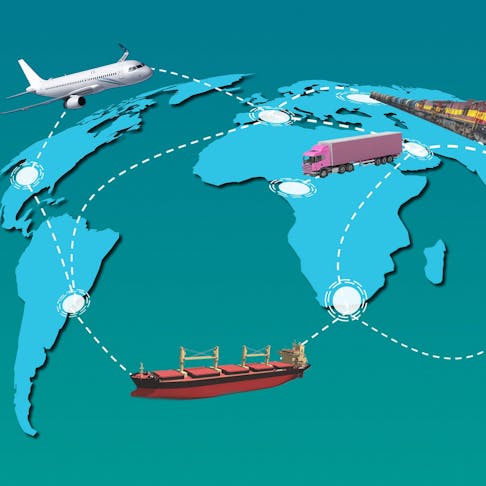
3D Printing Design
View All 3D Printing Design ContentThe latest news, trends, and manufacturing design tips for additive manufacturing.



Machining Design
View All Machining Design ContentThe latest news, trends, and manufacturing design tips for custom machined and fabricated parts.



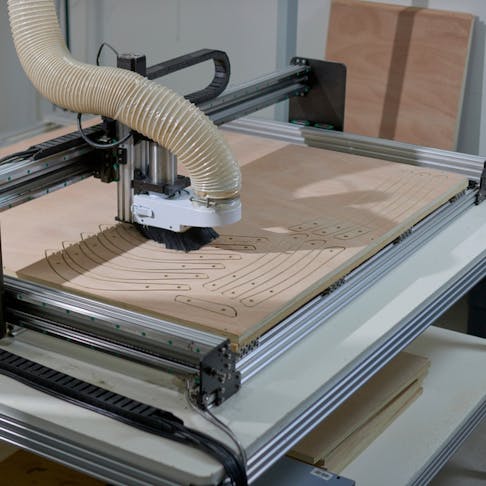
Design Guides
View All Design Guides ContentIn-depth design guides full of best practices for all of Xometry's manufacturing processes.
Blog
View All Blog ContentThe latest Xometry product updates, news, and trends in manufacturing.
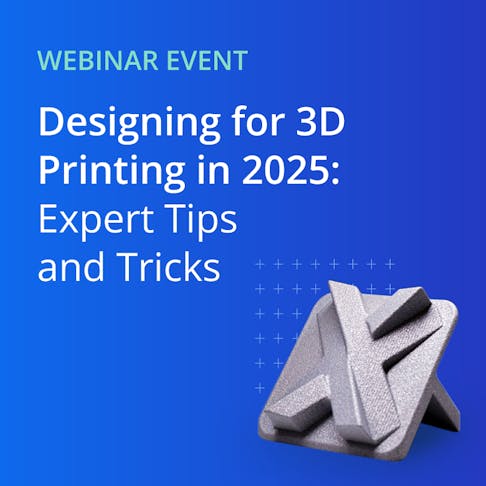
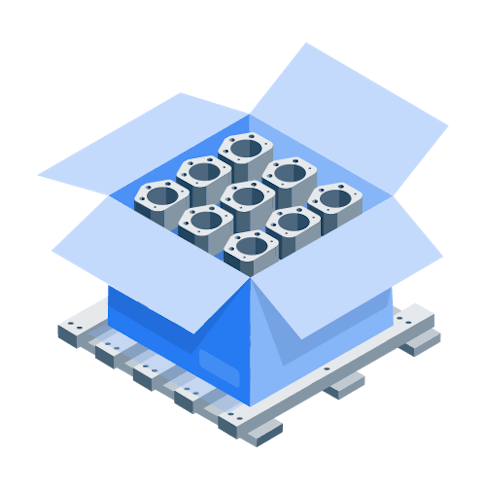
[Webinar Recording] Navigating CMMC Level 2: Compliance & Funding Support for Manufacturers
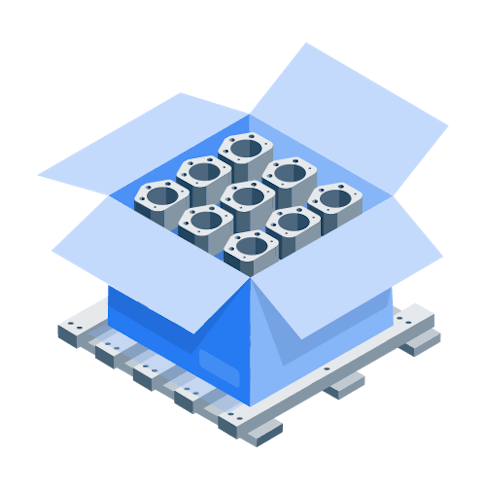
[Webinar Recording] Xometry: Your Medical Molding Partner from Prototype to Production
Materials
View All Materials ContentInformation about common materials used in manufacturing processes.
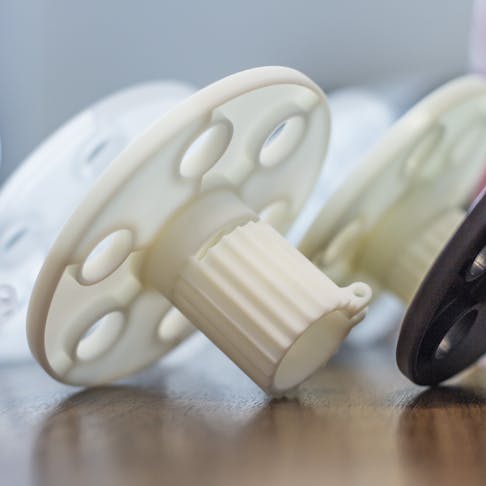
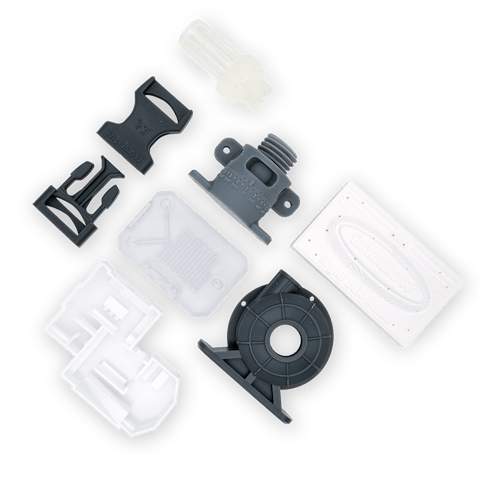
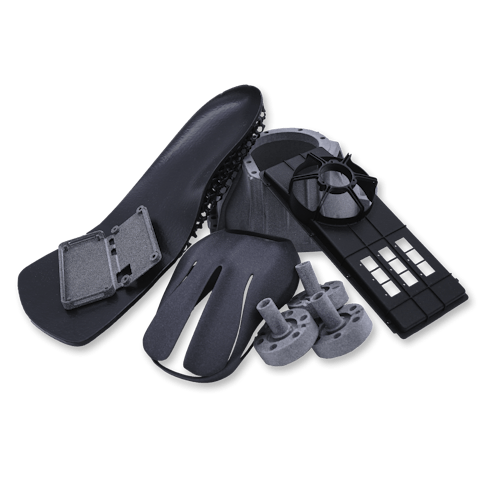
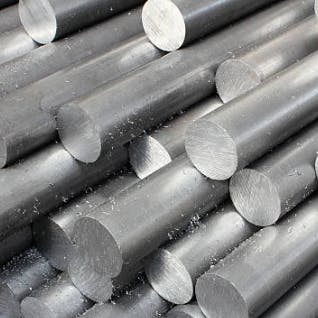
eBooks Library
View All eBooks Library ContentExplore our eBooks, rich with insights and practical information to help you better comprehend the manufacturing industry.
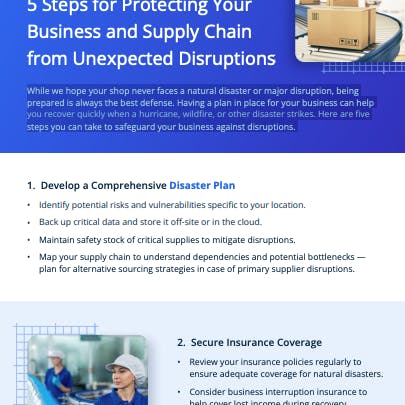
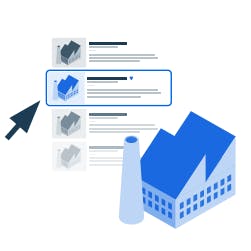
5 Common Manufacturing Challenges for Small Businesses
Casting
View All Casting Content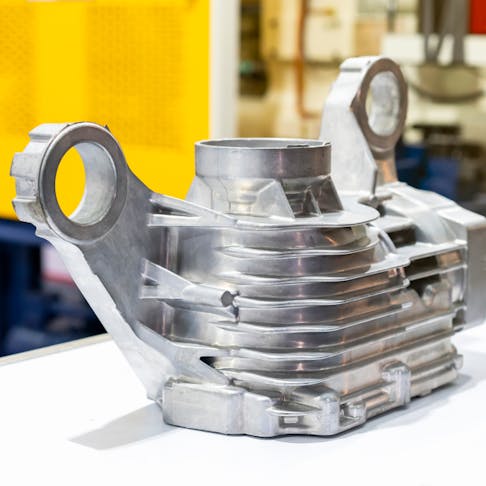
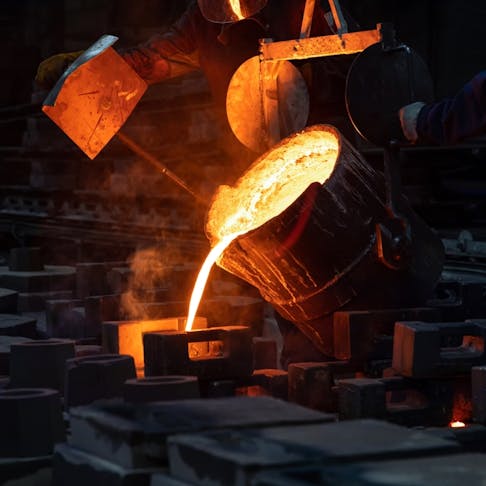
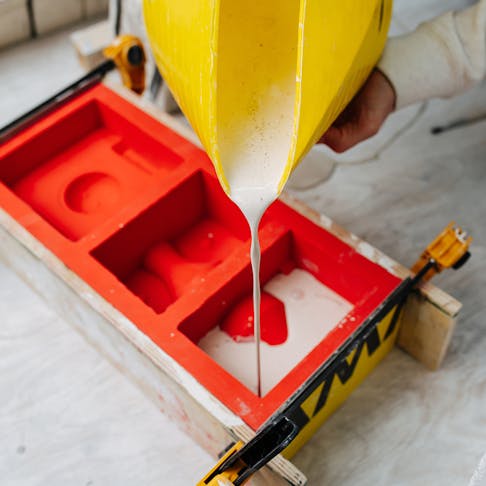
Plaster Casting: What It Is, How It Works, Uses, Process, and Advantages

Tube
View All Tube ContentThe latest news, trends, and manufacturing design tips for laser tube cutting, tube bending, tube rolling, and more.
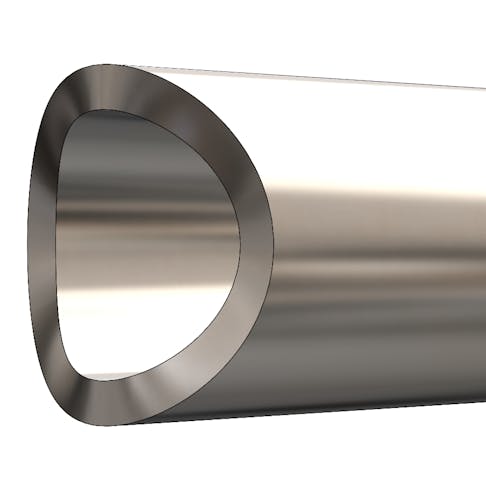
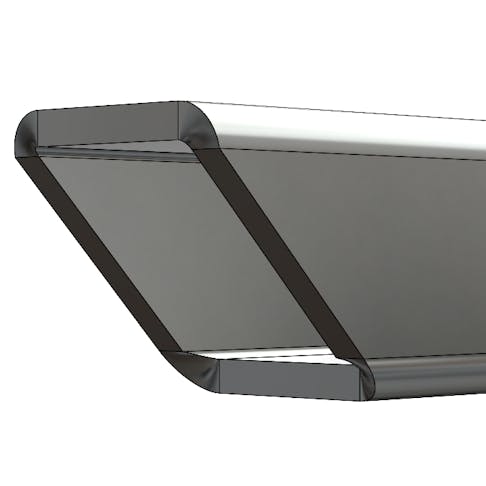
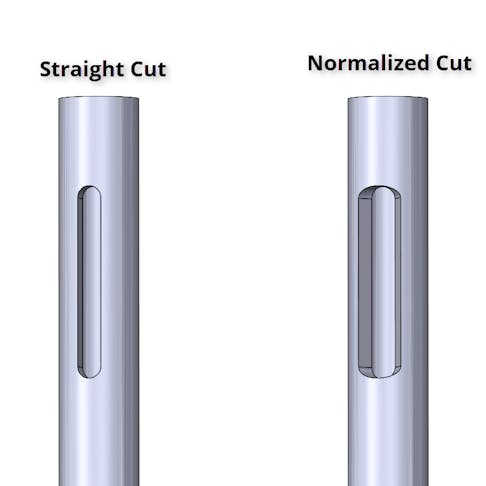
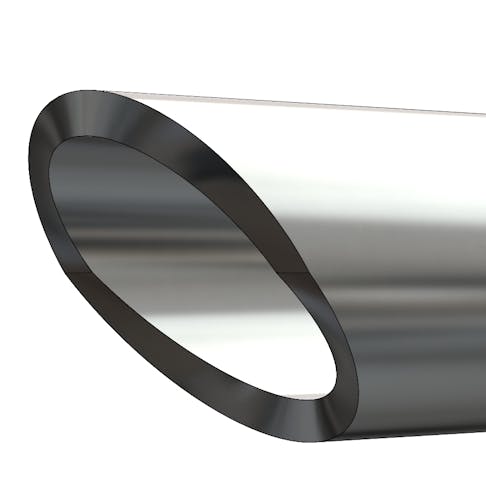
Certifications
View All Certifications Content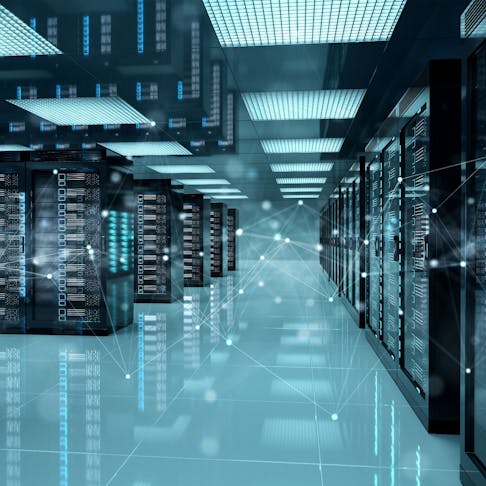
Guide to Cybersecurity Maturity Model Certification (CMMC): Funding Opportunities & Resources
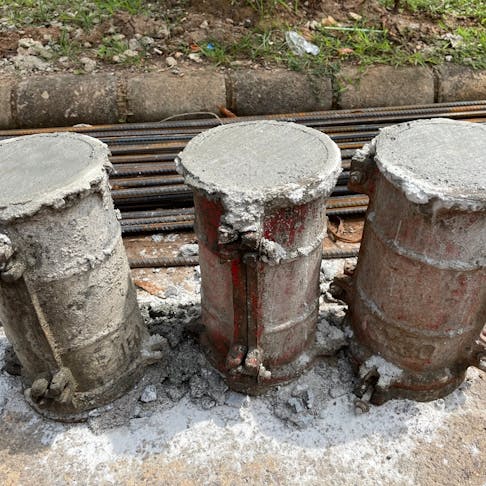
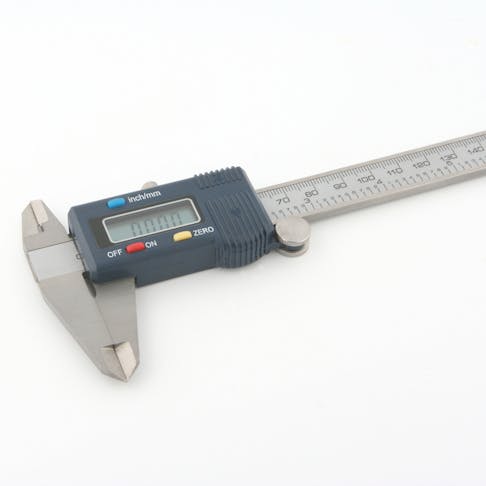
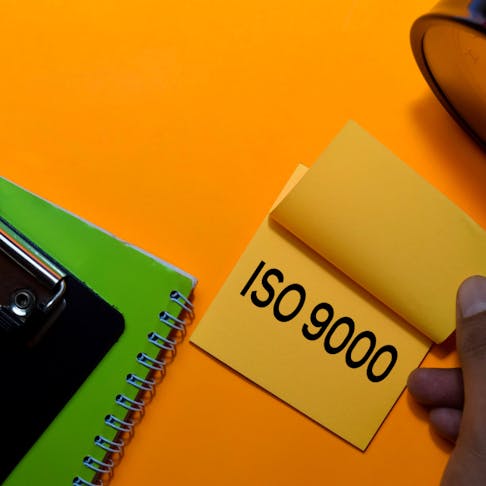
Sheet
View All Sheet ContentThe latest news, trends, and manufacturing design tips for sheet metal, stamping, laser and waterjet sheet cut parts.
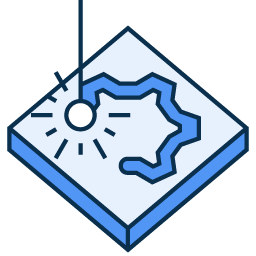
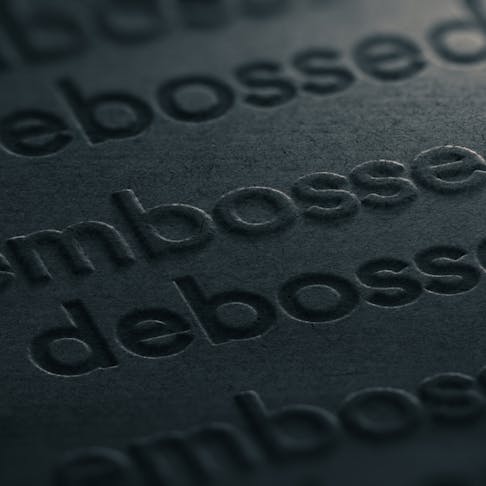
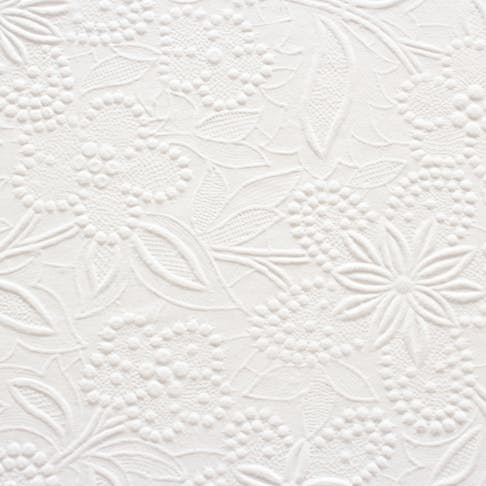
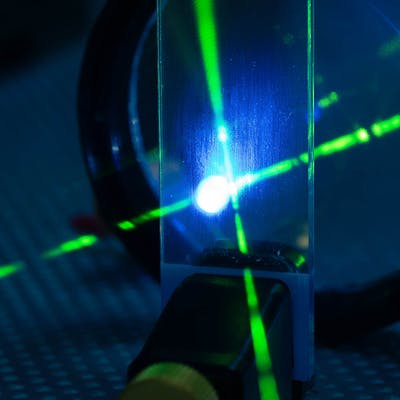
Metal and Plastic Extrusion
View All Metal and Plastic Extrusion ContentThe latest technical guides and articles related to extrusion processes.
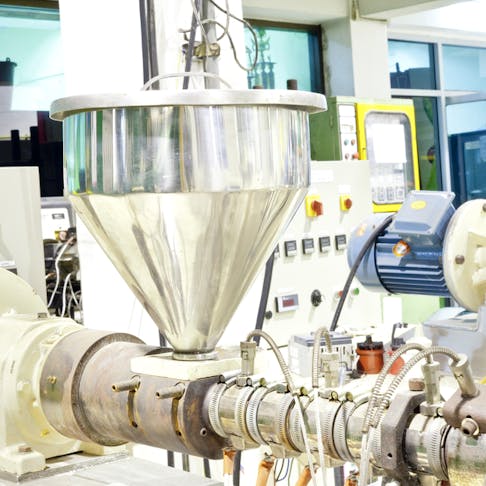
Extrusion Molding: Definition, How It Works, Applications, and Advantages
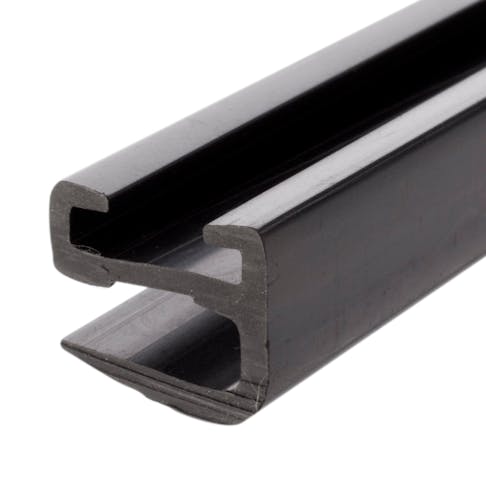
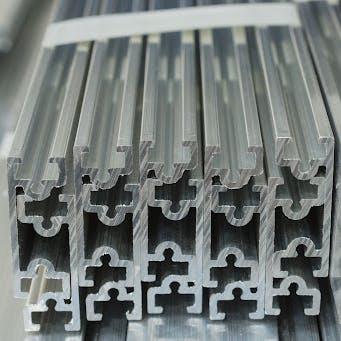